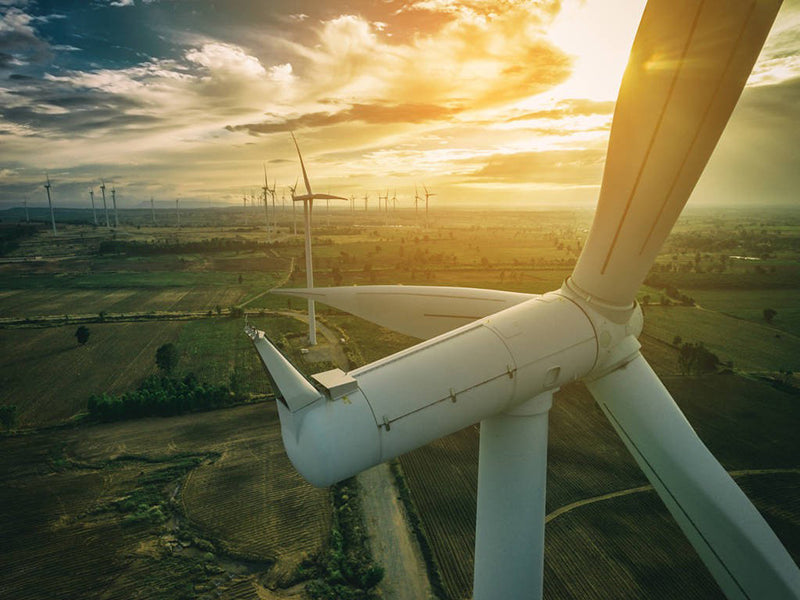
Main content:
1. Hierarchical load controller
The biggest feature of the independent wind power generation system is that it does not need energy storage equipment, and directly provides AC power to the user's electrical equipment. With a load controller, the ideal situation is to continuously change the user load according to changes in the frequency signal from the generator, so that the output power of the wind turbine is balanced with the user load. In fact, the load controller adopts the method of grading input or load shedding to balance the change of the output power of the wind turbine. As long as the change of the load at each stage of the load controller is not too large, the wind turbine can run close to the optimal power load line. In the wind power generation system using the load controller, the load that is frequently changed (input or cut) should use resistive equipment (such as electric heaters, electric furnaces, etc.). Of course, the maximum power value of the variable load should be determined according to the maximum allowable power value of the wind turbine and generator. In this way, when the load that is often fixed in the load controller system is reduced because it is not needed, it can be controlled by the system. to make up for the variable load inside.
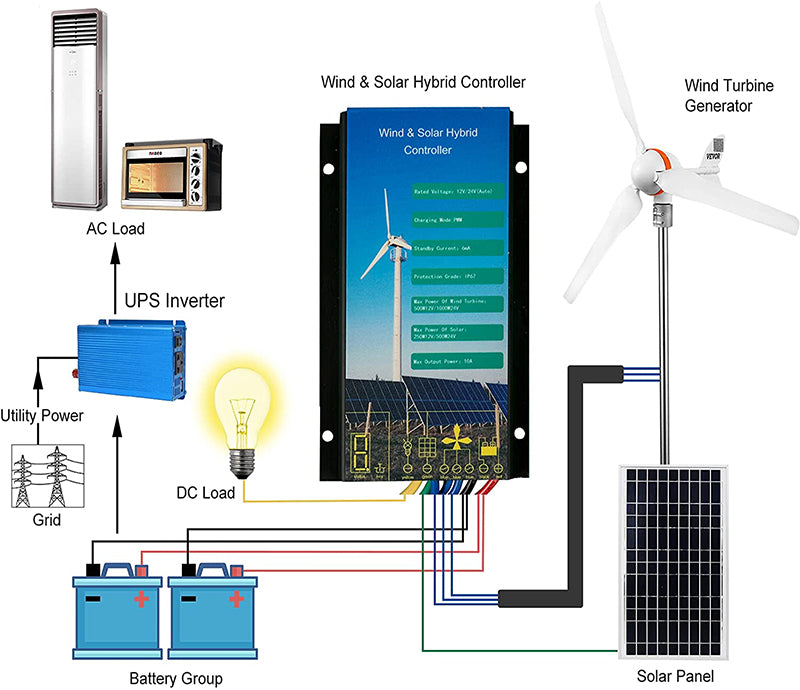
The principle of the graded load controller is shown in the figure below. The load is divided into several grades, and the frequency of the input or cut-off point of each load is different, which can be adjusted and determined in advance. When the output frequency of the generator of the load controller is greater than the frequency of the input operation point of the load of this level, the load of this level is switched on; when the frequency becomes less than the frequency of the cut-off point of the load of this level, the load of this level is cut off. Since the input and removal of the load of the load controller are carried out in stages, the output frequency of the generator will change accordingly when the load controller is turned on or removed. It may cause the load of this level to be switched on and off repeatedly at the operating point. In order to avoid this phenomenon, a hysteresis zone is set between the switch-on operating point and the removal operating point of the same level of load, so that the frequency of the switch-on point is slightly higher than the nominal operation point. point value, and the cut-off point frequency is slightly lower than the nominal operating point frequency value. As shown in the figure below, if the frequency of the nominal operating point is selected as 50 Hz, and the hysteresis zone is selected as -0.25 Hz~0.25 Hz, the frequency of the load input point of this stage is 50, 25 Hz, and the frequency of the cut-off point is 49.75 Hz , the hysteresis difference between the frequency of the load input point and the frequency of the cut-off point ensures the stability of the entire load controller system.
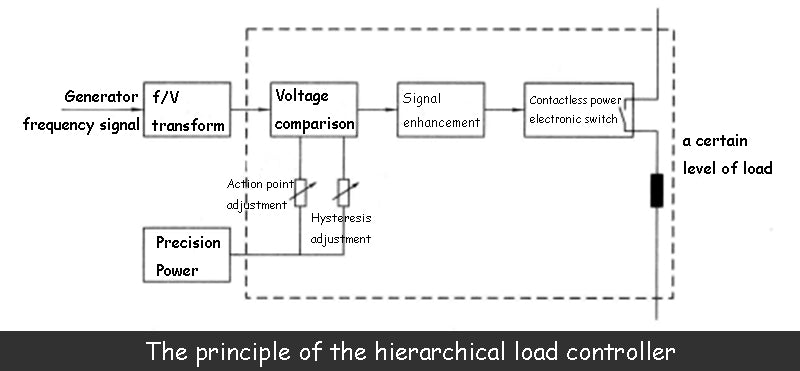
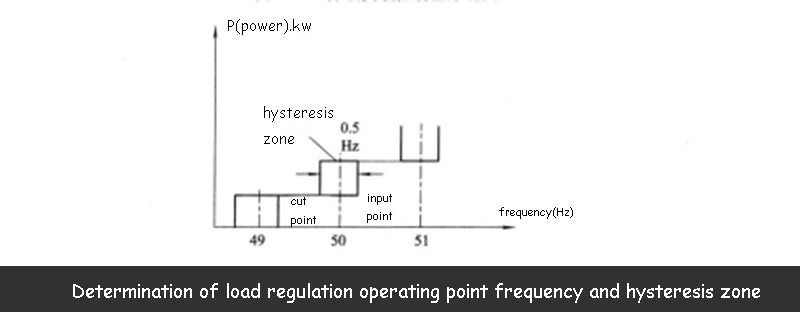
To achieve stable operation of the electrical system, the frequency of the generator can be controlled at 49~51Hz or 18-52Hzm. In order to prevent the independent running wind turbine from overloading, the wind turbine should have a pitch adjustment device or stall blades. It can automatically reduce the output power of the wind turbine and ensure the safety of the load controller system.
2. Load controller and variable speed constant frequency wind power generation
When the speed of the wind turbine fluctuates (or stops) and the generator voltage is lower than the battery voltage, the generator not only cannot charge the battery, but on the contrary, the battery must send current to the generator. A load controller interceptor is added between the circuit and the battery pack. Its function is that when the generator voltage is lower than the battery voltage, the interceptor acts to disconnect the connection between the two.
After the wind turbine drives the rotor of the main generator to rotate, due to the favorable magnetism of the generator, an induced potential is generated in the additional winding of the generator, and the induced potential is supplied to the excitation winding of the exciter after full-wave rectification by the diode.
The three-phase AC winding of the wind turbine and the exciter rotate coaxially, and an AC potential is induced in the three-phase AC winding, which is rectified by the three-phase half-wave rotating diode and supplied to the excitation winding of the main generator.
After the main generator excitation winding is energized, an induced potential is generated in the main generator winding, and at the same time, an induced potential is induced in the additional winding load controller, which increases the current in the excitation winding of the exciter, thereby increasing the main power generation. The current in the excitation winding of the main generator is repeated, the current in the excitation winding of the main generator is increasing, and the potential induced by the load controller in the three-phase winding of the main generator is also increasing, and finally tends to be stable, and voltage is established.
Wind energy is a kind of energy with strong randomness. The direction of the wind is constantly changing, the magnitude of the wind is strong and weak, and the change of the wind speed will cause the change of the speed of the wind turbine. If there is no necessary load controller, it will be driven by the wind turbine. The rotation speed of the alternator will also change accordingly, so the output voltage and frequency of the generator are not constant, whether it is powered by the wind power station alone or in parallel with other types of generator sets, or in parallel with the power grid. not allowed. On the other hand, it is well known that the wind energy is proportional to the cube of the wind speed. When the wind speed varies within a certain range, if the wind turbine is allowed to operate at a variable speed, so that the wind turbine load controller always maintains or is close to the operation at the optimal tip speed ratio, That is to say, the tip speed ratio is maintained at the optimum value and remains unchanged, so that the power coefficient value of the wind turbine load controller remains unchanged, and the purpose of better utilization of wind energy can be achieved. Therefore, the load controller and the variable-speed constant-frequency power generation method have important practical significance.
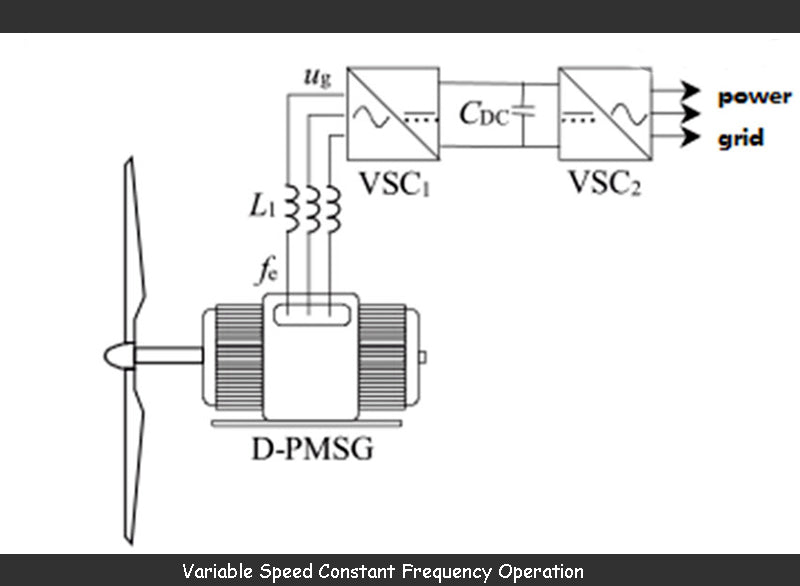
There are many different schemes to realize variable speed constant frequency power generation using load controller, such as AC-DC-AC conversion system; AC commutator generator mode; magnetic field modulation generator and down-frequency conversion system. Various load controller systems have different characteristics and are all under further research and development.
The AC-DC-AC conversion system connects the variable-speed wind turbine rotor and the alternator to the load controller. The variable-frequency alternating current generated by the generator is converted into DC through the load controller rectifier, and then into the load controller inverter. Power frequency alternating current, this method is technically mature, but due to the use of rectification and inverter devices, the cost of electronic equipment is high, which will lead to increased investment in power generation equipment.
When the rotational speed of the wind turbine changes due to the change of wind speed, the rotational speed of the driving shaft of the electromagnetic slip connection device will change accordingly, but the rotational speed of the driven shaft of the electromagnetic slip connection device rigidly connected with the AC synchronous generator can be automatically The magnetic field of the electromagnetic slip connection device is adjusted to remain unchanged, that is, the rotational speed difference between the driving shaft and the driven shaft of the electromagnetic slip connection device changes correspondingly. The adjustment of the magnetic field is realized by the speed measuring mechanism and the load controller of the electronic adjustment device, so the load controller of the electromagnetic slip connection device The variable speed constant frequency power generation system realizes the slip connection between the wind turbine and the generator by means of electromagnetic connection, and The magnetic field of the device load controller is connected by adjusting the electromagnetic slip. By changing the slip, it is possible to ensure a stable frequency power supply at the generator end when the wind speed of the wind turbine changes.
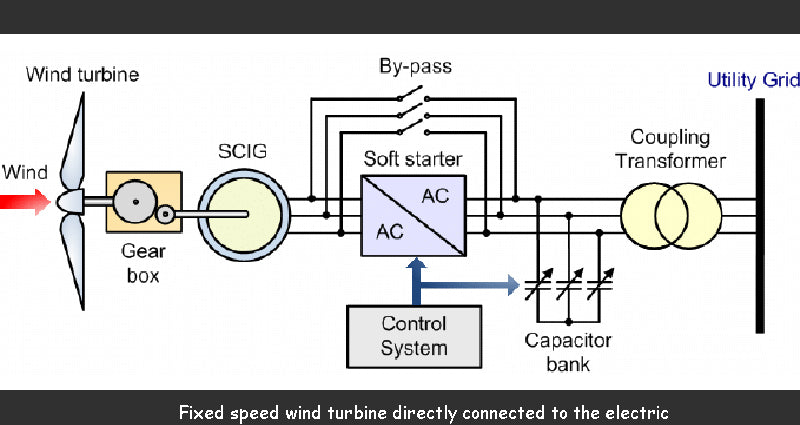
The electromagnetic slip connection device is essentially a special motor that acts as a clutch. It consists of two rotating parts. The difference from the general electromagnetic clutch is that there is no mechanical hard connection between the two rotating parts. , but realizes the elastic connection between the prime mover and the driven machine in the form of an electromagnetic field to transmit the torque.
From the structural principle point of view, the electromagnetic connection device is similar to the slip motor that is widely used in the industry. In industry, when the AC motor is powered by a constant frequency power grid, the slip motor can be used as a device for uniform speed regulation to realize the energy conversion from constant frequency electrical energy to variable speed mechanical energy. The electromagnetic slip connection device load controller and the alternator load controller together can realize the conversion from the variable speed mechanical energy to the constant frequency electric energy.
The structural form of the electromagnetic slip connection device can be various. Considering the reliability and simplicity of operation, the brushless excitation method without slip ring can be used. The disadvantage is that the slip power cannot be used, especially when the slip value is relatively large, the efficiency of the entire system will be affected. In order to improve the efficiency of the entire load controller system and obtain usable DC power at the same time, a structure with a clear ring in the rotating part can be considered, and the slip power is drawn out through the slip ring. The frequency and voltage of the slip power drawn from the slip ring also vary, but this type of load controller structure is effective for making full use of wind energy. The slip power drawn from the slip ring can be rectified by the rectifier device to charge the battery, and this part of the electric power can be sent to the network that requires DC power.
The slip power drawn from the slip ring can also pass through the load controller rectifier and the load controller inverter, firstly converted into DC, and then converted into rated AC to be fed to the power grid. This is also an AC-DC-AC conversion system.
Read more: Aerodynamic knowledge in wind turbines