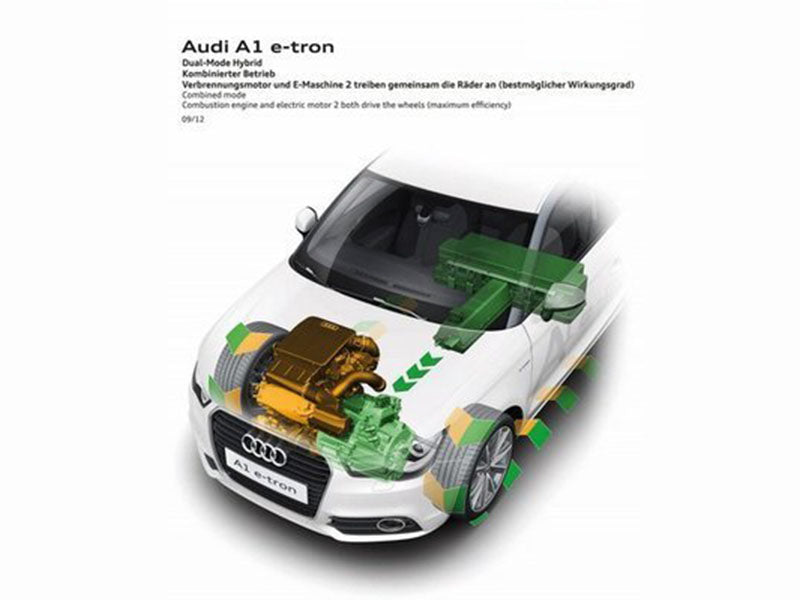
Main content:
The problem of energy storage has led to the short range of pure electric vehicles, so hybrid vehicles came into being. It combines an internal combustion engine with an electric motor and is able to use two different energy sources, such as chemical energy and electrical energy, at the same time. Obviously, these two energy sources can be combined in many different ratios, which creates some commercial terms that need to be explained to users, such as stop&go, mild hybridiza-tion, full hybridizatio, boost, downsizing, etc. According to the different coupling modes of the internal combustion engine and the electric motor, the structure of hybrid vehicles can be divided into: parallel structure, series structure and road coupling.
Hybrid vehicles, like all power vehicle assembly architectures, the aim is to reduce the consumption of hydrocarbon fuels, thereby reducing pollution and greenhouse gas emissions, and can even achieve zero emissions in cities. Its range depends on the capacity of the electrical energy storage. Not all structures use the same energy saving method, some methods may be more efficient, but are more limited due to the characteristics of energy.
The structure and class of hybrid vehicles are independent of vehicle type, whether it is a passenger car, van, construction vehicle or passenger car.
Hybrid vehicles of two-wheelers are outside the scope of this article because hybrid systems often require an increase in overall vehicle weight and volume to accommodate the heat engine and electric motor. The only possible application is a two-wheeler that often operates in a start-stop mode, where the combustioengine can be completely stopped when parked.
1.Parallel structure of hybrid vehicles
Figure 1 presents the rationale, explaining what start-stop means. The electric motor can be mounted directly on the shaft of the engine, as shown in the picture, or connected to the mechanical system through drive wheels and belts. Electric motors in hybrid vehicles serve two purposes: to charge the battery and start the car, and even act as a drive engine when zero emissions are required. The performance of the motor depends on its power and the capacity of the battery. The gain brought to the user by this method is very limited (about 5%), and it is only effective in urban operation, and the braking energy recovery is basically impossible.
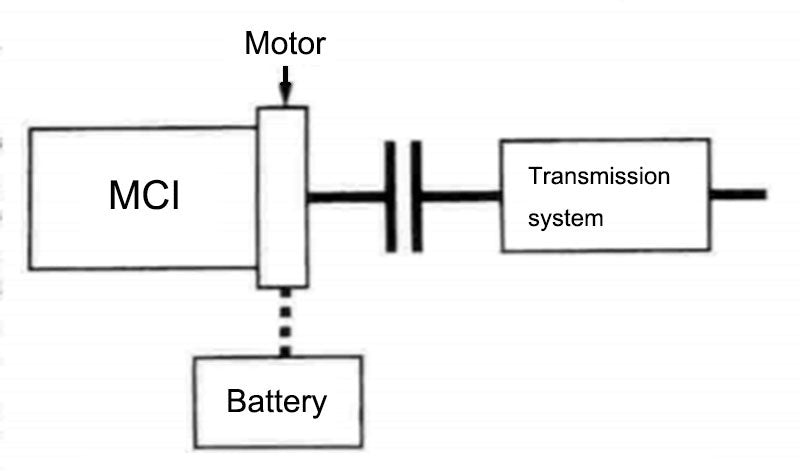
Figure 1-Schematic diagram of start-stop operation mode
The effect of electric drive reduces the size of the internal combustion engine and therefore reduces friction and losses. In order to improve the power output performance of hybrid vehicles, for example, when accelerating, the electric motor can be used as auxiliary power to improve the acceleration performance of the engine.
The parallel structure of hybrid vehicles is slightly more complicated, as shown in figure 2. The parallel structure is based on mechanical coupling, which is common in epicycloid gear trains. Although the three shafts each have different rotational speeds, their torques can still be superimposed. If necessary, the clutch can be engaged to disengage the mechanical coupling system, allowing the hybrid vehicle to operate in conventional vehicle mode or in zero-emission all-electric mode. The arrows in figure 2 indicate the direction of energy flow. The internal combustion engine can only provide mechanical energy to the wheels or to the generator, which is used to charge the battery or to power auxiliary functions, or to the electric engine as a generator through mechanical coupling, and this last energy flow route makes braking energy Recycling is possible.
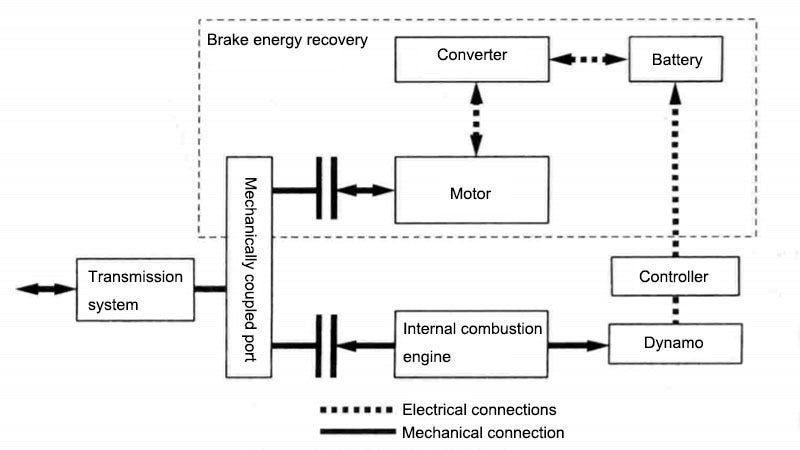
Figure 2-Parallel Hybrid Architecture
In this system, all the energy of the hybrid vehicle comes from the energy of the internal combustion engine and the feedback from the brake, because each inverter works at the optimal point, the overall energy management effect is very good. Adding battery chargers powered by an external grid will diversify energy sources.
Hybrid vehicles of this structure were first proposed by Toyota and used in its Prius models. Other manufacturers have followed this technical route with their own models, and have increased the level of technical sophistication by tightly integrating one or two motors into a mechanically coupled system, thus producing many different ways of distributing energy.
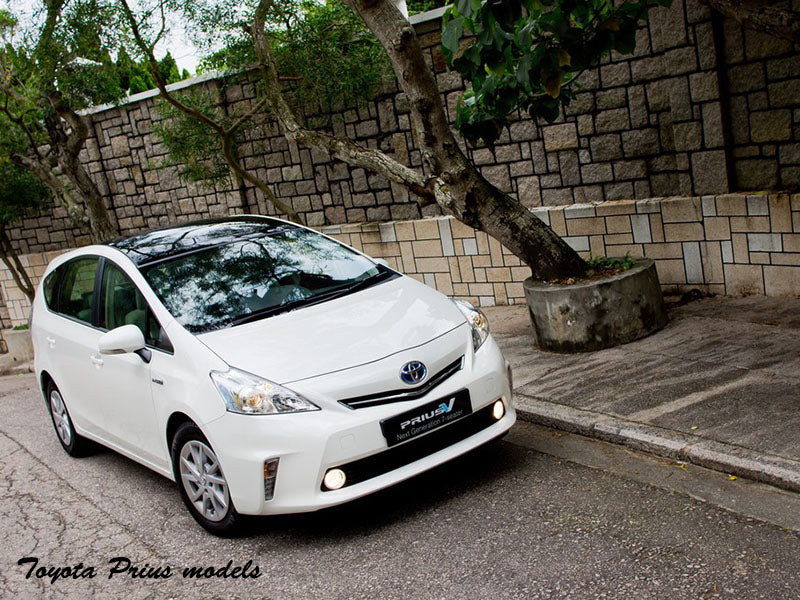
It's important to note that mechanical couplings, motors, inverters, and batteries all contribute to the added weight of a hybrid vehicle. The only benefit is the reduction in the size of the internal combustion engine. So it's no surprise that hybrid technology is currently limited to top-of-the-line cars.
There is no standard for the voltage rating of the DC bus in a hybrid vehicle. Using a high voltage rating to reduce the diameter of the conductors in the motor is beneficial, but high voltage is bad for the battery. If a 540V DC bus voltage is required, a 400V AC power supply needs to be rectified, and 150 lithium-ion batteries or nickel-metal hydride batteries need to be combined in series. The series connection of batteries will bring about voltage sharing problems during charging, because we want all batteries to work in the same state. Therefore, it is becoming a trend to have three or four different voltage levels on the same hybrid vehicle, and the schematic shown in Figure 3 was inspired by Toyota's Lexus model.
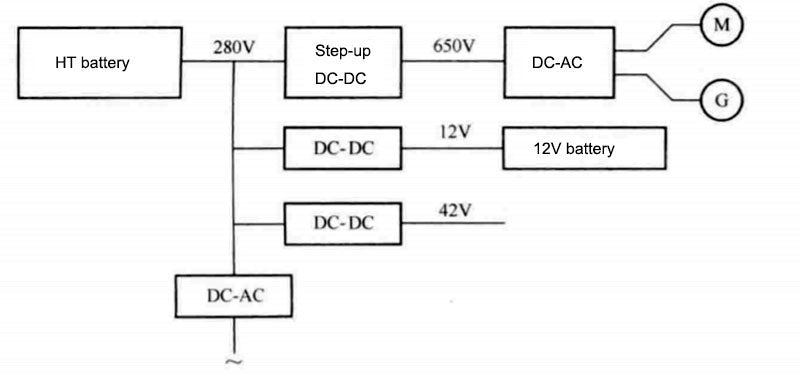
Figure 3-Electric vehicle block diagram with four voltage levels
The DC-DC converter can change the voltage level. Both the electric motor and the generator of the hybrid vehicles use a three-phase AC system, and the use of standard AC voltage allows the equipment originally designed for the traditional distribution network to be used directly, thus eliminating the need to develop special equipment for the air-conditioning system. Due to the complex electrical and mechanical components of the hybrid vehicles, a monitoring unit needs to be added to the energy management system so that the battery has the ability to recover braking energy (for example, the battery cannot be fully charged, otherwise it will not be able to absorb any excess).
Thanks to braking energy recovery, hybrid vehicles consume less energy than conventional cars in city traffic or on ordinary highways. But on the highway, because hybrid cars are heavier than conventional cars, their energy consumption is equal to or greater than the latter.
2.Tandem structure of hybrid vehicles
Internal combustion-electric hybrid trains have a typical series-type hybrid configuration, But for hybrid vehicles, this configuration is complicated by the addition of energy storage elements such as energy storage lithium-ion battery, supercapacitors, or flywheel energy storage. The series structure is shown in Figure 4.
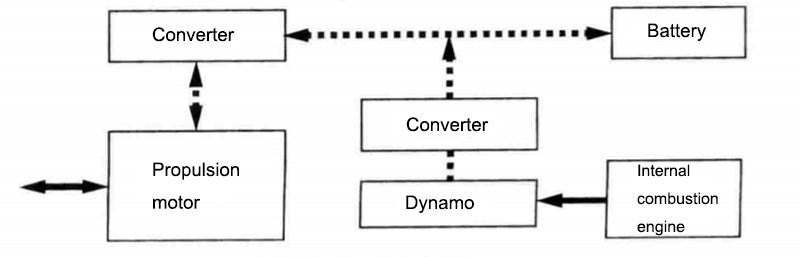
Figure 4-Typical series hybrid structure
In this configuration, the hybrid vehicle's internal combustion engine drives a generator (usually an alternator) to generate electricity. The AC voltage is rectified and adjusted to the voltage level of the battery, and the DC bus voltage is supported by the battery. Then, connected to the traditional propulsion chain of electric vehicles, either a central motor and differential, or a more decentralized structure with multiple motors or even in-wheel motors.
The arrows in the diagram indicate the direction of energy flow. The internal combustion engine can only provide mechanical energy, and the power converter connected to the generator only allows one-way flow of energy. The recovery of braking energy in a hybrid vehicle is achieved by the electric motor and its propulsion converter. Braking energy is stored in the battery, so the state of charge of the battery pack must be monitored in real time to store this energy efficiently.
Since different energy converters are connected in series (mechanical energy is converted into electrical energy, and electrical energy is converted into mechanical energy), the total efficiency of the system is equal to the product of the efficiencies of the different converters, so even if the internal combustion engine in a hybrid vehicle is operating at its best, this structure There are still inevitable deficiencies. The role of the energy management unit is to balance the energy provided by the internal combustion engine with the energy provided by the battery.
The tandem configuration is the only one that can be used by other types of generators, such as electrochemical power sources or fuel cells. In the schematic shown in Figure 5, an example of another fast energy storage technology (supercapacitor) for braking energy recovery is presented.
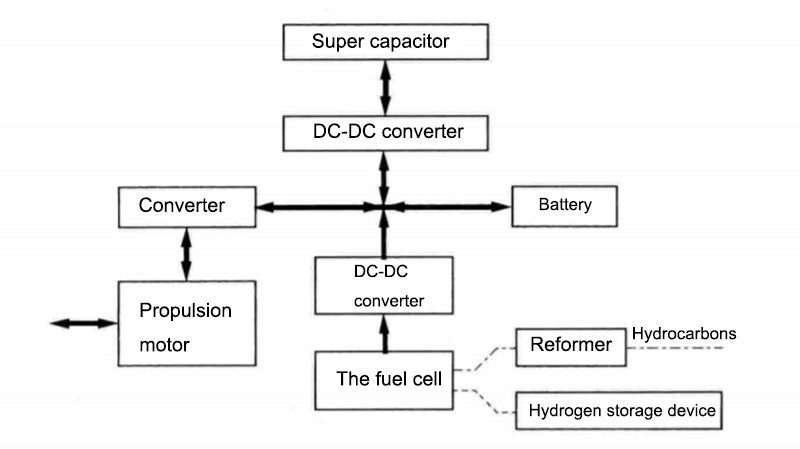
Figure 5-Series Hybrid Architecture with Fuel Cells and Supercapacitors
The fuel cell can be powered by hydrogen or carbon complex fuel flowing through a reformer. As a power source, it means that the fuel cell stack ensures the proper operation of auxiliary functions such as compressors and air humidifiers, fuel processors, refrigeration system flow controllers, and hydrogen recirculation pumps.
Fuel cell power generation is irreversible and outputs direct current. Its overall efficiency is currently around 35%, but if the electrochemical conversion efficiency and the efficiency of auxiliary functional devices can reach 55% to 60%, then the power generation efficiency of fuel cells is expected to be doubled.
The ECCE Bank test bench is in a series configuration and can test different types of generators (eg variable speed or constant speed generators, proton exchange membrane fuel cells in the SPACT80 program), different types of electric drives, as well as batteries, supercapacitors, flywheel energy storage etc. performance.
3.Road coupling for hybrid vehicles
In the two structures analyzed above, the hybrid vehicle internal combustion engine and electric machine are strongly coupled through mechanical or electrical connections. A third hybrid configuration for hybrid vehicles consists of two independent propulsion systems: one acting on the front wheels and one acting on the rear wheels, and the energy management unit constantly balances the output of the two systems. So this looks like a real electric car, charging the battery via the grid and recovering braking energy. However, practical application requirements also require it to have the characteristics of conventional gasoline or diesel vehicles, while the hybrid system allows hybrid vehicles to be competent in two modes: zero-emission in urban driving mode and internal combustion engine operation in out-of-town driving mode. The organic combination of these two modes enables the hybrid vehicle to obtain a greater improvement in the dynamic performance. Plug-in charging is essential for this electric vehicle.
Such a vehicle has not yet been commercialized, but there is already some research in the field.
4.Hybrid rail locomotives
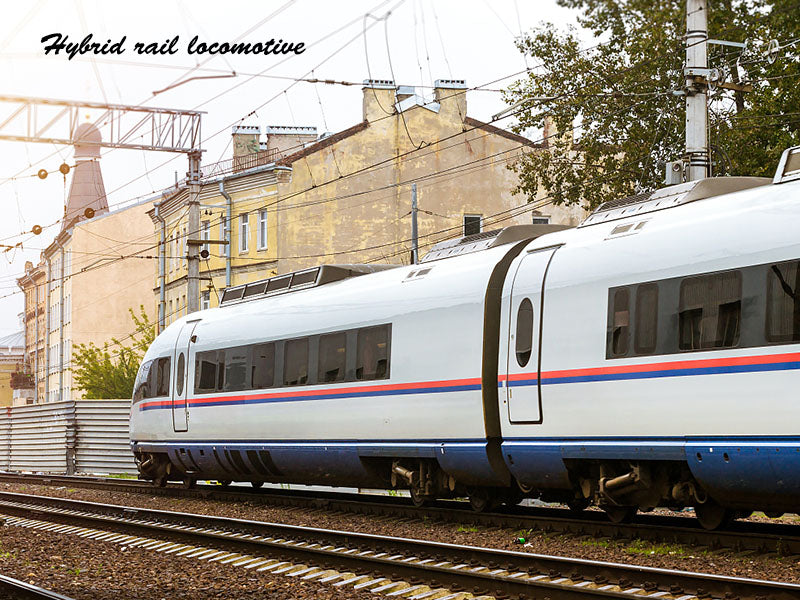
The energy required for a locomotive to start is very high, because only then can the carriage be dragged and accelerated to a smooth speed. Hybrid power can be a good solution if enough energy is stored. The basic structure of locomotives has been electrified, since the traction motors are generally DC motors, asynchronous motors or synchronous motors with power electronic controllers. Due to the long lifespan of equipment in railway systems (at least 50,000h or 15 years), electrochemical energy storage technology (batteries) has become a big problem. The life of supercapacitors is not long enough, and the inertial flywheel energy storage system can meet the requirements well, and superconducting energy storage has not been used in this occasion.
Railway equipment manufacturers have begun to study the use of hybrid locomotives. Japan, California in the United States, and Canada (Green Goat) have claimed to use this locomotive. Green Goat's diesel engine power is very small, only 165kW, its function is only to charge the battery pack, the voltage level is 600V. Energy consumption is claimed to be reduced by 60%, with a corresponding reduction in greenhouse gas emissions.
In the framework of the PLATTHEE project, the French SNCF company (French national railway company) has tested the hybrid locomotive. The test object is a transfer locomotive (LHYDIE) installed with different energy storage systems. The energy storage includes batteries, supercapacitors and flywheel storage. can. The energy of the energy storage system is provided by a small power diesel generator. The SPACT80 project in France is also testing fuel cells equipped with hydrogen energy storage. The current voltage rating is 540V (same as the ECCE test bench), but it will eventually target 750V, which is also the voltage rating for hybrid trams and hybrid vehicles.