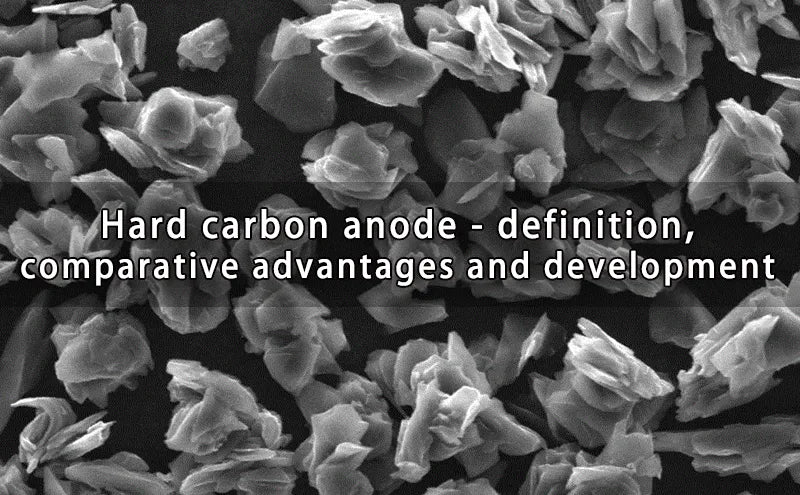
Main content:
At present, the anode materials for sodium-ion batteries mainly include tin-based, antimony-based, phosphorus, titanium dioxide, and hard carbon anode. Among them, the materials of conversion reaction and alloy reaction have the problems of serious volume expansion and poor conductivity; titanium dioxide faces the problem of low capacity.
Therefore, among many anode materials, hard carbon anode has the advantages of abundant reserves, low cost, good electrical conductivity, high sodium storage capacity, environmental friendliness, and low redox potential. It is considered to be the anode material for sodium-ion batteries that is most likely to be the first to realize industrialization.
1. What is a hard carbon anode?
The hard carbon anode refers to non-graphitizable carbon, which is pyrolytic carbon of high molecular polymer. Hard carbon anode can be obtained by pyrolyzing a cross-linked resin with a special structure at about 1000°C. This type of hard carbon anode is mainly composed of single-layer graphite, and these graphite layers are interlaced to form micropores with small pore size and opening.
This type of carbon is also difficult to graphitize at high temperatures above 2500°C. Common hard carbons include resin carbon (such as phenolic resin, epoxy resin and polyfurfuryl alcohol PFA-C, etc.), organic polymer pyrolytic carbon (such as PFA, PVC, PVDF and PAN, etc.) and carbon black (B group black), etc. Studies have found that hard carbon anode materials have high reversible specific capacity.
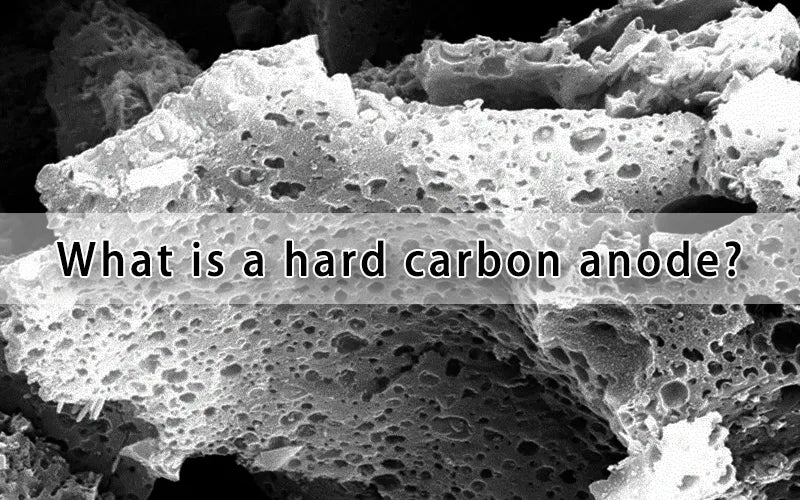
Among them, the capacity of polyfurfuryl alcohol resin carbon PFAC can reach 400mAh/g. The specific capacity of hard carbon obtained by pyrolysis of sulfur-containing polymer is 500mAh/g. The specific capacity of hard carbon anode obtained by pyrolysis of polyphenol is 580mAh/g, and the specific capacity of hard carbon obtained by pyrolysis of pitch, PVC, polyparaphenylene (PPP) and epoxy phenolic resin is greater than 700mAh/g.
2. Compared with soft carbon, why choose hard carbon anode?
Hard carbon anode materials have the advantages of diverse structures, low price, good conductivity, high sodium storage capacity, small volume deformation after sodium intercalation, environmental friendliness, and low redox potential. As far as the hard carbon anode is concerned, compared with the ordered layered structure of graphite, its structure at the molecular level is more complex, and the relatively disordered structure is more conducive to sodium storage. The interlayer spacing of soft carbon is smaller than that of hard carbon.
As far as soft carbon is concerned, although it has a similar structure to graphite, it has a lower degree of order. Compared with graphite, it is more conducive to intercalation and storage of sodium, and can increase the specific capacity at low current density. . The specific surface area and surface defects of soft carbon are low, which can reduce the consumption of ester electrolyte. From the perspective of commercialization, the soft carbon precursor is fired with cheaper anthracite coal, which has low price, high carbonization yield, good safety and certain electrochemical performance, and has good commercialization potential. Soft carbon has insufficient capacity.
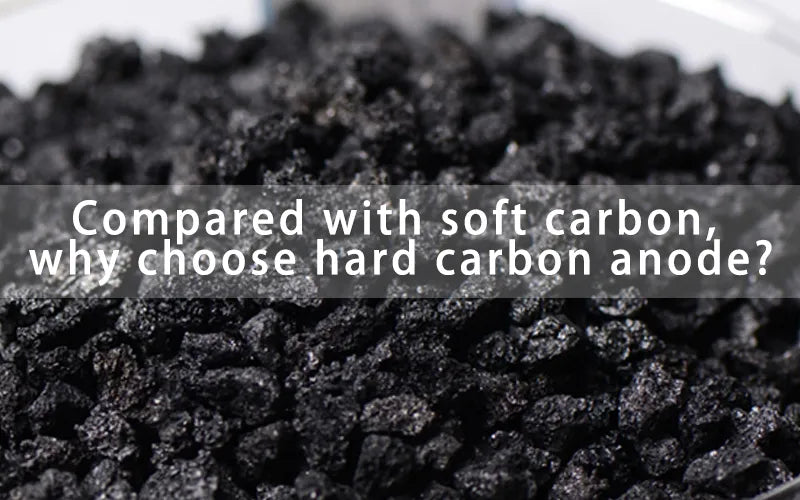
Although the cost is lower than that of hard carbon anode, it has a lower sodium storage capacity due to its graphitized structure. Although the capacity can be increased through the pore-making process, it will increase the cost, but it is not as economical as hard carbon, and it is not as good as hard carbon anode in terms of low-temperature performance and fast charging performance. Hard carbon has many nanopores, high sodium storage capacity, low compaction density, and high mechanical hardness. Due to its structural characteristics of large interlayer spacing, many nanopores, and many defect sites, it can store more sodium ions.
To sum up, in the field of sodium-ion battery applications, from the perspective of the selection of anode materials, most major sodium-ion battery companies in the world choose hard carbon materials as battery anodes, and hard carbon anode materials have also been researched and put into application by many companies.
3. Problems facing the development of hard carbon anode
Hard carbon anode is currently the mainstream anode material route for sodium batteries, and it is also the main constraint factor for the scale-up of the current sodium battery industry. The main reasons are as follows:
- The production capacity of hard carbon anode in China is limited, only in the order of several thousand tons in total, and the products rely on imports.
- The electrode potential and first-cycle Coulombic efficiency are low, and the cycle stability and rate are poor. These factors seriously hinder the industrial application of hard carbon anode materials.
- Research on hard carbon structure needs to be deepened.
A well-performing hard carbon anode needs to have a low external surface area to minimize irreversible charge loss during the first cycle and a high concentration of internal micropores to maximize specific charge storage. The existing methods are still uncertain and difficult to study the structure of hard carbon, which hinders the exploration of the sodium storage mechanism of hard carbon to a certain extent, and further affects the application of hard carbon in the industrialization of sodium-ion batteries.
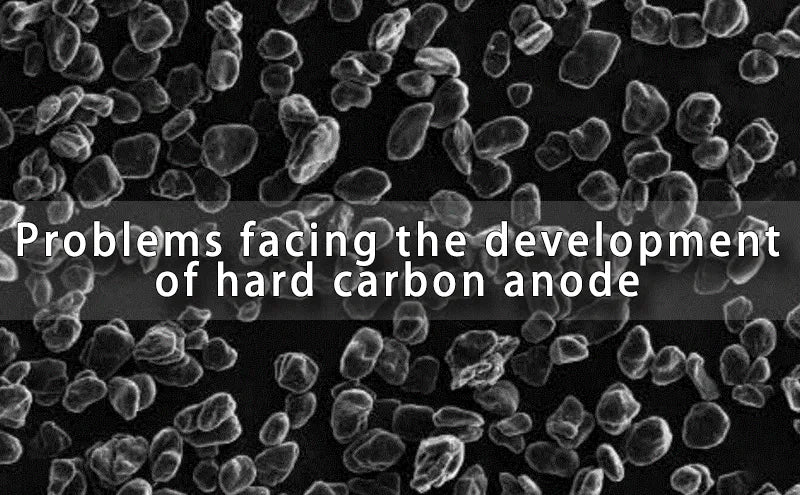
- There are defects in the precursor of hard carbon anode materials, and the process is complicated, resulting in high cost.
The structure of hard carbon anode materials depends on the state of the precursor and the corresponding carbonization process. Hard carbon anode precursor materials are complex and diverse, including biomass, resin base, pitch, etc. The hard carbon products obtained from different precursors have significant performance differences, and the source of raw materials is different, and the cost structure is also significantly different.
From the perspective of various technical routes, the hard carbon produced by the biomass-based route has moderate performance, a wide range of material sources, and a relatively reasonable cost. It is currently the choice of major manufacturers. However, it is still difficult to find cheap precursor materials suitable for mass production, which is still one of the bottlenecks limiting its commercial application. The synthesis process of hard carbon negative electrode is relatively complicated, which greatly increases the manufacturing cost of hard carbon, affects large-scale production, and limits the industrialization of hard carbon in the field of sodium-ion batteries.
4. How hard carbon anode breaks through the current dilemma
First of all, based on the understanding of the hard carbon sodium storage mechanism, the strategies for improving the sodium storage performance of hard carbon anode materials should mainly focus on the following aspects:
- Microscopically control the pore structure and interlayer spacing of hard carbon by regulating the synthesis of precursors and the pyrolysis process;
- Coating and compounding with other materials, heteroatom doping, etc. to control the defect degree and layer spacing of materials;
- Electrolyte regulation and pre-sodium treatment. Electrolyte regulation can improve the electrochemical performance and rate performance of hard carbon anode materials, which requires cooperation between battery manufacturers and electrolyte manufacturers for research and development, and is expected to be industrialized soon.

Secondly, in view of the high cost, although biomass precursors are a good choice for the transition period, in the long run, it is still necessary to continuously improve the research and development technology of asphalt-based negative electrode materials to achieve cost reduction of asphalt-based and resin-based materials, so that their scale application.
At the same time, in terms of hard carbon anode processing, since some production equipment still relies on imports, research and development of equipment that adapts to the production lines of various anode manufacturers is the key to cost reduction, and self-development of non-standard equipment is still required.
Related articles: lithium vs sodium battery, sodium battery electrolyte suppliers, anode materials