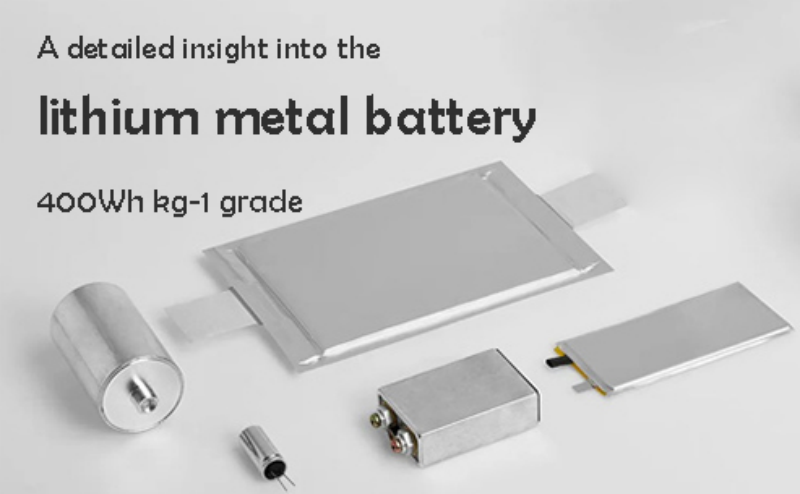
Main content:
- Preparation of low-expansion Li/LiB anode with built-in LiF-rich interfacial layer
- Li/LiB-PEL anode surface composition analysis and Li-Li asymmetric battery cycling
- Observation of the failed anode interface
- Cycle internal stress analysis
- Cycle performance test of Ah grade pouch lithium metal battery
- Conclusion
Li metal has a theoretical capacity as high as 3860 mAh g-1, making it an ideal anode for realizing high energy density devices. However, the side reactions between Li metal and the electrolyte continuously consume the electrolyte, resulting in the continuous formation of solid electrolyte interphase (SEI), resulting in the loss of active lithium and the degradation of the battery cycle performance. At the same time, the traditional lithium metal anode has a two-dimensional planar structure, and the repeated deposition/stripping of lithium metal during the cycling process makes the interior of the lithium metal battery face huge pressure changes all the time.
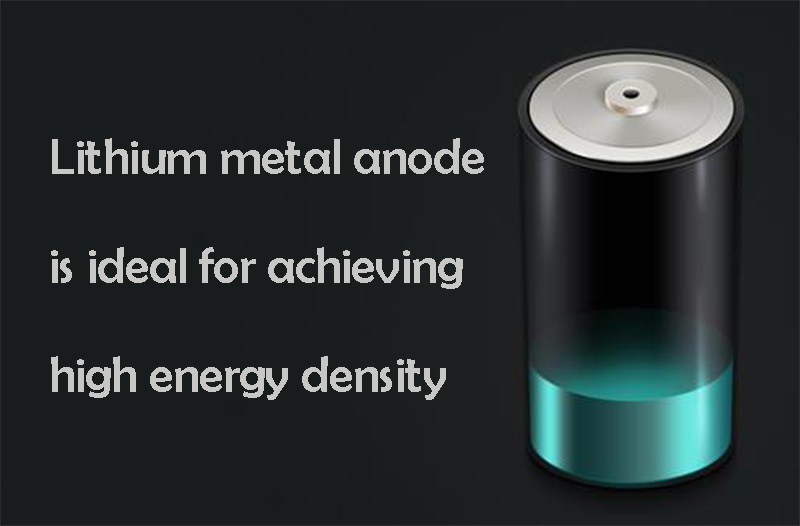
Achieving Ah-grade pouch lithium metal batteries with long cycle life remains extremely challenging under practical conditions of high cathode loading, lean electrolyte, and limited lithium sources. As an important component in SEI, LiF has a good electronic insulator function, which can effectively prevent the leakage of electrons through SEI, and at the same time can alleviate the continuous decomposition of the electrolyte. In addition, LiF has a high interfacial energy for the lithium anode, which can stabilize the lithium metal anode by reducing the activation energy barrier and promoting the diffusion of lithium ions at the electrolyte/lithium anode interface.
In this article, a single-phase and dense [Li(DMF)3][TFSI]/PVDF-HFP polymer solid electrolyte (PEL) was selected to form a LiF-rich interfacial layer inside the partially delithiated 3D Li/LiB anode. The modified three-dimensional Li/LiB-PEL anode can not only alleviate the pressure change during cycling, but also help to reduce the local current density of the electrode, so that the lithium metal anode can be uniformly deposited, thereby improving the cycling performance of the lithium metal battery.
1.Preparation of low-expansion Li/LiB anode with built-in LiF-rich interfacial layer
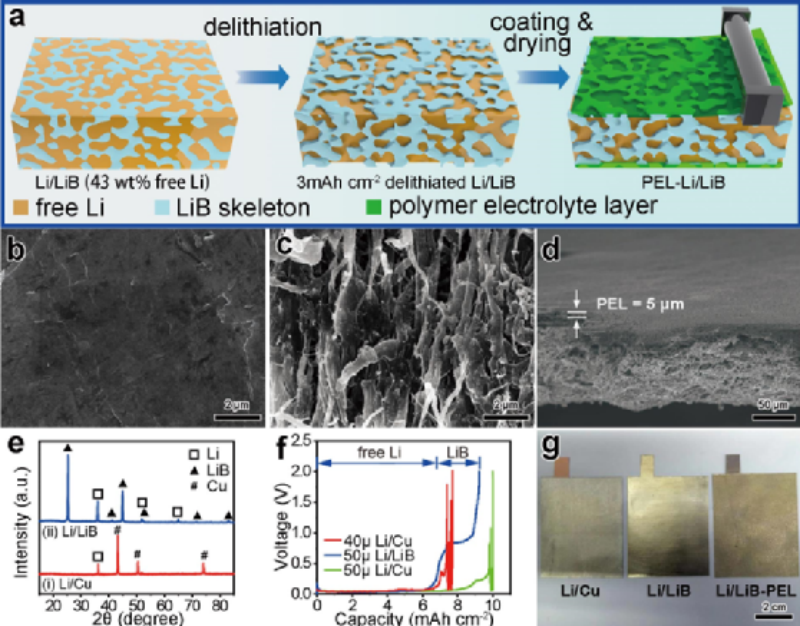
Figure 1 (a) Schematic diagram of the preparation process of Li/LiB-PEL anode. SEM images of (b) Li/LiB composite anode and (c) three-dimensional LiB framework after delithiation. (d) Cross-sectional SEM image of the Li/LiB-PEL anode. (e) XRD patterns of Li/Cu and Li/LiB anodes. (f) The charge-delithiation curves of Li/Cu and Li/LiB anodes when the upper voltage limit is 2.0 V. (g) Macroscopic physical photos of different anodes.
In this paper, a three-dimensional anode with built-in LiF-rich interfacial layer was prepared by electrochemical delithiation and composite polymer solid electrolyte (Fig. 1a). The three-dimensional structured LiB fibers are about 100–500 nm in diameter (Fig. 1c). The surface of the polymer solid electrolyte formed by casting coating is dense and uniform, with a thickness of about 5 μm, and has strong adhesion to the three-dimensional LiB framework (Fig. 1d).
The X-ray diffraction (XRD) patterns of Li/Cu anode and Li/LiB anode show that both are composite electrodes of current collector and lithium metal (Fig. 1e). The 50 μm Li/LiB composite anode can stably contribute about 6.86 mAh cm-2 of areal capacity of free lithium during charging, and the 40 μm thick Li/Cu anode also has a similar areal capacity (Fig. 1f). Figure 1g shows the macroscopic physical photos of the three anodes used in this work: Li/Cu, Li/LiB and Li/LiB-PEL.
2.Li/LiB-PEL anode surface composition analysis and Li-Li asymmetric battery cycling
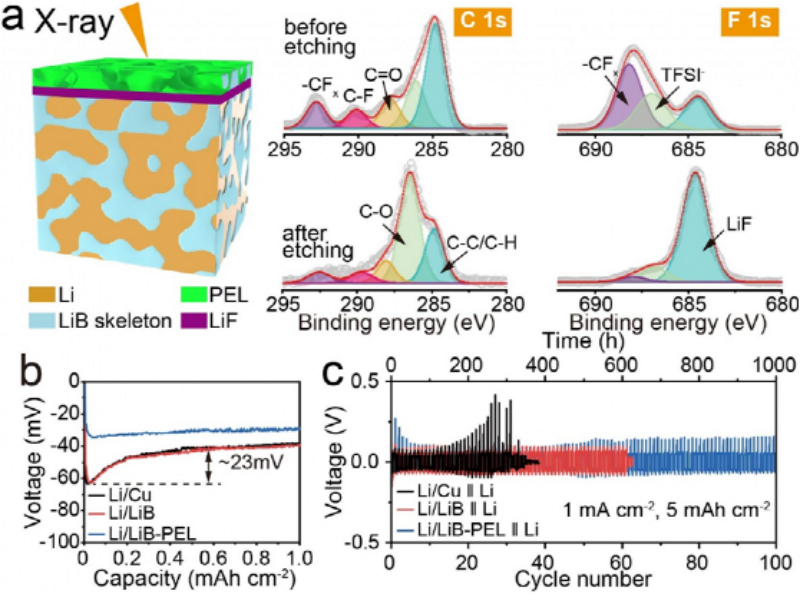
Fig. 2 (a) XPS spectra of C 1s and F 1s signals of Li/LiB-PEL anode before and after etching. (b) Li nucleation overpotentials on Li/Cu, Li/LiB and Li/LiB-PEL anodes. (c) Asymmetric Li-Li at 1 mA cm-2 and 5 mAh cm-2 with Li/Cu, Li/LiB and Li/LiB-PEL as working electrode and 450 μm thick Li metal as counter electrode Battery cycle stability test.
X-ray photoelectron spectroscopy (XPS) revealed the chemical nature of the SEI formed at the Li/LiB-PEL anode. After etching the anode interface, it can be found that the content of LiF increases significantly, and the prominent LiF signal proves the formation of LiF-rich SEI inside the Li/LiB-PEL 3D anode (Figure 2a). Meanwhile, the Li/LiB-PEL anode exhibits a lower nucleation overpotential (Fig. 2b), indicating that the three-dimensional structure of the Li/LiB-PEL anode helps to reduce the localized current density and improve Li-ion transport for Li deposition/stripping dynamics.
The Li/LiB-PEL anode can be stably cycled for more than 1000 hours at a high areal capacity of 5 mAh cm-2. The average Coulombic efficiencies (CEavg) of Li/Cu, Li/LiB and Li/LiB-PEL anodes were 95.7, 97.8 and 99.2%, respectively (Fig. 2c). The improved CE and cycle life demonstrate that the PVDF-HFP-based polymer solid electrolyte can act as a protective layer for Li metal anode, and the LiF interfacial layer can promote the uniform deposition of Li during cycling and effectively suppress the growth of lithium dendrite in the 3D anode.
3.Observation of the failed anode interface
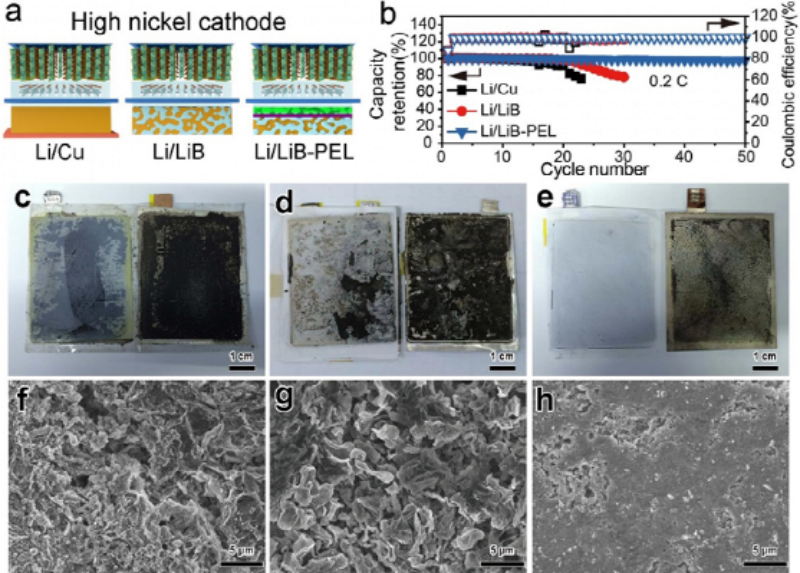
Figure 3(a) Schematic diagram of Li‖NMC83pouch lithium metal battery using Li/Cu, Li/LiB and Li/LiB-PEL as anodes and (b) corresponding charge-discharge cycling stability curves. Optical photographs of (c) Li/Cu, (d) Li/LiB and (e) Li/LiB-PEL anodes after cycling disassembly. And the interface SEM images of (f) Li/Cu, (g) Li/LiB and (h) Li/LiB-PEL after cycling for different anodes.
In order to further realize the lithium metal battery with high energy density, we choose the high-Ni cathode LiNi0.83Mn0.06Co0.11O2 (NMC83) with a specific capacity greater than 200 mAh g-1 as the active material. The cycling stability of Li/Cu, Li/LiB and Li/LiB-PEL anodes was evaluated (Fig. 3a). The initial areal capacity of a single-layer pouch lithium metal battery is as high as 5.88 mAh cm-2. By dismantling and observing the negative-side interface after cycling, we compared the morphological changes of lithium anodes with different structures before and after cycling. The morphology of the Li/Cu anode side is severely damaged (Fig. 3c), reflecting the large side reactions between the initial Li/Cu anode and the electrolyte.
The surface state of the Li/LiB anode after cycling is similar to that of the 2D Li/Cu anode, showing a rough surface covered by “dead lithium” (Fig. 3d). The SEM images of the cycled Li/Cu and Li/LiB anodes both showed loose and porous microscopic morphologies accompanied by micron-scale dendrites (Fig. 3f,g). The newly formed dendrites will accelerate the side reactions with the electrolyte, which will eventually lead to the failure of the lithium anode. In contrast, the Li/LiB-PEL anode still maintains an intact surface (Fig. 3e) and exhibits a dense and dendrite-free morphology in the SEM image of Fig. 3h.
4.Cycle internal stress analysis
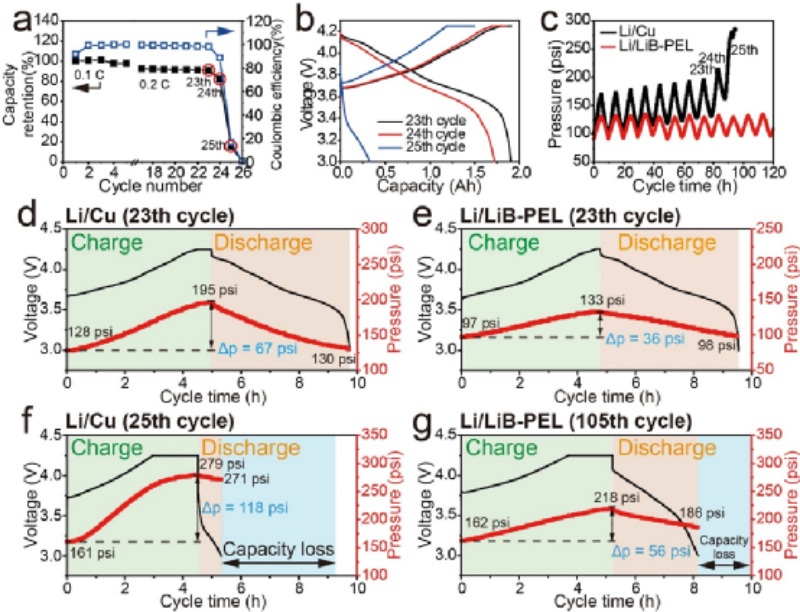
Figure 4 (a) Cycling performance of a multilayer (10-layer) pouch lithium metal battery with NMC83 cathode and Li/Cu anode. (b) The corresponding charge-discharge curves of the pouch lithium metal battery from the 23rd to 25th cycle and (c) the pressure data recorded during the cycle. The charge-discharge and in-situ pressure curves of the pouch lithium metal battery using Li/Cu anode at (d) 23rd cycle and (f) 25th cycle. The charge-discharge and in-situ pressure curves of the pouch lithium metal battery using Li/LiB-PEL anode at (e) 23rd cycle and (g) (g) 105th cycle.
Since pressure greatly affects the anode surface morphology and cycling performance of lithium metal battery, the pressure evolution process inside pouch lithium metal battery is monitored in situ. A pouch lithium metal battery with a capacity of 2.1 Ah was fabricated using Li/Cu or Li/LiB-PEL anode and 30 mg cm-2 NMC83 cathode. A pouch lithium metal battery was held between the test fixtures together with the pressure sensor and cycled at an initial pressure of ~80psi. The cycling performance of the multilayer (10-layer) pouch lithium metal battery with NMC83 cathode and Li/Cu anode is shown in Fig. 4a. During the last 3 cycles of the charge-discharge test (from the 23rd to the 25th cycle), the capacity loss of the battery was 1.58 Ah (Fig. 4b).
Figure 4c pressure data shows that the Li/LiB-PEL anode exhibits smaller pressure fluctuations during cycling.The pressure change (Δp) during charging of the pouch lithium metal battery with Li/Cu anode is about 67 psi. For the Li/LiB-PEL anode, Δp is about 36 psi, which is only 53.7% of the pressure change of the Li/Cu anode (Fig. 4d,e). LiB alloy fibers provide a low-expansion three-dimensional framework that can efficiently accommodate active lithium, thereby reducing pressure changes during cycling. The morphology of conventional 2D Li/Cu anodes is severely damaged after cycling, and side reaction products gradually accumulate as the active Li source is continuously consumed during cycling. This part of "dead lithium" is the cause of the residual pressure in the pouch lithium metal battery, and the loss of active lithium and the depletion of the electrolyte are the main reasons for the failure of the pouch lithium metal battery.
5.Cycle performance test of Ah grade pouch lithium metal battery
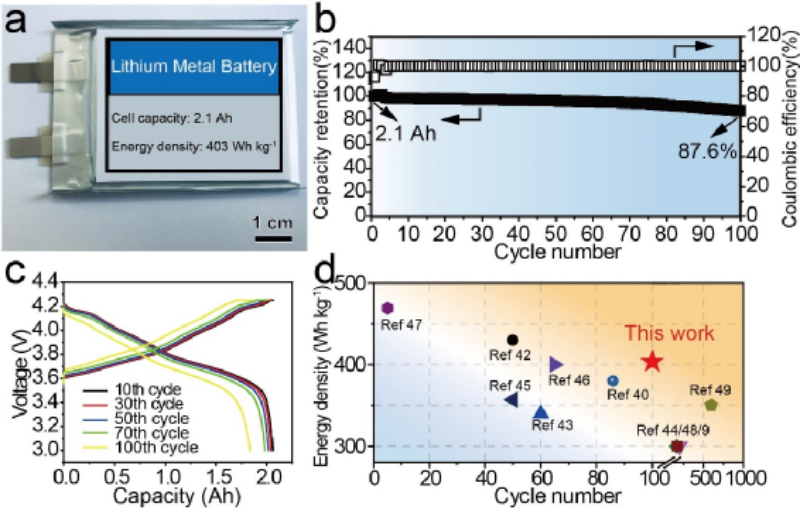
Figure 5 (a) Optical photograph of a 2.1 Ah pouch lithium metal battery using Li/LiB-PEL as the anode. (b) Cycling performance and (c) charge-discharge curves of the corresponding pouch lithium metal battery and (d) performance comparison with the reported pouch lithium metal battery.
The 2.1 Ahpouch lithium metal battery assembled with a three-dimensional Li/LiB-PEL anode protected by a polymer solid electrolyte layer and a highly loaded NMC83 cathode has a specific energy of 403 Wh kg-1 (Fig. 5a). Benefiting from the low-expansion three-dimensional LiB fiber structure and the LiF-rich built-in interface, the LiB/Li-PEL anode can effectively reduce the huge internal pressure change during cycling and inhibit the growth of lithium dendrites at the interface, thereby achieving high coulombic efficiency and cycling stability of the pouch lithium metal battery. After 100 cycles, the capacity retention rate of the battery was 87.6 % (Fig. 5b). The pouch lithium metal battery has an initial capacity of 2.1 Ah (0.1C), and the NMC83 cathode provides a reversible discharge capacity of up to 203 mAh g-1 (Fig. 5c). In the Ah-grade pouch lithium metal battery with high nickel material as the cathode, the battery exhibits relatively excellent performance of cycle stability and energy density (Fig. 5d).
6.Conclusion
In this paper, a three-dimensional low-expansion lithium anode protected by a LiF-rich interface is formed by reacting a polymer solid electrolyte with the active lithium inside the partially delithiated Li/LiB anode. Due to the high interfacial energy of LiF, the three-dimensional LiB framework exhibits good expansion resistance, which can achieve uniform lithium deposition/stripping on the electrolyte/lithium anode interface with little internal pressure change during cycling. The as-prepared Li/LiB-PEL anode exhibits 1000 h cycle stability and an average Coulombic efficiency as high as 99.2 % under high areal capacity test conditions of 5 mAh cm-2. The specific energy density of the 2.1 Ah metal lipo battery based on Li/LiB-PEL anode is 403 Wh kg-1, and the capacity retention rate is 87.6 % after 100 stable cycles. This study provides a new idea for realizing stable Ah-level pouch lithium metal battery with high energy density.
Related article: lithium deep cycle battery, solid-state lithium-ion battery