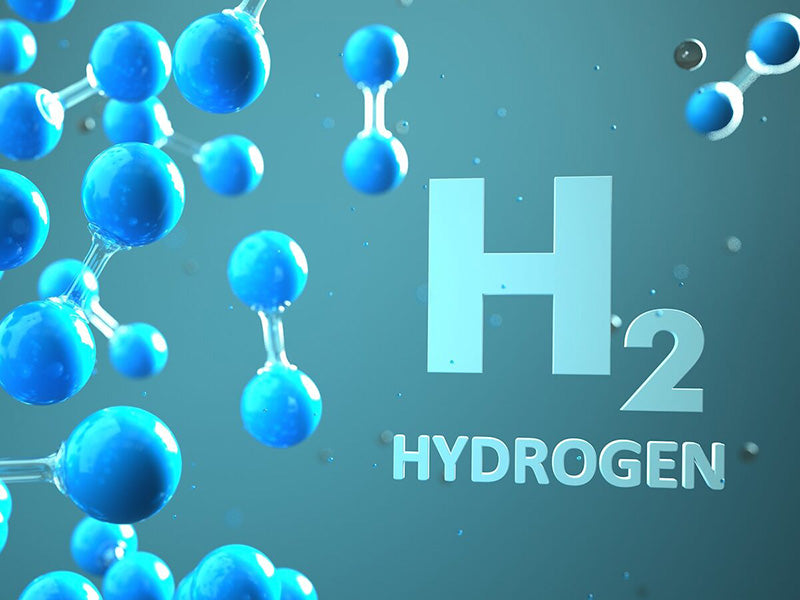
Main content:
1.Low temperature hydrogen storage
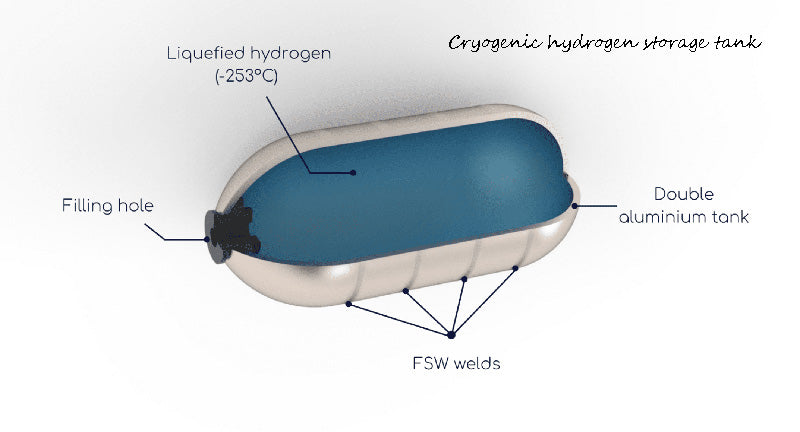
Liquefied hydrogen storage has certain advantages in the process of hydrogen production and distribution, for example, it can be transported by tanker. Even if gasified hydrogen is compressed to 700 bar, its density is not as great as that of liquefied hydrogen. However, efficiency is the most unfavorable constraint for liquefied hydrogen storage, because hydrogen needs to consume energy during liquefaction. Secondly, the evaporation loss of hydrogen during the hydrogen storage process should also be taken into account, and it is estimated that the loss may be 0.1% to 4% per day, depending on the size of the storage and recovery vessel and the specific application form. In terms of safety, the properties of the storage vessel (special steels do not become brittle at low temperatures or in the event of hydrogen permeation) and the handling of cryogenic fluids present certain risks.
1.1 Liquid hydrogen storage for transportation
For liquid hydrogen containers used in transportation, the relevant large European companies recommend the use of metal containers or low temperature boxes with double-wall structure, which are insulated by vacuum or thermal insulation materials (super-insulation, perlite, etc.). The cryogenic container has passed the on-board test. Depending on the model, it carries 5 (for fuel cells) ~ 8 kg (for internal combustion engines) of liquid hydrogen to ensure a driving range of about 300 km.
The original cryogenic hydrogen storage container consisted entirely of metal walls (inner and outer walls) and could weigh up to 150kg; the use of composite materials can greatly reduce the mass of the cryogenic container and is also a better solution for improving vehicle dynamics (smaller volume) . The price of cryogenic vessels is difficult to predict - it should be cheaper with the cheapest insulation and a reduction capture treatment unit that does not account for the evaporation of liquid hydrogen.
An experimental liquid hydrogen distribution station has been built. This type of hydrogen storage requires ancillary equipment and expensive security measures, such as pipe fittings, high-pressure vents, and capture devices for vaporized hydrogen.
1.2 Stationary liquid hydrogen storage
Stationary hydrogen storage is the storage method commonly used by liquid hydrogen distributors. The spherical liquid hydrogen storage device installed by NASA at the Kennedy Space Center in Florida is a typical representative of large-capacity stationary liquefied hydrogen storage, and it is currently the only ultra-large-scale liquid hydrogen storage container for transportation. The spherical container has a diameter of 20m and a volume of 3800m3 and can be loaded with 250t of liquid hydrogen. The measured daily loss is 0.1% to 1% of its capacity. It is not technically difficult to develop such a pressure vessel that can hold 1000t of liquid hydrogen. However, from a safety point of view, especially in Europe, there are no plans to build a plant of this size, even a smaller one, because the consequences of a liquid hydrogen explosion would be catastrophic and quite serious.
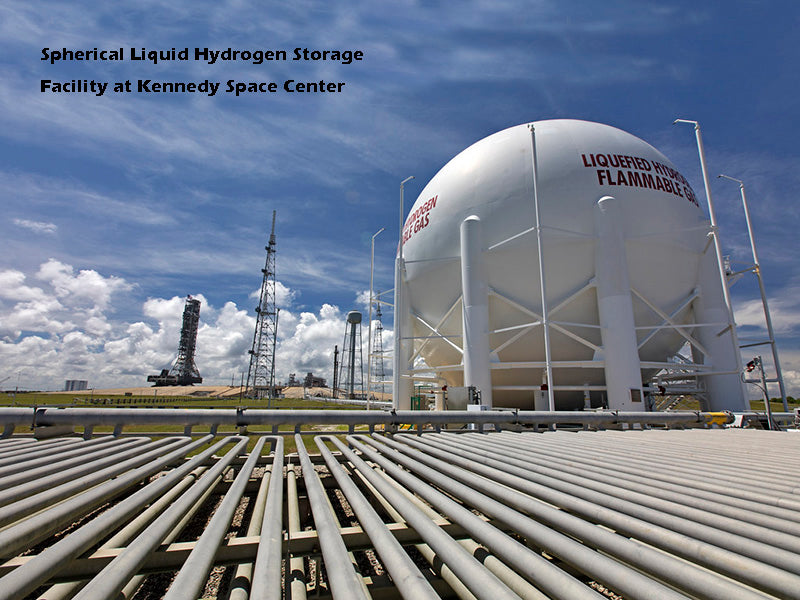
2.Solid-state hydrogen storage
2.1 Physical hydrogen storage by physical (chemical) adsorption
Porous materials (such as activated carbon) can adsorb molecular or atomic gases for hydrogen storage according to the van der Waals principle (VdeW) due to their huge surface area. Below we first describe carbon-based materials and then move on to other types of porous materials suitable for such applications.
2.1.1 Carbon-based porous materials for hydrogen storage
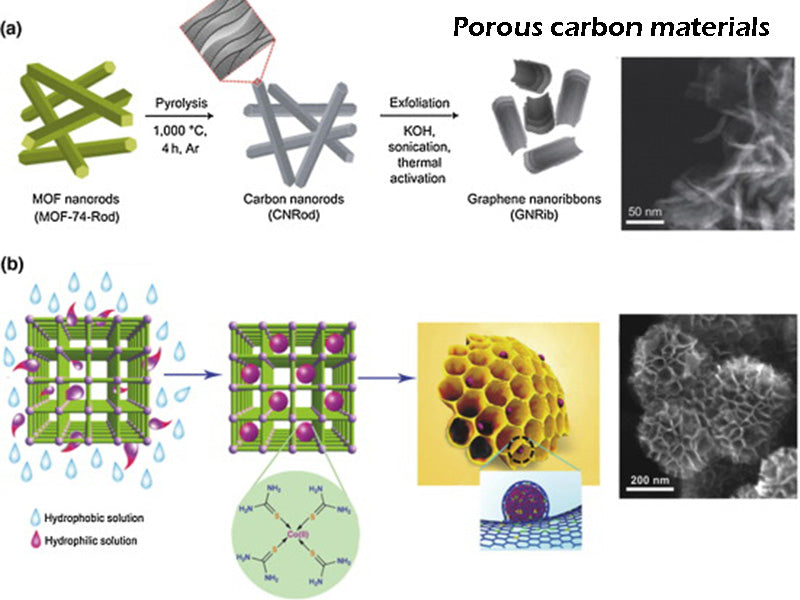
In addition to activated carbon, many other porous carbons and nanostructured carbons have been studied, and are considered to be promising high-performance hydrogen storage materials, some of which are even particularly high (such as fullerenes, nanotube- Single-walled nanotubes or multi-walled nanotubes: SWNTs, MWNTs, "fishbone carbon", cones, etc. There are also materials with a hydrogen storage concentration of 75%). It is necessary to distinguish between intermolecular van der Waals forces and chemical bonds, which are often the driving force for residual stress build-up in metal-containing materials to induce carbon nanostructure growth. Since 2000, the performance index data obtained by related research is relatively modest (especially the data released by metal hydride experts), especially some data at room temperature.
At present, it can be determined that the optimized single-walled carbon nanotube-type carbon nanostructure has the best hydrogen storage performance at room temperature and pressure, and its hydrogen storage density is 1% to 2%. Furthermore, physical bonds do not lead to thermal desorption, which occurs over a wide range of temperatures, even at temperatures higher than ambient. The ultra-high cost of purifying carbon nanostructures remains a major obstacle to the practical application of this hydrogen storage technology.
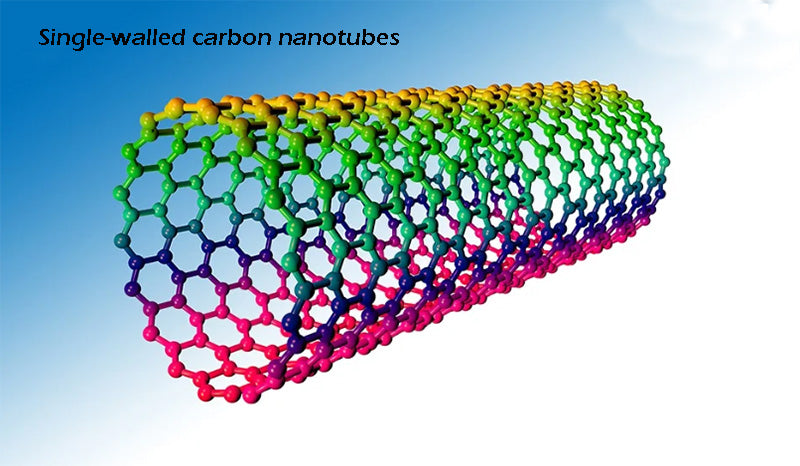
Other nanographite structures with ultra-high porosity (greater than 2000m2/g) with or without catalytic particles are also under development. The porosity of these structures can even be increased by mechanical processes such as ball milling (BM) or mechanical synthesis methods. It has been reported that the hydrogen storage capacity can be increased by 2%~3% at ambient temperature, and at low temperature (such as 77K), its physical adsorption capacity is also very optimistic: at 50bar pressure, more than 7%; at 100bar pressure down to about 10%. This result is interesting because it matches the parameters of compressed hydrogen. Don't forget, though, that these nanographite structures need to be kept at liquid ammonia temperature (to avoid losing the ability to adsorb hydrogen molecules), and must operate under a certain pressure (100 bar). Therefore, the theoretical hydrogen storage energy will be reduced by up to 10%; 2/3 of the reduced energy is used for cooling to 77K, while 1/3 is consumed in hydrogen compression. At the same time, the cryogenic vessel also needs to be heated according to the demand, and the temperature and pressure control system must be added to make the hydrogen storage and hydrogen release process operate normally.
For large-scale applications, the low-temperature hydrogen storage efficiency of carbon nanostructures is lower than that of liquefaction containers, but it has an advantage in the energy consumption of hydrogen storage (about 3 times lower than the loss of liquid hydrogen storage). And safety is also a key factor. The liquefaction vessel shell is subjected to pressure and low temperature, which is difficult to construct. It is necessary to coordinate the design of various parameters to meet the requirements. Of course, the cost of industrial application of activated carbon also needs to be taken into account, which is currently around 70 EUR/kg.
2.1.2 Molecular materials and other physical adsorbents for hydrogen storage
Compared with the previous materials, the effect of ammonium compound nanotubes and other nanostructures on hydrogen storage performance is not outstanding, but the economy is better.
Gels, such as silicone gels, are favored for their low cost. However, due to the limited specific surface area (1000m2/g) restricting the improvement of hydrogen storage performance, related research is still in progress. There is also a certain zeolite-like material, which is low in price and good in thermal robustness. Glassy microspheres are the third type of material with inherent price advantage. The microspheres reach a saturated adsorption state under high pressure hydrogen, and then release at ambient temperature, and regas thermally induced reduction. The main question now is how to control the activation process of such microvessels.
We can also list a variety of other materials, such as porous metal-amorphous materials, and hydride slurries (mixtures of alkali metal fines and complex oils). The efficiency of these hydrogen storage technologies is modest, but they are feasible for small-scale stationary applications where the durability and economy of hydrogen storage are clearly required.
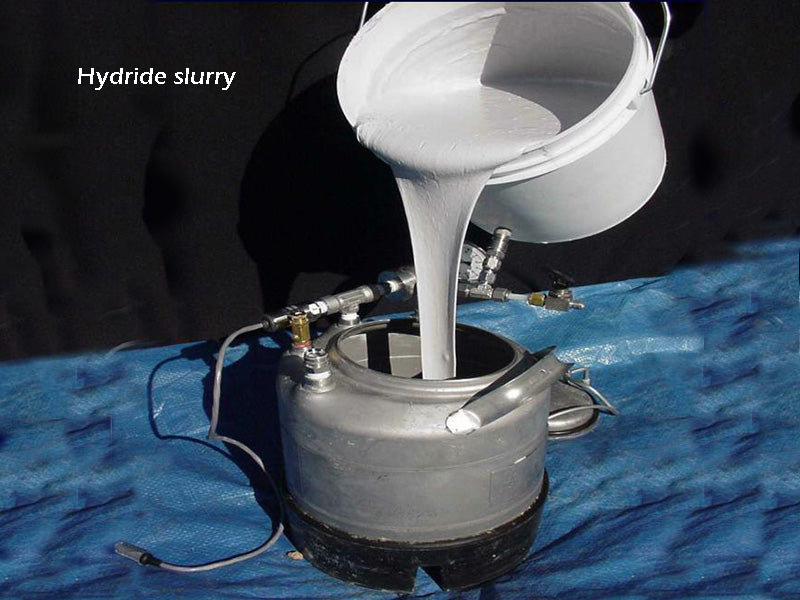
A class of materials that have recently emerged as hydrogen storage materials are molecular organic frameworks (MOFs). It is a large structural entity formed by ligands and organic complex radicals bound to different types of metal ions. This type of hydrogen storage material is latticed through a large-frame cage structure formed by a super-large mesh. These holes provide a huge specific surface area (greater than, 8000m2/g) for hydrogen storage, making it possible to physically adsorb hydrogen molecules; and MOFs can also form chemical bonds. Some constituent molecules are cheap, such as metal oxides. The reported performance is high (the hydrogen storage density is greater than 8%), but since its hydrogen storage process is still essentially physical adsorption, it is similar to the absorption and resorption method adopted by those nanocarbon structures, that is, hydrogen is captured at low temperature. At present, a large amount of hydrogen storage research is devoted to the research of such materials, but their long-term performance has yet to be verified, especially whether there are risks in the process of hydrogen absorption and release, and how biocompatibility of this molecule is.
2.2 Chemical hydrogen storage
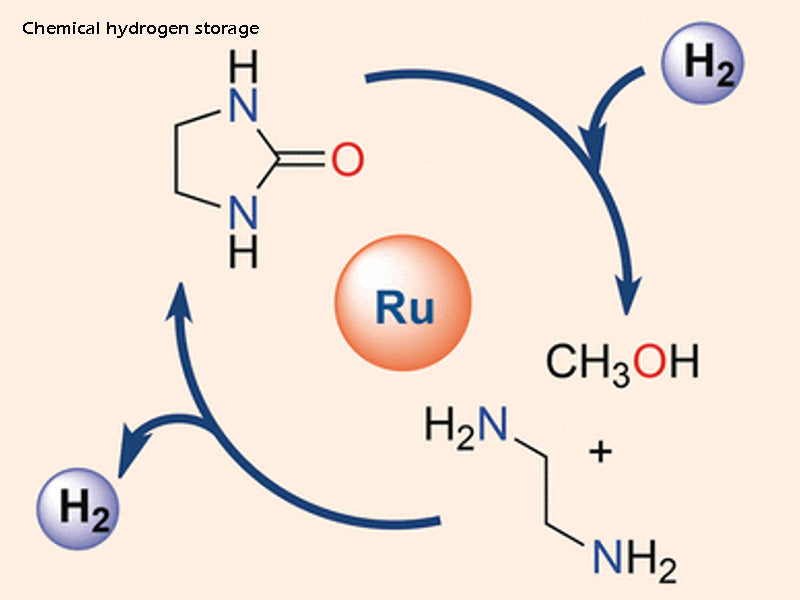
Chemical hydrogen storage means that hydrogen molecules dissociate to form complex atoms, and form metal bonds or ionic covalent bonds with specific elements (mostly metal atoms) in the existing molecular structure, thereby generating compounds or metal hydrides. Complex hydrides include aluminum hydrides (generated from alkali ions and aluminum), multi-element systems based on transition metals and alkaline earth metals, and new materials or amides called imides—nitrogen and hydrogen bonds. We can identify metal hydrides or complex hydrides by the weight or light weight after synthesis and the high temperature or low temperature environmental requirements of the synthesis process.
For the hydrogen storage process of metal materials, the process of hydrogen absorption and hydrogen release is essentially a one-step chemical reaction, and the metal lattice generally does not change; for composite materials, the insertion and removal of complex atoms are carried out in several steps. Reactions have their own energy levels. All the different types of complexes have one thing in common, that is, the diffusion process of extra particles, which we call "catalysts" in most cases, is actually the proper kinetic energy that must be obtained in order for the reaction to take place. Under this goal, the latticed material can be ground into powder using processes such as ball milling to increase the specific surface area of the material.
A metal hydride is a compound whose reaction equation looks like this:

The two elements M and H are connected by chemical bonds. In hydrides, H atoms occupy interstitial sites consisting of a certain number of adjacent M atoms. Chemical reactions depend on temperature and pressure and can be quantified by defining a set of isotherms. From this, it is possible to obtain reaction thermodynamic values, such as enthalpy ΔH (isotherm gradient along the 1/T direction) and entropy ΔS, which are consistent with the reaction heat generation. In the hydrogen release stage, the hydrogen atoms leave the above-mentioned interstitial positions and recombine into hydrogen molecules.
2.2.1 Metal Hydride Hydrogen Storage
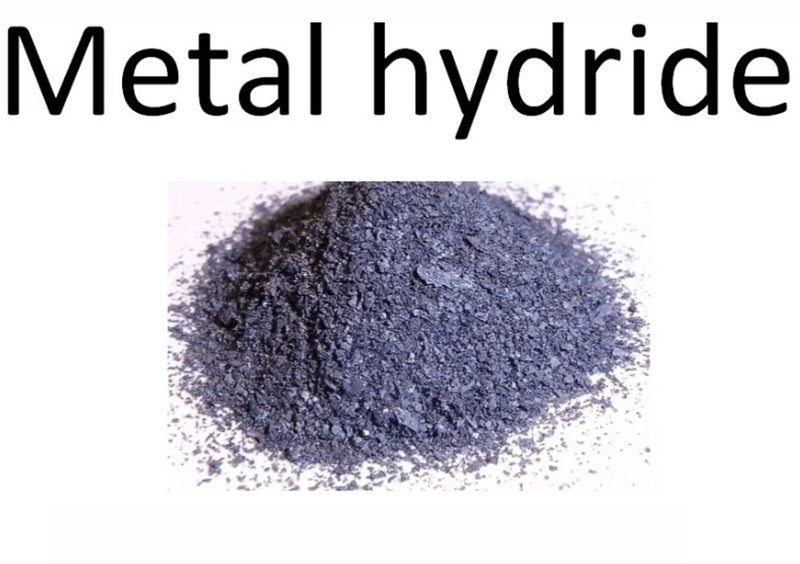
As mentioned earlier, metal hydrides can also be referred to as "traditional hydrides"; they can be divided into several categories according to their structure and thermodynamic properties. We focus on the following categories:
1) LaNi5 (hexagonal structure), which is usually an important part of electrodes for rechargeable batteries, such as NiMH batteries (jin hydrogen batteries).
2) FeTi and its derivatives (structural types such as CsCI).
3) Compounds with Laves phase structure, whose molecular formula is AB2, in which A is Zr, Ti, and B are transition metals, with cubic or hexagonal structure, and in some cases, also used as battery electrodes.
4) BCC structure, that is, alloys based on body-centered cubic structure, such as β-Ti, V, Cr, etc., and MgH2 form powder nanostructures, which are mixed with hydrogenation catalysts and intermetallic compounds rich in magnesium.
The reaction of these four types of intermetallic compounds to generate low-temperature hydrides is reversible under the conditions of close to ambient temperature and moderate pressure (generally 1 to 10 bar).
Therefore, LaNi5 (theoretical storage density is 1.4%) and derivatives formed by steel substitution are better in applicability and have also been tested in a variety of different application systems. These include hundreds of kilogram hydrogen storage systems for proton exchange membrane fuel cell systems (PEMFCs), propulsion systems for American hybrid vehicles (400kg hydrogen storage systems are required for a driving range of nearly 300km), as exchange membrane fuel cell PEMFC integrated systems small storage containers. But in reality, the density of reversible hydrogen storage systems is only about 1%, and another disadvantage of this excellent hydride is that the cost of the metal is too high, and its heavy weight is not suitable for transportation applications.
FeTi compounds do not show the best performance in practical applications (the hydrogen storage density is less than 1%). However, the low price of iron-titanium-based alloys produced in the steel industry opens the door to large-scale stationary applications, even in the field of transportation, such as some German submarines. This type of submarine carries 160t of this storage compound to provide regassing for two 120kW PEMFC systems.
Laves phase structure alloys (molecular formula ZrM2, where M is Mn, Fe, Co, Ni, etc., in different proportions) have attracted attention because of their good ambient temperature adaptability and suitable pressure requirements. Its theoretical specific volume does not exceed 2% (less than 1.5% in practical applications), and there is a possibility of hydrogen absorption failure after a long-term hydrogen storage cycle. In addition, the cost of different materials also limits its stationary applications.
The maximum hydrogen storage densities of active magnesium and slightly weaker Mg2Ni compounds are 7.6% and 3.9%, respectively. At present, a large number of researches focus on obtaining nanostructures of materials through ball milling process, and their mediocre kinetic performance in hydrogen absorption and hydrogen release processes can be improved. By adding additives with a "catalytic" effect, the actual specific volume can be reduced to 6% and up to 6.5%. These data have been confirmed by tests in the industrial field. The innate thermodynamic inadequacy of the reaction lies in the high dissociation temperature of these hydrides. When the reaction equilibrium pressure is 1 bar, the dissociation temperatures are around 250 °C and 320 °C, respectively. This means that for MgH2 hydrogen storage, about 1/4 of the hydrogen storage energy is used to provide heat and thermal power for the hydride generation reaction. Due to the unstable state of Mg2NiH4 in the hydrogen uptake/release cycle, only MgH2 appears to be a robust hydride that is inexpensive, recyclable, biocompatible, and suitable for industrial mass production. The progress of metallurgical methods in material activation means that the specific volume of this material will exceed 7% in the near future, even approaching its theoretical reversible specific volume (7.6%). In practical applications, the hydrogen storage system must be operated efficiently according to the specific application mode (SOFC or ICE), and the regenerative heat utilization should be carried out to achieve the global optimization of the system energy. It is worth noting that the thermal conductivity parameters of this hydride are greatly improved due to the effect of the MgH2-graphite composite.
2.2.2 Hydrogen storage in complex hydrides
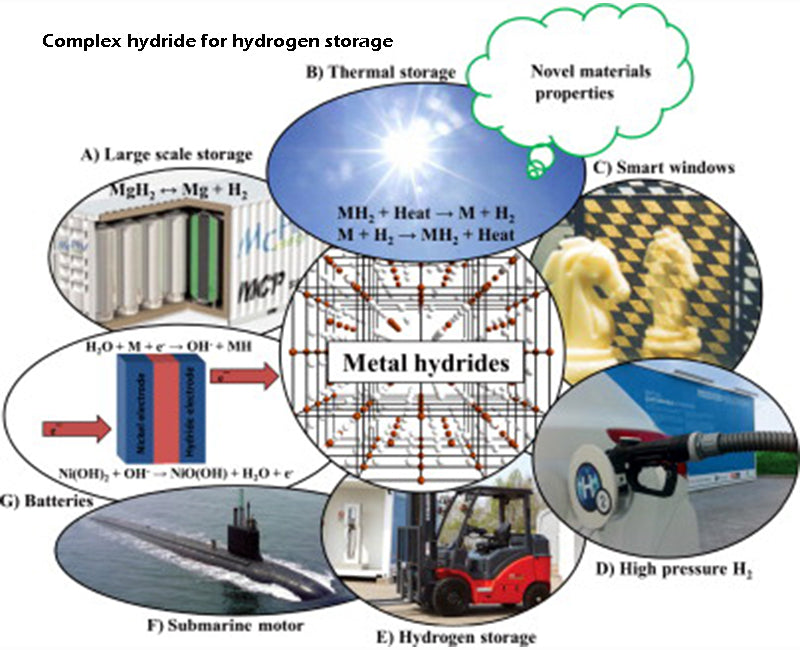
Complex hydrides based on magnesium, calcium, other alkaline earth elements or rare earth elements are currently under development. The synthesis process of these hydrides is complex, and no important properties have been found for their generalized applications, except for micro-hydrogen storage containers that integrate application systems under everyday conditions.
Aluminium hydride materials are composed of aluminum and positively charged basic elements, and the molecular formula is AAIH4, where A is Li, Na, and K. It holds promise for hydrogen storage in high hydrogen storage density grades (10.5%, 7.5%, 5.7%, respectively). A lot of basic and applied research (storage and recovery containers of several kilograms) is being carried out in this area, as well as other related applied research on this type of material. The hydrogen absorption and release temperatures of KAIH4 are both 300 °C, while NaAIH4 is better, its hydrogen absorption and release temperatures are 160 °C and 130 °C, respectively. In fact, the stored hydrogen can be fully released due to the existence of two reaction processes; only NaAIH4 is recyclable and reversible for practical applications, at least for a limited period.

A hydrogen storage density of 5.5% can release 3% to 4% of hydrogen.
The addition of aluminum hydride to catalysts with ball milling and nanostructures (such as titanium salts) can achieve good activity, but because aluminum hydride is very unstable and prone to spontaneous combustion, it should be used with caution from the current situation. Because in the process of hydrogen absorption, it is necessary to add several tens of bars, or even hundreds of bars of pressure to the hydrogen.
The hydrogen uptake and release process of ternary compounds such as amides or imides are multi-step reactions, and from a chemical point of view, hydrogen is nearly completely released (hydrogen uptake). In fact, characteristic phases exist in materials like LiNH2, Mg(NH2)2, Li-Mg-N-H, Mg(NH3)6Cl2 and (CH3)4NBH4 (theoretical mass hydrogen storage density reaches 18%). But the most disadvantageous factor is that if a trace of ammonia (NH3) is formed at any stage of the hydrogen release reaction, the material loses the reversibility of the hydrogen storage cycle.
Other physical hydrogen storage systems are also in development, but we cannot list them all here. The main limitation of this type of hydrogen storage technology is the pressure required for hydrogen charging, and the temperature of the dissociation process, and the release of all hydrogen will reach a very high temperature (400~600℃). In addition, such mixtures for hydrogen storage must be chemically innocuous.
Read more: Indirect hydrogen storage mode