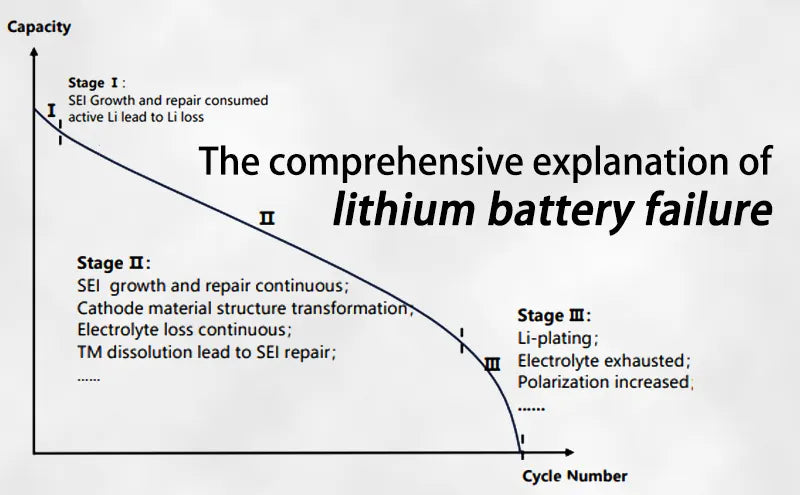
Main content:
Cycle life is one of the core indicators of lithium-ion batteries, and a longer cycle life means that the battery can handle more repeated charges and discharges. However, the number of cycles is limited after all, lithium battery failure can only be reduced and is inevitable.
Therefore, it is of great value to find out the cause of lithium battery failure and improve the cycle life of lithium batteries. Lithium battery failure is related to many factors, such as materials, processes, manufacturing processes, and use environments.
1. Basic principles of lithium battery failure
Although lithium-ion batteries are secondary rechargeable batteries, the number of charge and discharge times is limited. The discharge capacity of the lifepo4 batteries will gradually decay with the increase of the number of cycles, and when it reaches a certain extent, it loses its usefulness.
Find the factors that cause lithium batteries to fail and determine the extent of their impact, so as to improve battery life in a targeted manner. Through the failure analysis of lithium batteries, the weak points affecting the cell cycle are continuously improved, so that the cycle life can be continuously improved.
The main factor affecting the cycle performance of the battery is material failure. Lithium battery failure modes can be broken down into power loss due to increased impedance and loss of capacity due to loss of active lithium.
● Power loss
Power loss is reversible, also known as polarization loss, and capacity can be restored when a small current is discharged.
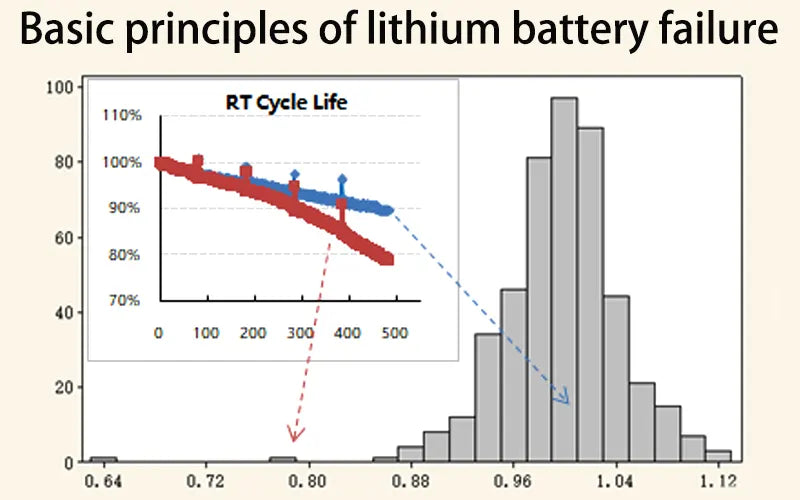
● Active lithium loss
Active lithium loss (li loss) is irreversible and capacity cannot be restored even with a small discharge of current. The relationship between the causes and consequences of lithium battery failure is very complex, and lithium battery technology is not completely clear.
2. Lithium battery material composition
As mentioned earlier, the root cause of lithium battery failure is material failure. To this end, we have listed materials that have a greater or smaller impact on the cycle performance life of lithium batteries.
Among all materials, the four main materials of lithium batteries are cathode active materials, anode active substances, separators, and electrolytes. Their weight and cost account for about 80% of the total battery, which is the most important part of the battery.
3. Four main materials and lithium battery failure
Lithium cobalt oxide (LiCoO2) is the most commonly used cathode active material, and its capacity decay is often attributed to poor structural stability at high voltages, which hinders the embedding and removal of Li+ after long cycling.
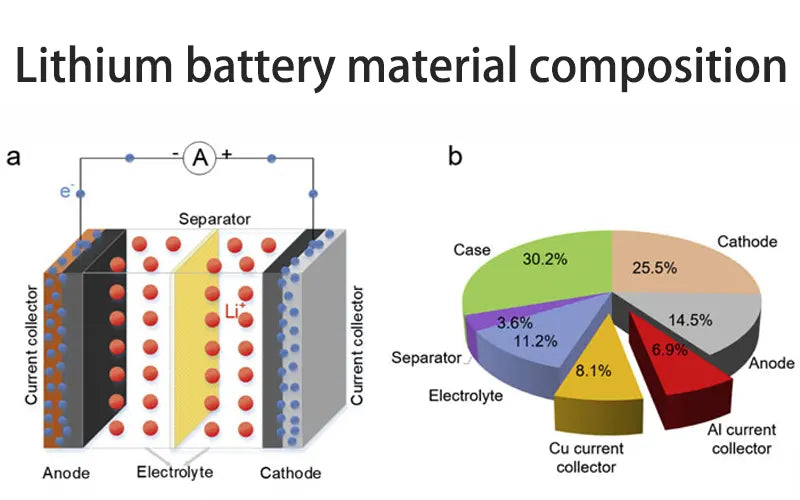
The cause of failure of anode materials is usually the overgrowth of SEI films. Usually, during normal battery use, the problem of continuous solvent reduction reaction is inevitable, so the stability of SEI is crucial. In addition, the use of auxiliary materials will also affect the cycle performance of lithium batteries to a certain extent, they are:
- Binder failure causes electrode pulverization.
- Insufficient CMC dosage leads to slurry settlement and uneven electrode coating.
- Agglomeration of conductive agents leads to a decrease in the utilization rate of certain active substances.
- Local breakdown of the current collector leads to an increase in impedance.
- The dissolution of the adhesive paper in the electrolyte causes the cell to leak virtually.
- Insufficient overcurrent design leads to excessive local temperature rise and uneven distribution of current density.
- Insufficient adhesion of the separator coating layer leads to electrode deformation and increased contact impedance.
- Corrosion of aluminum plastic film causes water vapor to enter the inside of the battery.
4. External cause analysis
A basic principle of lithium battery failure analysis is: from "external" to "internal", that is, the external problems of the battery cell must be analyzed first. For example, check whether the cell cycle test step is correct, test the actual voltage and current.
And whether there is continuity, whether abnormal power outages or artificial movements have occurred. It is also necessary to test whether there is a foreign object in contact between the clip and the tab, and whether the electrical contact is good.
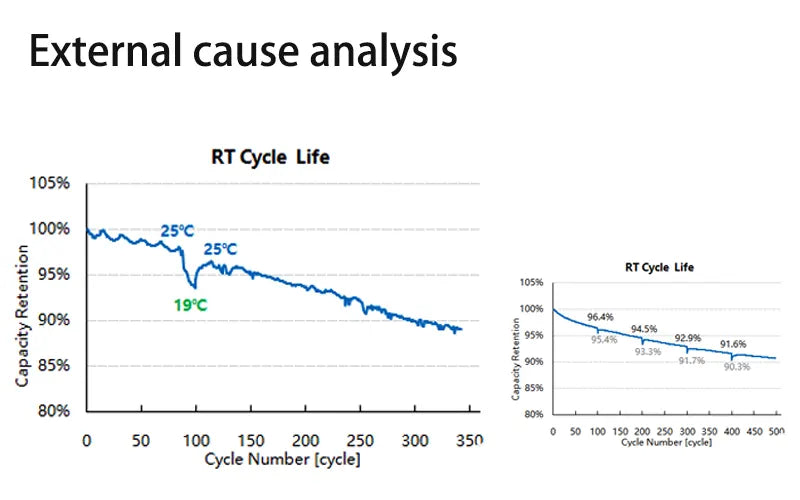
The enlightenment of the external factors investigation is that under the premise of the correct test process, we must ensure the continuity and stability of the test process, otherwise it may cause abnormal attenuation of the lithium battery failure.
5. Full cell analysis
Another basic principle of failure analysis of lithium batteries is full cell to half cell. Generally, lithium batteries include cathode materials (LCO, NCM, LFP, LMO, etc.) and anode materials (Gr, Si, LTO, etc.), which are called "full cell" and are also the standard combination form of commercial lithium batteries.
The full battery analysis mainly includes the following:
① Capacity attenuation source
For small current charge and discharge tests for lithium battery failure, it is generally believed that when the current density is small enough, the polarization effect can be ignored.
In this case, irreversible loss capacity accounts for a relatively large proportion, and the improvement direction should focus on improving irreversible loss capacity.
② Full cell impedance contrast
Lithium battery failure and fresh battery testing found that ohmic impedance is not much different. The sources of impedance increase were mainly membrane impedance and charge transfer impedance.
And it is indicating that li+ resistance to electrochemical reaction through SEI increased, and the electrochemical reaction rate slowed. Battery companies like top 10 lithium battery companies in the world should gradually accumulate cyclic fault analysis databases, which will help solve problems faster, more efficiently, and more economically.
③ Liquid preservation
Before disassembling the battery, the circulating cells should also undergo a rehydration cycle to verify the effect of liquid retention on cycle performance. In general, for pouch batteries, care must be taken to maintain a closed environment inside the cell.
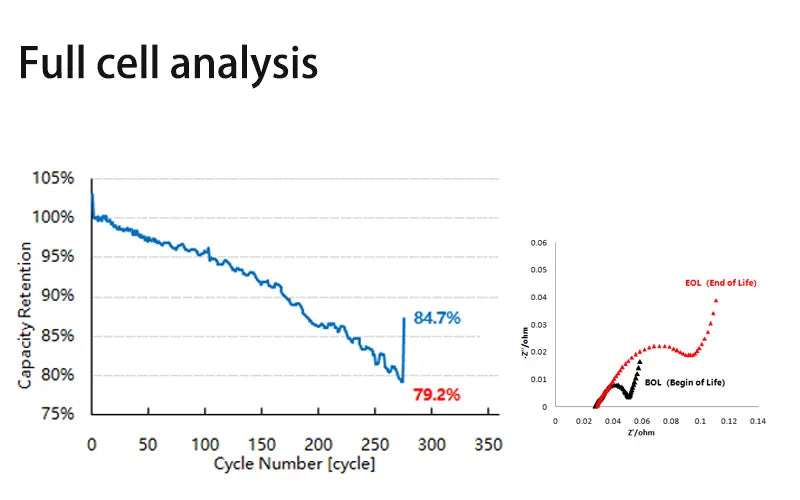
Rapid diving in the later stages of the cycle, followed by rehydration. After the second infiltration, the cycle can be restarted, and the cycle trend can be restored as before, indicating that the main reason for cyclic diving is electrolyte exhaustion.
The capacity decay of the battery in the early stage is fast, and then the cycle curve is gradually flattened. The rehydration operation was then carried out, and the circulation trend remained unchanged after secondary infiltration, indicating that the amount of liquid retention was not the main cause of capacity decay.
6. Half cell analysis
Anode is a lithium metal sheet, and cathode is the button cell of the material to be analyzed, called the "half cell". Compared to full cell, half cell allow the study of single materials. Such as cathode and anode materials, separators, etc., are an important part of lithium battery failure analysis.
Before assembling the half cell, the disassembled electrode piece is made on one side: one side of the electrode piece is erased with a solvent (NMP for the anode, water for the cathode). The purpose of baking is to remove moisture from the electrode, the purpose of punching is to facilitate assembly, and the purpose of weighing is to calculate the test current and gram capacity.
If low pressure is present, the possible reasons are:
- The pole burr pierces the separator, causing a short circuit.
- The electrode and the lithium plates are not placed in the center region of the separator, resulting in a short circuit.
- The assembly is not compact enough, resulting in a large contact impedance.
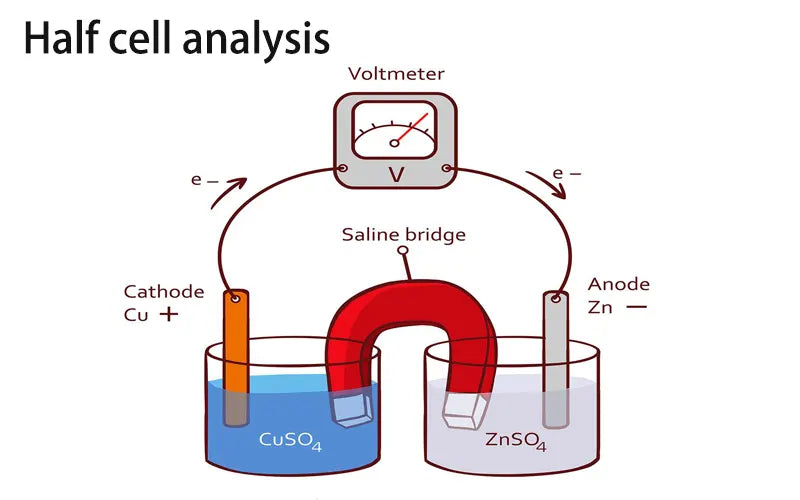
For the analysis of the impedance source of the entire battery, both the three-electrode technique and half-cell analysis can be used. Three-electrode technology enables in-situ detection without damaging cells.
At the same time, it can also monitor potential changes, which is more powerful. However, half cell can quantitatively analyze the loss of material capacity before and after the cycle. Moreover, it is still one of the technologies that cannot be ignored for lithium battery failure analysis.
7. Conclusion
Lithium battery failure is related to many factors, such as materials, processes, and the environment, and should be followed in analyzing the problem according to the details. Finding out the reversible battery capacity loss and the irreversible sources, so as to make targeted improvements.
Lithium battery failure analysis is not an independent activity, but a systematic one. The companies should take some actions like make forward verification data, material evaluation, fault cause analysis.
Related articles: swollen battery, cathode and anode, top 10 power battery recycling companies