main content:
1. Battery thermal management performance requirements and classification
Battery thermal management is based on the influence of temperature on battery performance, combined with the electrochemical characteristics and heat generation mechanism of the battery, based on the optimal charge and discharge temperature range of a specific battery, covering materials science, electrochemistry, heat transfer, molecular dynamics and other disciplines Background, in order to solve the problem of heat dissipation or thermal runaway caused by the battery working under the condition of too high or too low temperature, and improve the overall performance of the battery. With the increasing demand for battery power performance in power systems such as electric vehicles, the need for battery thermal management is becoming more and more urgent. Based on the above analysis, the problems caused by the temperature of the electric vehicle power battery system mainly include the following three aspects.
(1) When the battery is operated in a high temperature environment, the heat dissipation is not timely and the high temperature formed by the rapid accumulation of heat generated during high current discharge will reduce the battery cycle performance, and even cause direct damage to the battery such as combustion and explosion. Safety problems.
(2) Unbalanced heat production of battery cells, unbalanced temperature distribution among the cells of the battery module, and unbalanced temperature distribution among the modules and between the cells of the entire battery pack of an electric vehicle will reduce the overall life of the battery pack and affect the Vehicle power performance and life.
(3) The cold start efficiency of batteries in low temperature environment is low, and the depth of battery discharge does not match the power performance of electric vehicles, which restricts the application and development of electric vehicles in alpine regions and winter.
The improvement of electric vehicle battery power performance and cycle life puts forward the following requirements for the battery thermal management system.
(1) Ensure the most suitable working temperature range of the single cell, avoid the overall or local temperature of the single cell, battery module and battery pack being too high, so that the battery can effectively dissipate heat in a high temperature environment, and quickly heat or keep warm in a low temperature environment.
(2) Reduce the temperature difference between different parts inside the single battery, especially the large-sized single battery, and ensure the uniform temperature distribution of the single battery.
(3) Reduce the temperature difference between different battery modules inside the battery pack to ensure uniform temperature distribution inside the battery pack as a whole.
(4) It meets the specific requirements of electric vehicle light weight and compactness, and is easy to install and maintain, with good reliability and low cost.
(5) Effective ventilation when harmful gases are generated, and thermal measurement and monitoring consistent with temperature and other related parameters.
Work related to battery thermal management was first seen in the 1980s, but before 1998, due to the widespread use of batteries in miniaturized devices, little work was reported on battery thermal management. After 1999, the thermal problem of power batteries became increasingly prominent, and the work related to battery thermal management began to be systematic. The National Renewable Energy Laboratory (NREL) and the Illinois Institute of Technology (IIT) both take the research of battery thermal management as one of the key directions. In 2001, based on IIT's battery thermal management technology, Al-Hallaj and Selman established AllCell, which specializes in providing battery thermal management solutions for various electric vehicles. After more than ten years of development, battery thermal management has mainly formed the following technologies.
(1) Research on temperature-resistant battery materials based on battery structure, including high-temperature-resistant materials, low-temperature electrode materials, electrolyte materials, etc.
(2) The battery thermal management system using air as the medium.
(3) Battery thermal management system with liquid as medium.
(4) Thermal management of batteries based on phase change heat transfer media/materials.
(5) Heat pipes, thermoelectrics, cold plates and other thermal management systems based on the principle of cooling and heating.
(6) Coupling of the above two or more ways.
2. Thermal control based on temperature-resistant battery materials
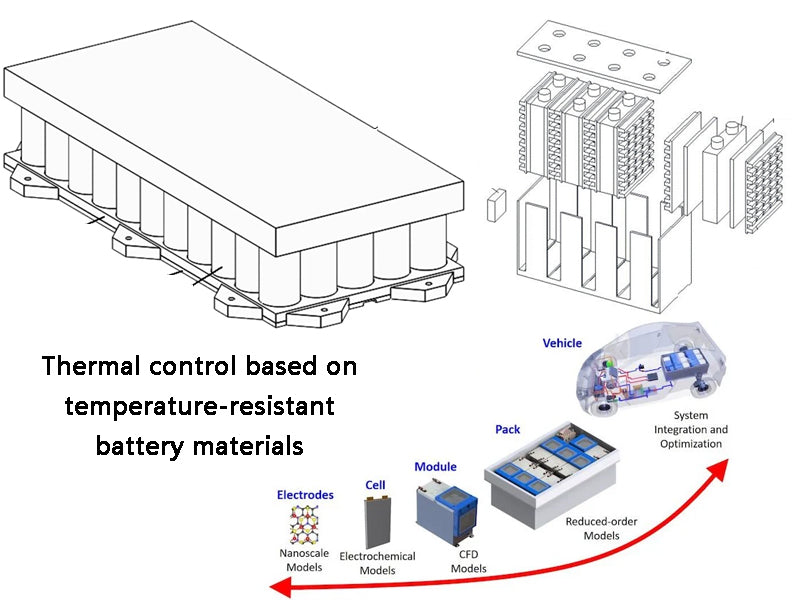
The thermal control of battery temperature-resistant materials mainly includes the modification of positive electrode materials, negative electrode materials, electrolytes, etc., to improve their high temperature resistance performance or low temperature activity. Kise et al. synthesized a positive temperature coefficient compound using carbon/polymer as raw material, and used it as the negative electrode material of Lon battery to prevent internal short circuit of the battery and improve the high temperature safety of the battery. Yoshizawa et al. synthesized a magnesium lithium cobalt oxide and made a Li-ion battery for testing. The results showed that the battery was discharged at 1C at 0, -10 °C, and -20 °C, and the discharge capacity was 84% and 23 °C, respectively. 63% and 33%, the capacity can still maintain 95% after the battery is put aside at 100 ℃ for 5h, and the thermal stability of the battery increases with the charging capacity. Wang and Sun used 4-isopropyl phenyl diphenyl phosphate (IPPP) as additive and tested the thermal performance of LiCoO2/IPPP electrolyte/C battery. 5% and 10% can improve battery safety performance. Arai et al. synthesized Li2DFB, which was charged and discharged at 60 °C. Li2DFB showed better thermal stability and cycle performance than LiPF6 batteries. Although pure LiPF6 materials showed better stability at 180 °C, LiPF6 batteries showed better stability. The thermal stability displayed at 60~85℃ is relatively poor. Li2Ti3O7 battery has higher charge-discharge capacity than room temperature at 40℃ and 50℃, but when the temperature rises to 70℃, its battery performance deteriorates rapidly. Ma and Noguchit made Li2Ti3O7 at 70℃ by doping Fe. Case stability is improved. It is not difficult to see that for Liio batteries, the flame retardant of the electrolyte is the key. Adding flame retardants to the original electrolyte and researching new non-combustible or low-flame electrolytes can improve the thermal stability of Liio batteries and reduce the risk of battery combustion. Useful ways.
For electrode materials, the main purpose is to improve its thermal conductivity, speed up the transfer rate of heat inside the battery to the external space, and reduce the accumulation of heat inside the battery. Zahran investigated the thermal conductivity enhancement of carbon electrodes by adding copper and aluminum. Maleki et al. studied the thermal conductivity of Li-ion batteries made of graphite, polyvinylidene difluoride (PVDF), carbon black (carbon-black, C-black) and other negative materials synthesized. The results show that the battery's thermal conductivity The thermal conductivity is related to the graphite size, PVDF and C-black content. When the PVDF content increases from 10% to 15%, the thermal conductivity increases by 11%~13%.
The improvement of thermal stability of electrode materials and electrolyte materials is based on the premise of sacrificing battery capacity. The research conducted by Kohno et al. on Li-ion batteries for HEV showed that although the power coefficient of the battery reached 3800 W·kg-1 at 25 °C, and the battery was left at 80 °C for 20,000 h without leakage of electrolyte, they also pointed out that its The problem of battery storage in a high temperature environment for a long time is still an urgent problem to be solved. From the perspective of heat transfer, the increase in thermal conductivity (such as about 10%) has little effect on the heat dissipation of the battery. If high thermal conductivity particles such as copper and aluminum are added instead, the battery capacity will be directly reduced. group, to ensure that battery capacity and power performance are parallel indicators. Therefore, the method of accelerating the heat diffusion and control of the battery by improving the battery material also has a certain limit, and the thermal management of the power battery by air, liquid, phase change materials, etc. will be a more effective way.
3. Air-based battery thermal management system
Heat transfer media have a significant impact on the performance and cost of thermal management systems. Using air as the heat transfer medium is to directly introduce air into the module to achieve the purpose of thermal management. Figure 1 shows the principle when air is used as a medium to cool or heat a battery.
Figure 1 Air cooling or heating principle
Thermal management systems that use air to heat, cool (or ventilate) the battery can be passive (uses only the surrounding environment) or active (built into the system to provide a source of heat at low temperatures or at high temperatures) cold source), while active elements include evaporators, heating cores, electric heaters, or fuel heaters. In a high temperature environment, the electric vehicle battery only needs to be cooled without heating it; on the contrary, in a cold environment (the temperature is about -10 ° C or below), the energy and power of most batteries are very low, and the performance of the vehicle is serious. recession, which requires the use of a heating system to ensure proper operation. For EVs, since there is no engine to heat the battery pack, the heat emitted by the motor and the heat generated by the more powerful in-vehicle electronics can be utilized. For HEV, the engine can provide a heat source, but it must pass a certain time delay (more than 5 minutes) to heat the battery to the ideal working temperature, so it is necessary to add a corresponding heating device to the battery. Relatively speaking, it is much easier to cool the battery than to heat it, because it can be cooled by the vehicle air conditioning, refrigeration system or engine cooling medium. However, the use of cooling technology leads to an increase in battery energy consumption, which contradicts the use of hybrid technology to improve its energy economy. Today's scholars have analyzed the heat dissipation characteristics of the battery through simulation and experimental research, and verified the feasibility of forced air cooling. However, with the wide application of the air cooling method, for large-scale lithium-ion polymer batteries, due to its low thermal conductivity, The relaxation time of heat conduction is long, and air cooling alone cannot meet the requirements.
4. Liquid-based battery thermal management system
For heating under cold conditions, air is generally used as the medium to meet the requirements, but under complex conditions such as high temperature, the power battery heat dissipation has higher requirements, and it is possible to use liquid as the cooling medium for power battery heat dissipation. Liquid cooling systems are mainly divided into active liquid cooling systems and passive liquid cooling systems. In the active liquid cooling system, the vehicle's own refrigeration device is used, and the heat of the battery is sent out through the exchange of liquid and liquid; in the passive liquid cooling system, the heat of the battery is sent out by the heat exchange between the liquid and the outside air. Heat transfer using a liquid medium can be performed by piping between modules, or by arranging jackets around the modules, or by immersing the modules in a dielectric liquid, or by placing the modules directly in a heating (or cooling) liquid. If the liquid is not in direct contact with the module (such as heat transfer tubes, jackets, etc.), the heat transfer medium can be water, ethylene glycol or even refrigerant. If the module is to be immersed in a heat transfer liquid, the liquid must be dielectric and insulated to avoid short circuits. The rate of heat transfer between the module walls and the heat transfer medium depends on the liquid's thermal conductivity, viscosity, density, and flow rate, among others. At the same flow rate, the heat transfer rate of most direct contact fluids (such as mineral oil) is much higher than that of air, because the latter has a thinner boundary layer and higher thermal conductivity. However, due to the high viscosity of oil, high pumping power is required, and only a low flow rate can be used, so that its heat transfer coefficient is only 1.5 to 3 times higher than that of air. At present, liquid cooling has been widely used in many fields such as heat dissipation of electronic equipment and cooling of Ni-MH battery packs.
5. Battery thermal management system based on phase change heat transfer medium
Phase change material (PCM) refers to a substance that changes shape with temperature change and can provide latent heat. The process of the phase change material from solid to liquid or from liquid to solid is called the phase change process, at this time the phase change material will absorb or release a large amount of latent heat. Phase change materials can be divided into organic and inorganic phase change materials, as well as hydrated phase change materials and paraffin wax phase change materials. At present, phase change energy storage materials have been applied in many fields, such as the space field as a thermal protection system. Active or passive cooling systems and heat dissipation of electronic devices in electronic devices and energy storage devices, whether from the perspective of energy saving, improving vehicle cruising range, or from the miniaturization and miniaturization trend of vehicles, traditional air and water cooling. The thermal management system of the medium has limitations, and the battery thermal management system using phase change materials is expected to be used.
As shown in Figure 2, when using PCM as the battery thermal management system, the battery pack is immersed in the PCM, the PCM absorbs the heat released by the battery and the temperature decreases rapidly, and the heat is stored in the PCM in the form of phase change heat. The phase transition latent heat and phase transition temperature of PCM are two important reference indicators for selecting PCM. Paraffin waxes have high latent heat of phase transition per unit mass, suitable melting temperature in the battery operating temperature range, and are valuable for large-scale commercial development, but have poor thermal conductivity, low heat storage rate, and can occur during melting/solidification cycles. segregation, thereby reducing overall function. Many researchers have carried out many studies to overcome this defect, for example, adding metal fillers in paraffin to improve thermal conductivity; using metal finned tubes to couple with P℃M; filling PCM in aluminum sheet; filling PCM in graphite To improve thermal conductivity; add carbon fibers or carbon nanotubes to PCM. The findings show that these methods can improve the thermal conductivity and overall performance of PCM to a large extent.
Figure 2 PCM cooling principle