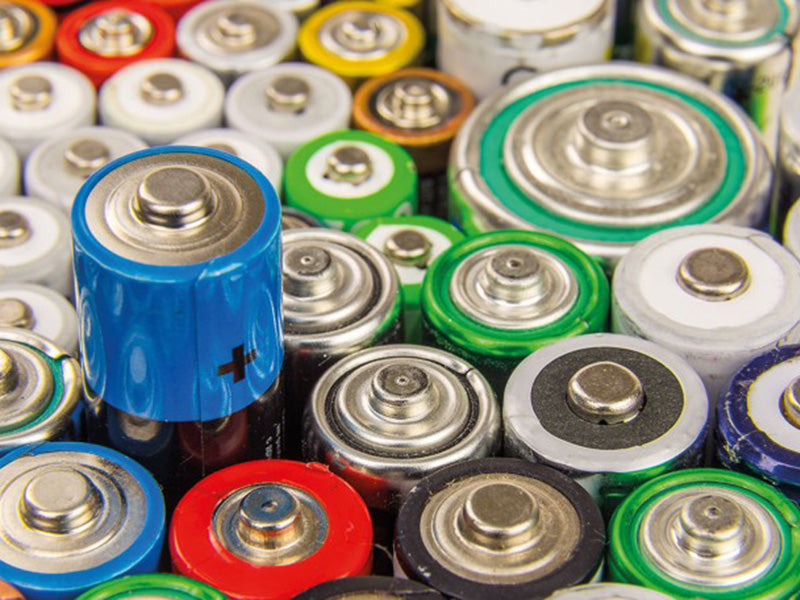
1.Current status of cathode materials
Compounds with polyanionic structures have great potential to replace lithium oxides such as LiCoO2.
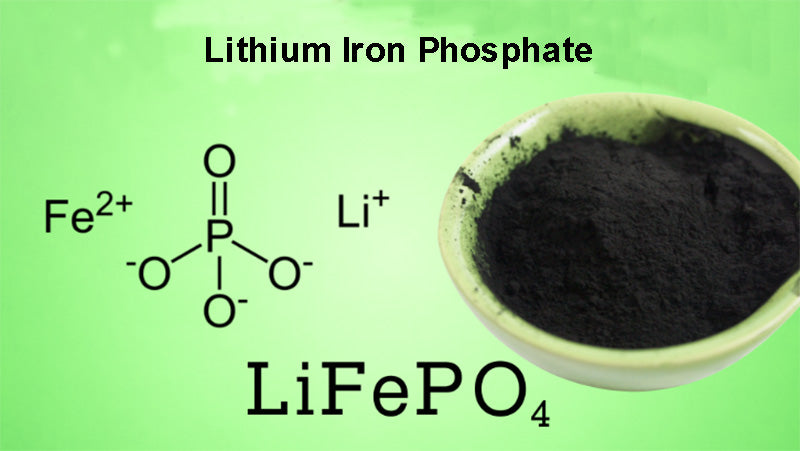
Among these cathode materials, the most successful application is lithium iron phosphate (LiFePO4). At present, Phostech has carried out commercial application, and some other companies such as Valence technology, A123 Systems, and several companies in China have used it in batteries. These cathode materials are essentially an insulator, and changing its properties has been a focus of research in the industry. The theoretical capacity density of lithium iron phosphate is 170 mA·h/g, and the voltage relative to Li+/Li is 3.45 V. The reversible specific capacity of the battery system composed of LiFePO4/C as the cathode materials can reach 160 mA·h/g. The main advantage of the polyanionic structure compound is its performance stability at high temperature, which makes it suitable for the fabrication of large-capacity and high-safety lithium-ion batteries.
2.Mid-term development of cathode materials
Among the cathode materials that can replace lithium cobalt oxide LiCoO2 (which is currently used in almost all lithium-ion batteries) and its derivatives, high-potential intercalation cathode materials such as olivine structure oxides (such as LiNi0.5Mn1.5O4) and spinel-structured materials such as LiCoPO4 which have the potential to further increase the energy density. The new layered oxides Li1+x(Mn,M)1-xO2(M=Ni、Co, etc.) can also provide higher capacity due to their high charge-off voltage (4.5~5V for Li+/Li).

In practical applications, the use of these cathode materials presents the problem of the electrolyte reacting with the electrodes in contact at high potentials, resulting in high self-discharge rates (up to 80% per month). However, if we refer to the calculated values from ab initio calculations (the voltage against Li+/Li reaches 5.5V, higher for EC, PC, DMC), the solvents used in the electrolytes of Li-ion batteries have inherently high Oxidative stability. Here, EC (Ethylene Carbonate) is ethylene carbonate, PC (Propylene Carbonate) is propylene carbonate, and DMC (Dimethyl Carbonate) is dimethyl carbonate.
However, as described by Kanamura et al. in their paper for PC-based electrolytes (relative Li+/Li voltage varies between 5 and 4.2 V), the actual measured limiting potential valuevary widely, and when the measured electrodes are based on Potential values are always lower for active cathode materials. This apparent difference may be due to several factors: the "catalytic" effect of the inserted cathode materials, traces of water, and the effect of the lithium salt used. In some cases, the decomposition of the electrolyte is accompanied by the formation of a solid film on the anode surface.
Taking the research of anode materials, especially graphite, by introducing additives into the electrolyte to create a stable solid electrolyte interface (SEI) seems promising to eliminate the above phenomenon. This method is not yet widely used, but Japan's Ube Industries is tracking. The purpose is to reflect the problem through the control interface and realize the reduction of the self-discharge rate.
High-voltage electrode materials have been studied for many years, but there is still no reliable technical solution. There seems to be more room for innovation in how to make electrolytes stable under high pressure than in the search for active cathode materials.
Among the solutions mentioned in the literature to reduce the effect of the electrode/electrolyte interface reaction, there is a method to produce an electrochemically inert inorganic compound precipitation (such as Al2O3,AlPO4,TiO2,ZrO2 Passivation films can avoid high Oxidative loss of the inserted cathode materials in the state of charge (a problem often encountered with layered oxides), but does not protect the cathode materials as a whole, which is vis-a-vis electrolyte oxidation. In other words, For the protection of high-potential electrodes, only external measures are not an effective solution.
Therefore, the protection of cathode materials should be done in situ, by employing organic compounds dissolved in conventional electrolytes (such as LiPF6 in EC/PC/DMC) to achieve overall protection of cathode materials. The oxide additives employed should allow the precipitation of electrolyte-insoluble passive films, which should occur at lower potentials than electrolyte oxidation. In order to keep the electrochemical performance of Li-ion batteries (such as charge-discharge speed and internal resistance, etc.) unaffected, the film formed on the electrode surface should have sufficient Li+ conductivity. The use of additives should not cause electrochemical instability of the negative electrode, such as affecting the formation of a passivation film on the negative electrode.
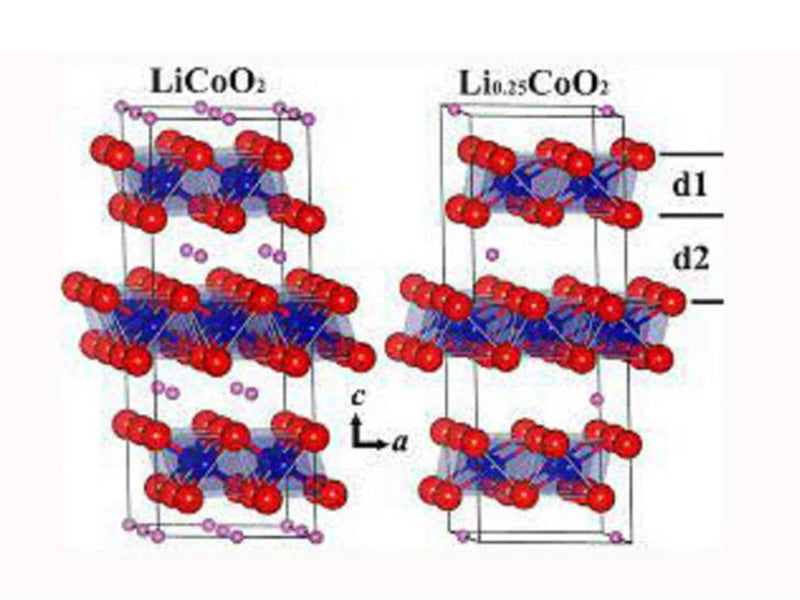
The literature on cathode materials protection is limited to common electrodes such as LiCoO2. LiCoO2 has improved its cycle performance by using trimethylpentane, phenyladamantane, phenylcyclohexane, and biphenyl or triphenyl. The most studied compound, biphenyl, has an oxidation potential of 4.45V for Li+/Li. In order to obtain a film that covers but does not prevent the movement of Li+ ions, the amount of biphenyl added to the electrolyte needs to be optimally configured. These additives are used to aggregate and block the battery when the battery is overcharged.
Globally, companies such as Sanyo, SDI and LGC are currently developing this high-voltage cathode materials.
Read more: Focus on Lithium-ion Battery Technology