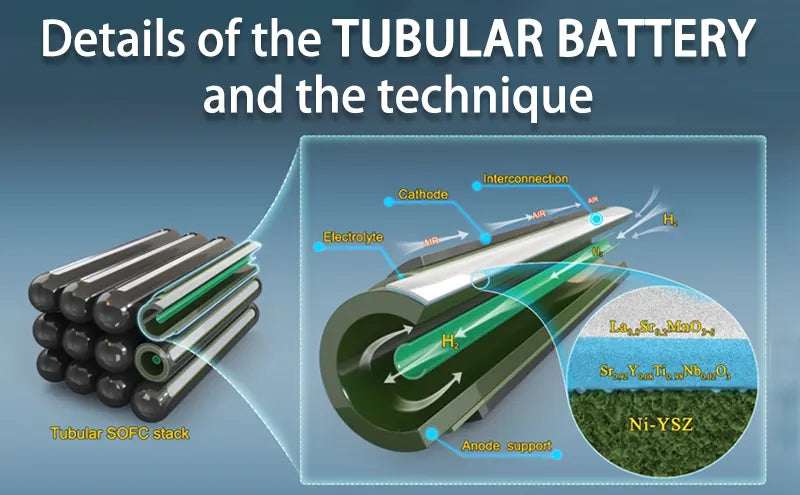
Main content:
The tubular battery is an ideal power generation device because of its advantages: fast start-stop speed, good thermal cycle stability, high conversion efficiency, a wide range of fuel applications, and no emissions pollution.
This article also discusses the structure of the battery, preparation methods, and key material parts. And advanced strategies and programs to solve tubular battery problems, providing understanding for the high-quality development and commercial application of tubular battery technology.
1. Introduction to tubular battery technology
Tubular battery is a green, stable and reliable power generation device that efficiently converts chemical energy from fuels into electrical energy. And because of its unique configuration and advantages similar to the lifepo4 battery, it has great application potential, including:
- Fast start-stop speed
- Strong thermal shock resistance
- Good cycling stability
- High mechanical strength
- Easy to seal at high temperatures
Tubular battery is composed of porous cathode and anode, dense electrolyte and other components in tubular form in a certain order. The electrical connection and current transmission are achieved by the connector and the collector, respectively, and the internal hollow channel is generally the fuel flow channel.
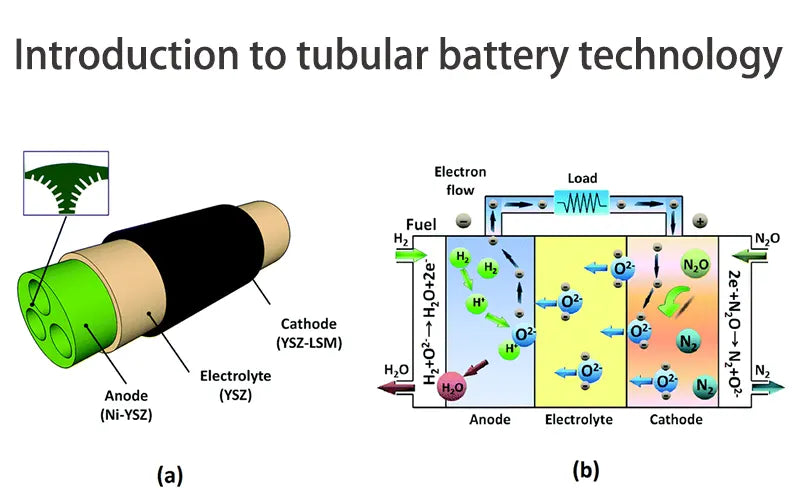
According to the characteristics of ion transport in the electrolyte, tubular battery can be divided into two categories: oxygen ion conductor types and proton conductor type. According to the battery support structure, it can be divided into self-supporting type (cathode support, anode support, electrolyte support) and external support type (metal support, inert matrix support).
2. The structure of the tubular battery
Tubular battery has two structures: self-supporting type and external support type. The self-supporting type includes electrolyte support and electrode support, while the external support type has metal support and inert matrix support.
The structure of the tubular battery has undergone a development process from electrolyte support to cathode support to anode support, and in recent years it has tended towards external support.
● Electrolyte support type
Most of the earliest tubular batteries were electrolyte-supported. Due to the high density and thickness of the electrolyte support, this type of battery has excellent airtightness and mechanical strength.
However, as the thickness of the electrolyte increases, the ohmic resistance increases rapidly, and the battery power density will drop significantly. Therefore, the current focus of the tubular battery is mostly on the electrode support type or external support type.
● Cathode support type
Cathode supported tubular batteries are characterized in that the ohmic resistance of the battery is reduced, and the anode side is less affected by carbon deposition when using hydrocarbon fuels. However, this structure will make Cathode's polarization loss large, and the high price of cathode materials limits its large-scale application.
● Anode support type
The anode support type is the most commonly used structural form. The battery of this structure can operate efficiently at medium temperatures thanks to the electrolyte and cathode deposited on the anode substrate in a thin film form with low ohmic resistance and cathodic polarization.
Moreover, it is difficult and less expensive to manufacture, and is suitable for large-scale applications. However, the top 10 lithium ion battery anode material companies found it during the manufacturing process that the fuel gas has a large diffusion resistance in the thick anode and is easily affected by carbon deposition.
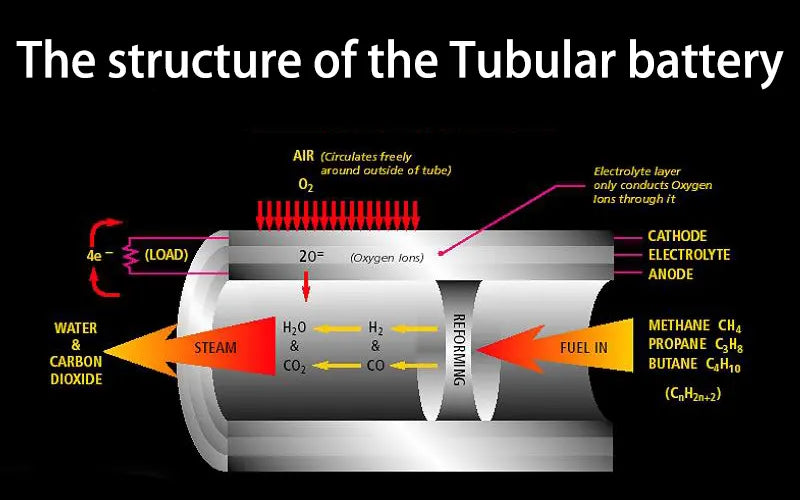
The porosity and pore size in the support body are distributed in a gradient, which has a good gas diffusion effect while meeting the requirements of support strength, and the battery shows good electrical output performance. In addition, the honeycomb structure makes the battery have excellent thermal cycling and mechanical stability, and the battery durability is good.
● Metal support type
In order to further improve power generation efficiency and mechanical stability and reduce production costs, metal support types have attracted attention. Compared to other self-supporting batteries, its advantages are:
- Higher mechanical strength
- Better impact resistance
- Low ohmic and polarization losses
- Less difficult and costly to prepare
- Suitable for use in medium and low temperature environments
The fuel gas can pass smoothly through the copper support layer and distribute evenly to the active part on the anode side, ensuring an efficient oxidation reaction. However, at present, metal-supported batteries still have problems such as poor corrosion resistance and low redox cycle stability.
Its working life is lower than that of batteries using ceramic-based materials as supports, and these technical difficulties still need to be overcome. In addition to metal-supported tubular battery, an inert matrix support method has also been developed in recent years.
● Inert matrix support type
This structure gives the battery high thermal cycling stability, and the support can be used as a catalyst carrier. When using hydrocarbon fuel, the influence of carbon deposition on the catalytic activity of the electrode can be suppressed to a certain extent, which has advantages in durability.
However, the inert matrix-supported tubular battery has a long current path on the anode side and a large overall ohmic resistance. When using the same electrode and electrolyte material, the battery has a lower power density than an anode-supported battery.
3. Preparation method and characteristics
The preparation method can control the microstructure and quality of the battery module, which is a key factor affecting the performance of the battery, and it is extremely important to select the appropriate preparation method and operating process for different types of tubular batteries.
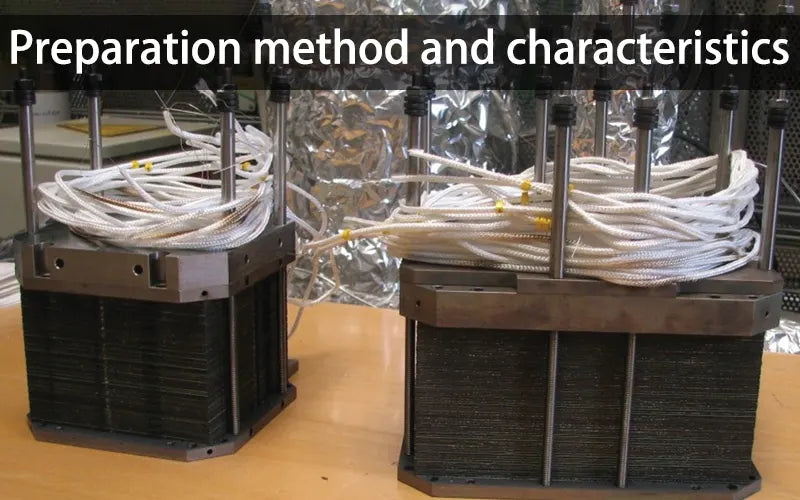
Tubular supports can be prepared by extrusion, phase conversion, gel injection molding and isostatic pressing, while tubular thin film electrolytes or electrodes are generally prepared by dipping coating technology, brushing, and electrochemical deposition.
At present, more mature methods for preparing tubular battery supports include extrusion, gel injection molding and isostatic pressing. They all have the advantages of easy operation, simple equipment and low production costs.
● Extrusion
However, tubular components prepared by extrusion are easy to deform during drying and sintering.
● Gel injection molding
The gel injection molding method has the problem that the uniformity inside the component is difficult to control and the quality stability is poor.
● Isostatic pressing
The disadvantage of the isostatic pressing method is that the preparation is time-consuming, and the small components have high requirements for molding.
● Phase conversion
Phase conversion method is one of the most studied methods for preparing tubular support in recent years. Its advantages are high production efficiency, fewer defects in the prepared components, and good quality, but the preparation of slurry is a technical difficulty.
In the preparation of tubular thin film electrolytes or electrodes, dip coating technology and electrochemical deposition are the most commonly used methods. Impregnation coating technology is characterized by precise control of component thickness.
However, production is slow and inefficient. The electrochemical deposition method is simpler. And for different component materials, extensive testing is required to determine the right conditions, otherwise component performance can be severely affected.
In recent years, with the continuous development of 3D printing technology, tubular battery components with complex geometries and microstructures can be manufactured efficiently and accurately, and proton conductive half cells have been successfully prepared using this technology. However, the machinery used in this method is complex, costly, and not suitable for the production of large-scale components.
4. Tubular battery electrolyte material
Oxygen ion conductor oxides are the most common electrolyte materials in tubular batteries. Zirconia-based materials (such as YSZ, ScSZ) are typical representatives, they have high conductivity at high temperatures (700 to 1000 °C) and good redox stability, but the ionic conductivity decreases rapidly with the decrease in temperature.
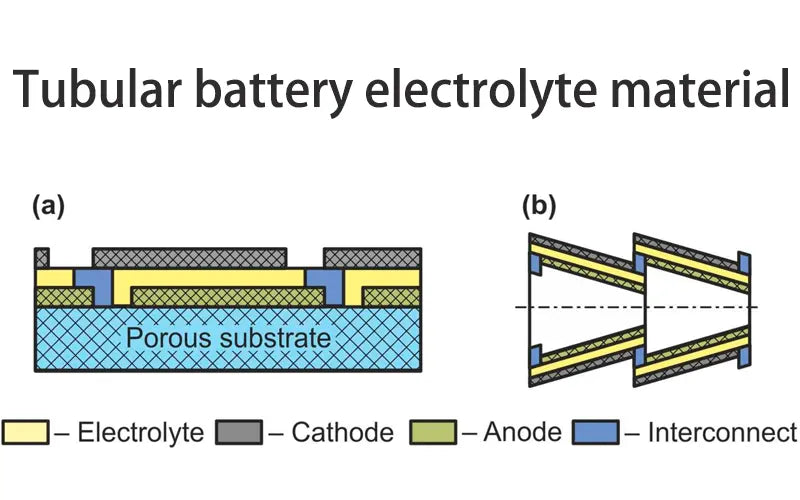
In order to meet the low temperature development of tubular battery and reduce material costs, CeO2-based materials such as GDC and SDC are used as electrolytes, and their ionic conductivity is several times that of YSZ at medium temperature.
In recent years, proton conductor electrolyte has developed rapidly, and the top 5 battery electrolyte companies propos solutions to the problems of this electrolyte. Related materials used in tubular batteries include BCY, BZY20, BCZY and BZCYYb.
Although many characteristics of such electrolytes are not clearly understood, and the technology is still immature, they generally have high ionic conductivity under medium and low temperature conditions (400 to 600 °C). Good electrochemical properties and high mechanical stability make it possible for tubular battery to have low temperatures and long life.
5. Tubular battery electrode material
At present, the vast majority of anode materials used in tubular batteries are Ni-based, and only a few are ceramic-based.
● Ni base
Among these common anode materials, Ni-YSZ has the most extensive application due to its high electrocatalytic activity and mature preparation technology. However, Ni-based anodes are susceptible to carbon deposition and sulfur toxicity when using hydrocarbon fuels, which destroys the electrocatalytic activity and structural stability of the anode.
● Ceramic base
In terms of the anode material of the proton conductor type tubular battery, the anode can maintain electrocatalytic activity well, and the power density is very good. The catalyst layer deposited inside the anode has better long-term working stability.
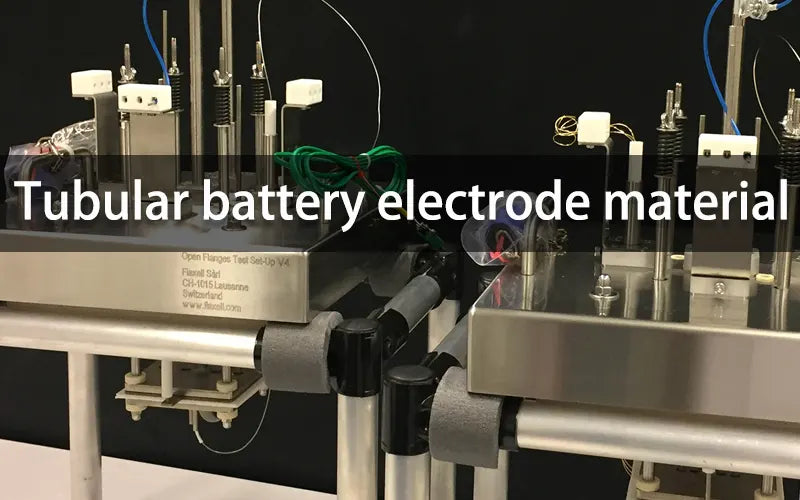
In terms of cathode materials, it can currently be divided into co-based, co-free, and composite materials. Among the common cathode materials for tubular batteries, LSCF and LSM are the most common.
6. Conclusion
Tubular battery has the unique advantages of high efficiency, fast start-stop speed, good thermal cycle stability and high mechanical strength. This article introduces tubular battery from the perspectives of battery structure, preparation technology and key materials.
- At present, the most mature and comprehensive tubular battery is the anodic support type, and the external support type (metal support and inert matrix support) battery structure is an important direction for the development of high-performance batteries.
- Common methods for preparing tubular batteries include extrusion methods, phase conversion methods, coextrusion technology based on phase transition and impregnation coating technology, etc., and laser 3D printing technology has also been applied to the preparation of tubular battery in recent years.
- The low-temperature development of tubular battery has new requirements for various key materials. For electrolyte materials, proton conductive oxides exhibit high conductivity at medium and low temperatures, attracting increasing attention. For electrode materials, synergistic optimization of their electro catalytic activity, electrical conductivity and durability, as well as reduction of thermal expansion coefficient and cost are the focus of research.
Related articles: gel battery vs agm, battery thermal management, cathode and anode