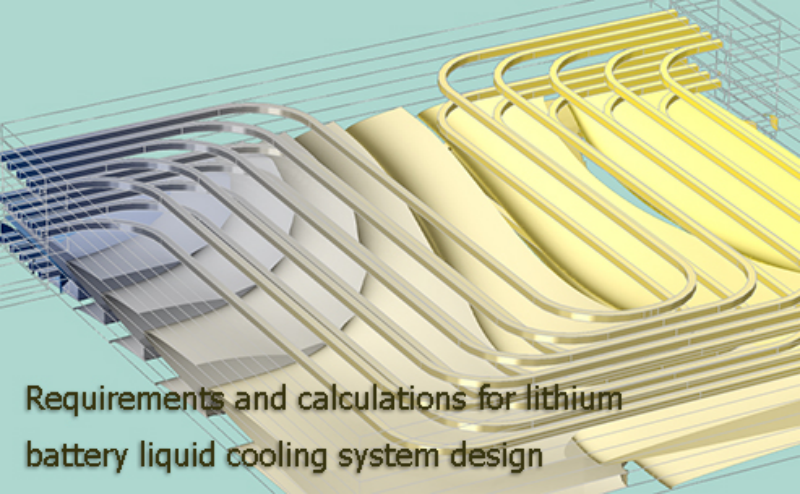
Main content:
- Demand for import
- Type and parameters of the cell
- Battery pack design information
- Structural layout of battery pack
- Maximum heating power of the system (full life cycle of the battery, full working conditions of the vehicle)
- Application of extreme environment (temperature)
- Battery pack thermal management goals
- Overall design
- Calculation
- Lithium battery heating rate calculation
- Calculation of the calorific value of the battery pack
- Selection and calculation of monolithic radiator
- Calculation of heat dissipation design of the system
- Calculation of low temperature heating power
- Reasonable preheating power estimation
- Calculation of installation and fixing strength
Temperature is the most important factor in the aging process of power lithium batteries. Obtaining a suitable working temperature can slow down the aging of the battery and exert the best performance of the battery. In the power lithium ion battery pack, hundreds of thousands of battery cells are integrated into a system, and the consistency of single cell performance directly affects the overall performance and life of the battery pack.
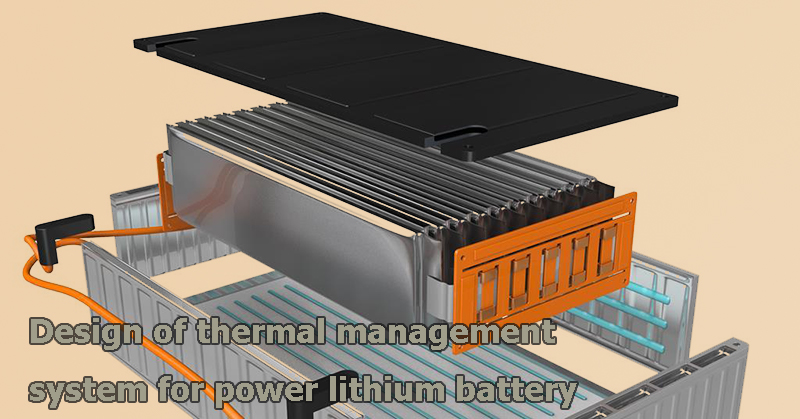
At different positions in the battery pack, the natural heat dissipation conditions vary widely. In order to obtain a consistent aging progress, it is necessary to create a consistent working temperature. There are two design goals for the thermal management system of the power lithium battery: 1) Keep the inside of the battery pack within a reasonable temperature range; 2) Ensure that the temperature difference between different cells is as small as possible.
1.Demand for import
In the design of a project, the first step must be to clarify the customer's needs. In addition to general needs, you should also put yourself in the shoes of the surrounding needs. Even if the customer does not mention it, we'd better consider it privately in advance. For liquid cooling systems, the basic requirements for power lithium battery packs are shown in the items listed below. In addition, this article is directed to the case of indirect cooling.
① Type and parameters of the cell
Lithium battery system selection, different material systems, bring differences in thermal characteristics. Take the current mainstream lithium manganate, lithium iron phosphate and ternary lithium as examples. Lithium manganate has good low temperature characteristics, but poor high temperature aging resistance, short lifespan and medium energy density. Lithium iron phosphate has poor low-temperature discharge capacity, good high-temperature performance, and low energy density. The high and low temperature performance of ternary lithium is in the upper middle, the energy density is high, the life is long, but the relative safety is low.
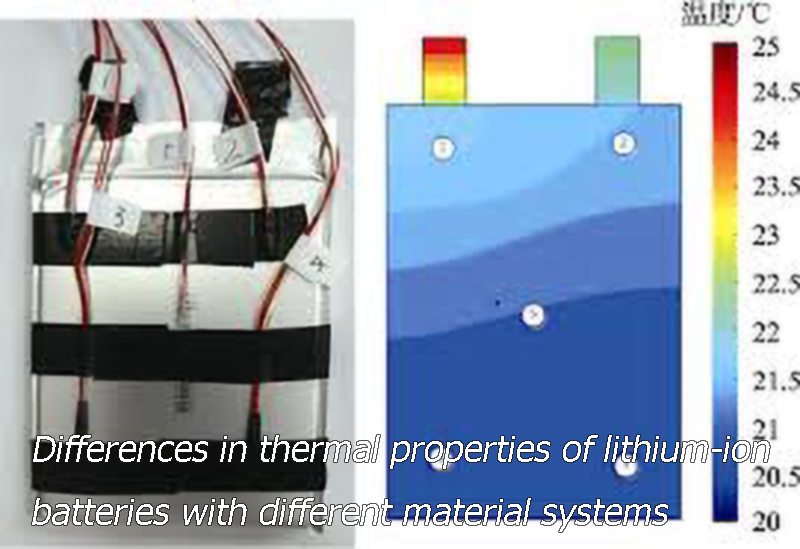
Cell selection is to select the type of lithium battery according to the main requirements such as energy density, power density, cycle performance, and cost constraints. The calculation parameters of heat source for thermal management can be determined only when the type of electric cell is determined. The battery parameters concerned by the thermal management system include: nominal voltage and voltage range, maximum continuous operating current, energy density, power density, battery internal resistance (new battery and end of life stage), thermal characteristic parameters (equivalent specific heat capacity, equivalent heat conduction coefficient).
② Battery pack design information
How many series and parallel the battery pack consists of, the equivalent connection resistance value, the structural design form, and the possible radiator arrangement form.
③ Structural layout of battery pack
The shape and size of the battery pack box, the distribution of battery modules, and the location of high and low voltage cables.
④ Maximum heating power of the system (full life cycle of the battery, full working conditions of the vehicle)
The continuous maximum power that the cells, modules and battery packs can achieve as a whole and the heating power under corresponding conditions, the continuous maximum heating power after considering various aging factors at the end of the battery life, the maximum heating power and duration in the vehicle operating conditions, The maximum heating power and duration of the car's continuous operation at the highest speed. Another requirement that needs to be determined, the maximum heating power of the system, whether the thermal runaway situation needs to be considered.
⑤ Application of extreme environment (temperature)
Maximum ambient temperature and duration, minimum ambient temperature and duration for the vehicle's target sales area.
⑥ Battery pack thermal management goals
The objectives mainly include the maximum and minimum operating temperature range and maximum temperature difference.
2.Overall design
The overall design, according to the input requirements, generally considers the frame of the cooling system. According to the system heating power density and sealing, allowable temperature range, cost requirements, etc., select a suitable cooling method, and preliminarily determine the type of radiator and heating method. Refer to the reserved space of the vehicle, and generally consider the arrangement and fixing method of the equipment.
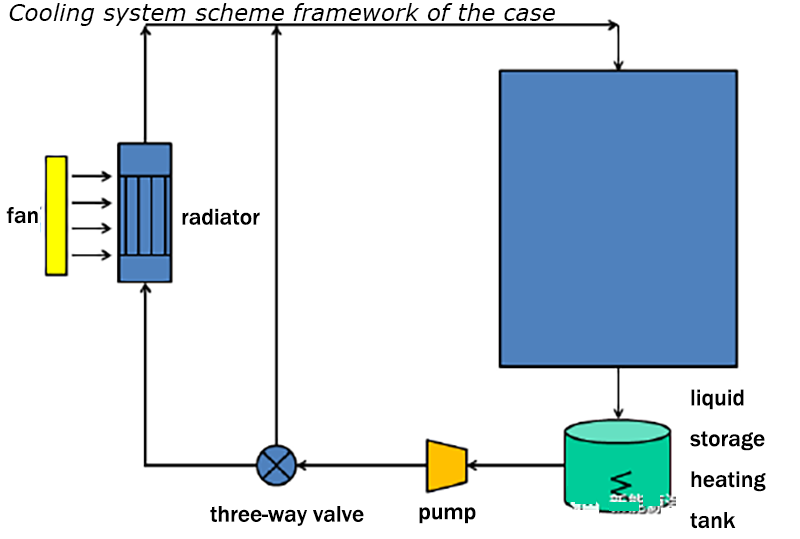
3.Calculation
① Lithium battery heating rate calculation
According to the understanding of the electrochemical reaction process of lithium batteries, the heat in the charging and discharging process is usually divided into four parts: reaction heat, ohmic heat, polarization heat and side reaction heat. For new cells, the proportion of side reaction heat is very small and can be ignored. But later in the life of the battery, this simplification may introduce large deviations. A heavily simplified model is shown in this formula:

Among them, the coefficients K represent the thermal conductivity of the lithium battery in the length, width and height directions, T is the temperature, q is the heat generation rate per unit volume of the battery, ρ represents the battery density, cp is the battery specific heat capacity, and t is the time. This model simplifies other heat transfer modes and only retains the main form of heat transfer inside the battery - heat conduction.
Heat is only generated in the center of the cell, which is quite different from the actual structure of the cell. System parameters, regardless of the situation that changes with temperature, set the thermal conductivity and heat capacity as constants. For the value of thermal conductivity in each direction, there is an idea that the value is obtained according to the weighted average of various constituent materials in the cell.
There are a large number of studies on the thermal model of lithium battery cells, some of which consider the actual physical form of winding or stacking of the cells, setting each layer as a heat source, and there is a process of heat transfer between layers. Some describe the heating situation of different components inside the cell in detail, and integrate the action of various heat sources to generate heat from the inside of the cell and spread it in three-dimensional space.
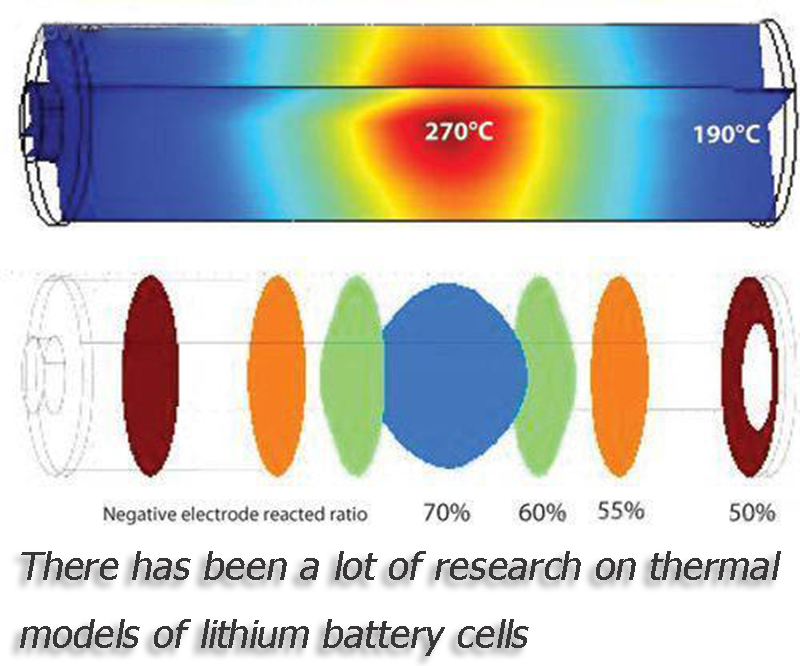
When designing the form of the radiator or the heat collecting plate and its placement in the battery module, which part of the cell generates heat and which point has the highest temperature will have a definite impact on the design result. However, in the face of battery thermal management system design, the main impact of a single cell is heat generation and heat generation rate. Too many details take up computing resources. Next, the heat generation rate q in the previous formula needs to be calculated, and the formula comes from the classical heat generation rate model:
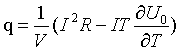
Among them, V is the volume of the cell; I is the current of the cell; T is the temperature of the cell; R is the internal resistance of the battery; 5 mv /k; I^2R represents the ohmic heat, and the term of the partial derivative of U0 to T represents the reversible heat of the battery. This heat generation rate model links the heat generation rate with the parameters that can be measured by the battery, which is convenient for practical application. If a constant current value is selected, the heat generation rate can be directly calculated.
② Calculation of the calorific value of the battery pack
In the battery module, in addition to the internal resistance of the battery cell, there is also a connection resistance. The single cell is connected to form a battery pack, the contact resistance between the cell and the connecting conductor and the self-resistance of the connecting conductor; High-voltage wires or copper and aluminum bars are used to connect the battery modules to the modules, and there are contact resistance and internal resistance of the wires.
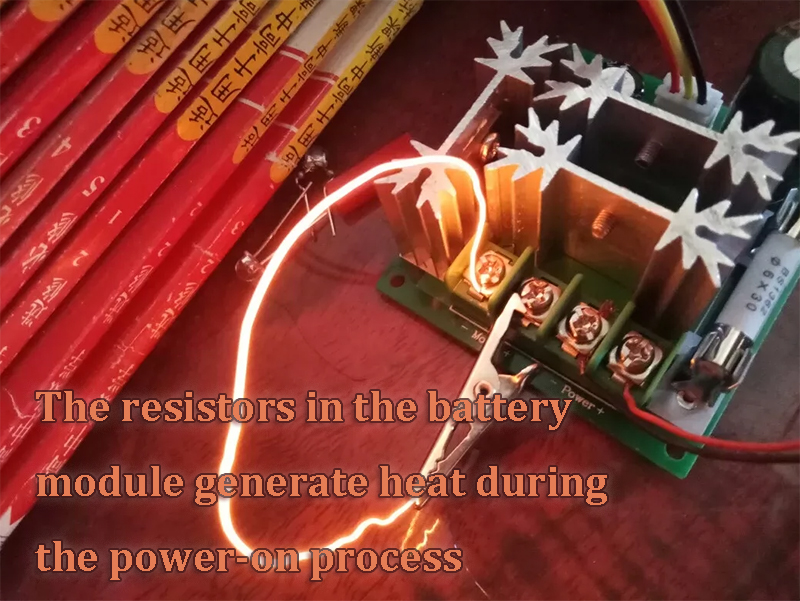
During the power-on process, the above resistors will generate heat. For battery modules with the same connection form, the overall internal resistance can be measured, or an estimated value can be given based on experience, which can be used when establishing a simulation model, and then adjusted according to the experimental verification results. The calorific value of the battery pack is calculated according to the sum of the calorific value of all cells in the battery pack and the sum of the calorific value of the connection resistance.
③ Selection and calculation of monolithic radiator
There are various forms of radiators, including flat radiators, heat pipe radiators, phase change material components, aluminum plate composite heat pipe radiators and so on. According to the heat dissipation capacity of the single radiator, the contact area between the radiator and the battery pack and the heat exchange area between the radiator and the liquid cooling circuit are designed.
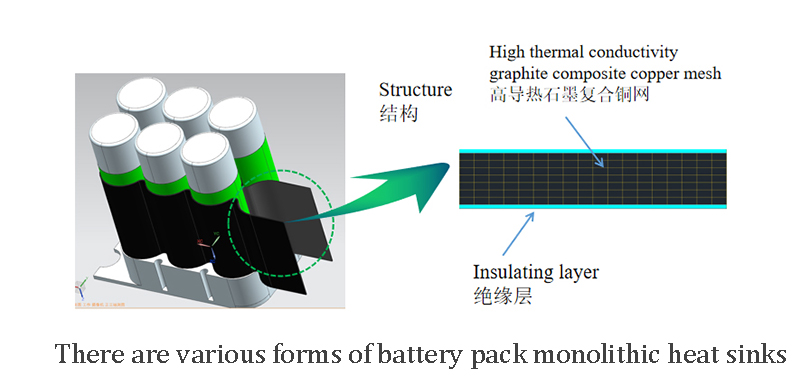
The shape of the contact surface of the heat sink needs to be determined according to the shape of the battery cell and the arrangement of the cells in the battery pack. On the one hand, it is desirable to obtain the largest heat dissipation area between the heat sink and the battery. On the other hand, the cells in different positions need to maintain the same contact area with the heat sink.
There is a problem here. Compared with the battery cells farther away from the cooling water pipe, the temperature of the coolant flowing through it is lower. In theory, the temperature rise of the coolant can be offset by adjusting the contact area at different positions. Impact. However, the interchangeability of this design is too poor in engineering. Without a certain batch, the cost will rise significantly. The picture below shows the matching of the serpentine tube and the cylindrical battery in the case.
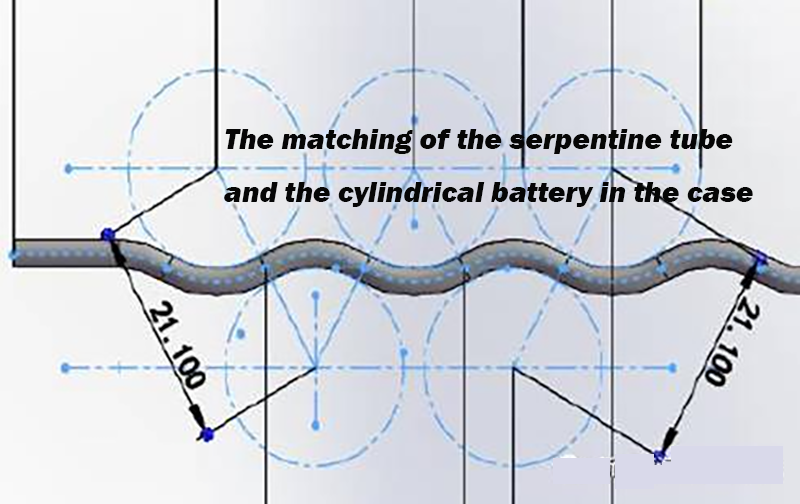
④ Calculation of heat dissipation design of the system
Confirm the coolant type based on the application environment and temperature range. The total number of radiators used in the battery pack cooling system and the sum of their heat dissipation capacity are the minimum requirements for the coolant circulation system. According to this requirement, select the piping size and piping arrangement of the circulation system. Confirm the series-parallel relationship between heat sinks; Confirm the inlet and outlet temperature, pressure and flow of coolant; confirm the head of the pump; confirm the power of the refrigeration unit.
⑤ Calculation of low temperature heating power
The general idea is to realize that there are actually two heat transfer processes going on during the low-temperature heating process, one is that the heater heats all the components of the battery pack, and the other is that the battery pack box dissipates heat to the surrounding environment. During the heating process, the components of various materials inside the battery pack are calculated to calculate how much heat is required to heat from a low temperature to an ideal temperature.
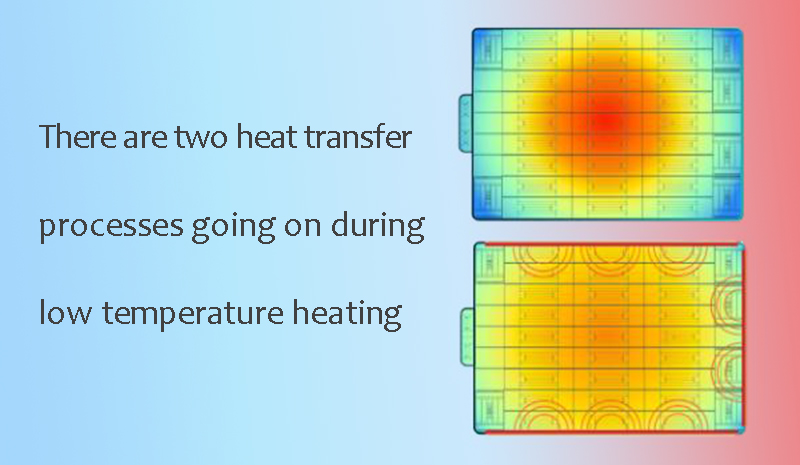
In the process of heat dissipation, during the heating process of the heater, the heat absorption temperature of the battery pack box rises, and at the same time, it dissipates heat to the surrounding environment. This is a dynamic heat dissipation process, the temperature of the high temperature part rises continuously, and the low temperature ambient temperature remains unchanged. The heat dissipation process is mainly carried out in two ways of heat transfer, convection heat transfer and heat radiation.
The types of components in the battery pack generally include cells, high and low voltage wires, structural components for fixing cells, radiators for cooling systems, cooling system pipelines, battery boxes, battery management systems BMS, and sensors. The following table is a general classification of the materials in the box by the case authors. Calculate the sum of all the heat required to heat up the battery pack components and the heat dissipated by the box to obtain the total heat of heating. Then according to the specific requirements of the heating time, the corresponding heating power is obtained.
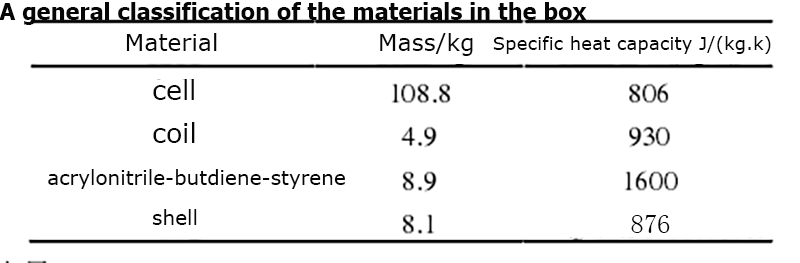
⑥ Reasonable preheating power estimation
Preheating here means that in a low temperature climate, when the vehicle is parked for a long time, the temperature of the radiator, pipeline and coolant of the battery pack and thermal management system is extremely low. If rely on the power of the lithium battery for heating, on the one hand, the temperature is too low, which may be lower than the lower limit temperature of the battery's allowable discharge, and it is impossible to achieve power supply heating. In another situation, even if the power supply can be supplied, the internal resistance of the system is large and the discharge capability is poor.
And the battery system itself consumes a large amount of power, the power consumption directly affects the subsequent battery life. In order to cope with this situation, some designers have considered the warm-up strategy. When the temperature of the battery pack is too low, the battery pack is not allowed to discharge, and the vehicle owner is required to turn on the external power supply to supply power to the heating system in the battery pack, and the vehicle is in a prohibited state. During the preheating process, the cooling medium fills the cooling circuit and is able to capture heat together with the battery pack.
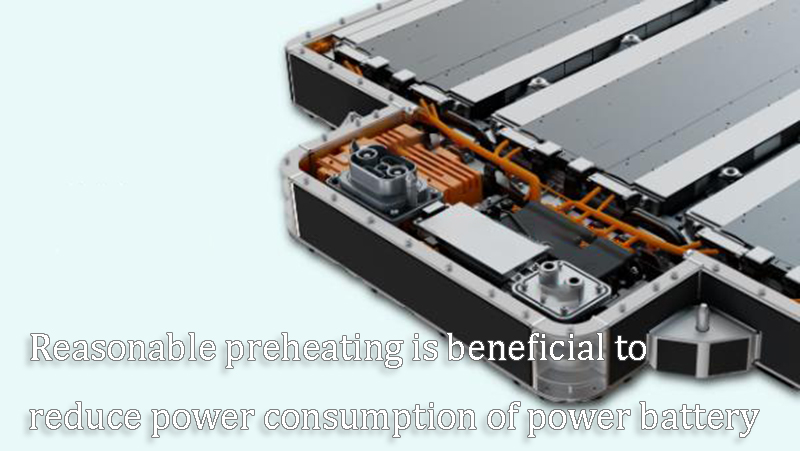
After the warm-up process is over and the vehicle starts to run, the battery itself will generate heat to maintain the temperature in the battery pack. In this way, a large amount of power from the power battery is avoided to be used for heating. As long as the warm-up time is not delayed for too long, it will greatly benefit the user experience. The calculation of the preheating power is similar to the calculation process of the previous low temperature heating, but the preheating needs to consider the situation that the cooling circuit is full of coolant.
⑦ Calculation of installation and fixing strength
The thermal management system of the battery pack is partly installed inside the battery pack and partly directly on the body. Each installation, fixing and structural design needs to consider its own strength and fixing strength. The calculation method of installation and fixing strength is the same as that of other components in the battery pack. After learning about the design of lithium battery liquid cooling system, maybe you are also interested in the recycling of power batteries. You can read car battery recycling on our website for more details.