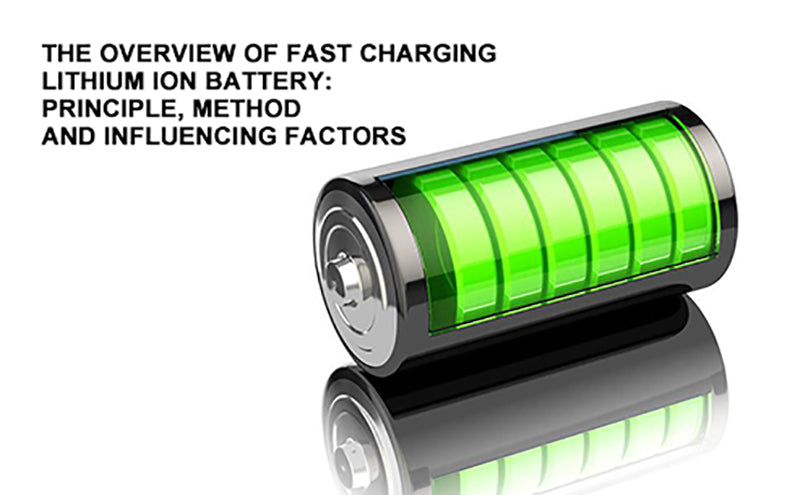
1.The background of fast charging lithium ion battery
The widespread use of lithium-ion batteries in pure electric vehicles has accelerated in recent years to limit the effects of climate change and air pollution. However, compared with traditional fuel vehicles, range anxiety, long charging time and other problems have become the main obstacles to the development of electric vehicles. Thus, the improvement of fast charging capability has become a common development goal for battery manufacturers and oems. However, the results show that low temperature and high charging rate will accelerate the degradation of battery capacity and output power. On the other hand, the large amount of heat generated during battery charging is difficult to disperse evenly and effectively, which can also cause decay acceleration and other safety issues. FIG. 1 shows the factors affecting fast charging lithium ion battery from atomic level to vehicle system level. This paper focuses on the review and summary of the existing literature and analyzes the key technical constraints at each level.
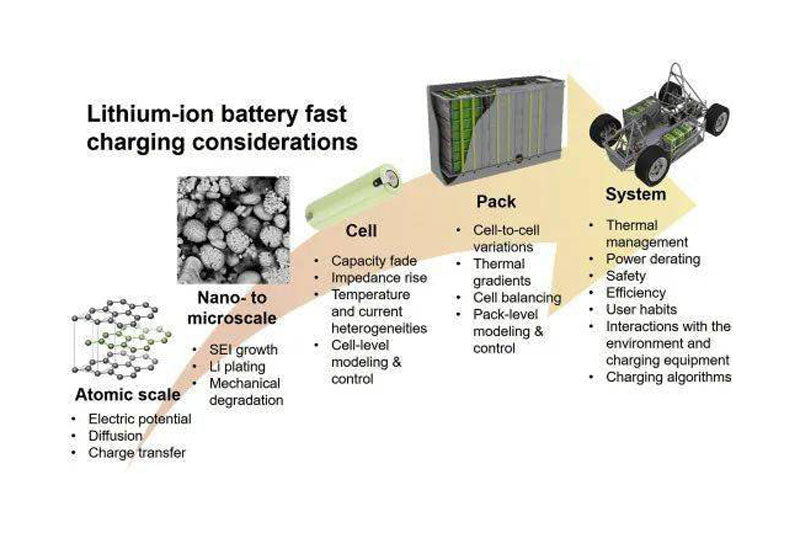
FIG. 1 Factors affecting fast charging lithium ion battery at different levels
Electric vehicle charging categories include AC and DC, with DC charging faster. Tesla is the first company to use 120kW fast charging; Although great progress has been made in improving electric vehicle charging power, these fast charging technologies are not suitable for all situations. According to the specific working conditions and charging environment of the electric vehicle, the charging power will gradually decay during the continuous charging process. In addition, in fast-charge mode, due to safety and other factors, the battery can only be charged to 80% capacity. At higher power, the charging rate will gradually decrease to avoid overcharging. In addition, charging power is limited by the battery management system (BMS). The industry is increasingly interested in the field of rapid battery charging, so it is necessary to understand the speed determination steps of different charging methods and their impact on battery life. Based on the multi-scale and multi-disciplinary characteristics of fast charging, this paper aims to establish the relationship between micro processes, material properties, battery and Pack design, and charging strategy optimization.
2.The principle of battery fast charging
The ideal battery should show the characteristics of long life, high energy density and high power density, so as to be able to charge and recharge quickly at any place and at any temperature to meet the requirements of electric vehicles for long distance driving. However, there is a trade-off relationship between these physical characteristics, and the influence of the temperature of the material and the device determines the usage threshold of the battery. When the temperature drops, both the charging rate and the maximum voltage should be reduced to ensure safety, making temperature a key limiting factor for fast charging. As the temperature decreases, the risk of lithium separation increases significantly. Although many researchers have pointed out that Lithium plating often occurs at temperatures below 25℃, it can also occur at high temperatures, especially at high charging rates and energy densities. In addition, the fast charging efficiency is also closely related to temperature. The charging efficiency of 50kW charging pile is 93% at 25℃, but as low as 39% at -25℃, mainly because BMS limits the rated power at low temperature.
Common lithium-ion batteries are mainly composed of graphite anode, lithium metal oxide anode, electrolyte, fluid collector and porous diaphragm. As shown in FIG.2, Li+ is transferred from the positive electrode to the negative electrode through the electrolyte during charging, and the main transmission path is as follows: 1) through the solid electrode; 2) Electrode/electrolyte interface through positive and negative electrodes; 3) Through the electrolyte, including Li+ solvation and de-solvation. However, improper use conditions of batteries often cause a series of side effects that affect performance and life. In addition, charging and discharging rate, battery internal resistance and battery polarization will affect the thermal characteristics of the battery, such as increasing heat production, reducing the charging efficiency and safety.
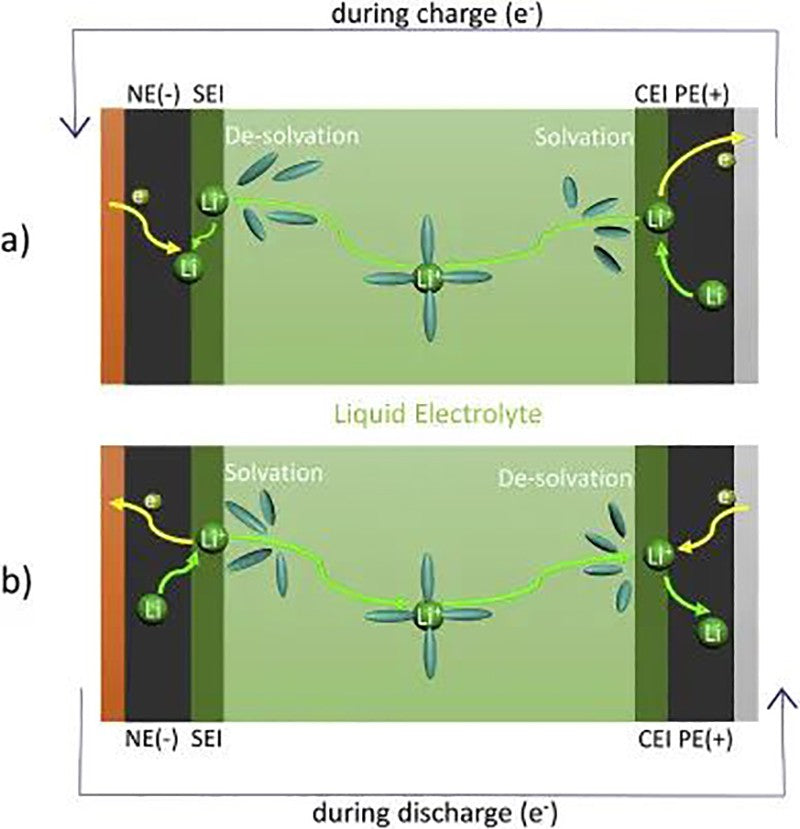
FIG. 2 Lithium ion transfer a) charge, b) discharge
A large number of studies have shown that the decay of the positive electrode and the growth of the positive CEI film have no influence on the fast charging speed of the traditional lithium ion system, so the negative electrode has become the main object of concern in the charging process. Under certain circumstances, lithium metal may continue to precipitate into lithium dendrites, or even Pierce the diaphragm to cause internal short circuit. The factors affecting the deposition and structure of lithium include the diffusion rate of lithium ions at the anode, the concentration gradient of electrolyte at the anode interface, the deposition of metal salts and the side reactions at the electrode/electrolyte interface. The results show that the behavior of the anode can be attributed to the effect of the current at the beginning of lithium separation on the density resistance of the anode surface. It is very important to improve the fast charging ability of battery to reduce the negative internal resistance through battery design. In addition, the influence of temperature is also very important, too low or too high temperature will be considered to be harmful to the battery, but the high temperature of the battery during fast charging will be conducive to its balance, especially for the high specific energy battery. The effect of electrode thickness on charging performance also needs to be concerned. Thin electrodes are often considered ideal for lithium ion transport. As the electrodes are thickened, it becomes important to ensure sufficient lithium ion concentration at the electrode/electrolyte interface to maintain overpotential stability and reduce the possibility of Lithium plating. In the fast charging process of thick electrode batteries, lithium salts may deposit in the fluid collector, resulting in unbalanced electrode utilization and an increase in the current density of the diaphragm anode.
3.Attenuation effect of fast charging lithium ion battery
1) Temperature impact
Heat generation of lithium-ion batteries can be divided into reversible and irreversible processes. The expression of non-heat producing Qirr is as follows:

U is the open circuit voltage,Vbat is the battery voltage, and I is the current (while charging). Most of the irreversible heat comes from internal resistance:

Where R is the battery internal resistance. Joule heat is proportional to the square of the current, so when the current increases, the irreversible heat will increase significantly. Reversible heat Qrev comes from entropy change in electrochemical reaction, also known as entropy heat, and its expression is:
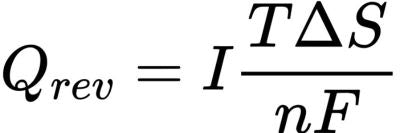
In lithium ion batteries, the heat distribution and loss of soft package, cylindrical and square shell batteries are unevenly distributed: for example, the surface thermal conductivity of some battery materials is poor, so the heat will accumulate in the core position more than the surface. In addition, current density and heat production rate vary from cell to cell. These inconsistencies are further amplified in larger batteries. The temperature in the inner center of the cylindrical cell is significantly higher than that on the surface. For soft packs or square cells, the temperature at the electrode lugs is significantly higher than at other locations. In addition, because the resistance of the positive aluminum collector is greater than that of the negative copper collector, the temperature of the positive electrode is often higher than that of the negative electrode.
The uneven distribution of heat generation not only exists in the cell, but also in the design of the thermal management system at the battery Pack level, because it has a significant impact on the temperature distribution in the Pack. Over time, different aging paths of cells will also have a significant impact on the uniformity of Pack heat generation, due to the increase in internal resistance of different cells. To address this problem, the design of a thermal management system is described in Part 6.

Many aging mechanisms in lithium ion batteries are temperature-dependent. At high temperature, SEI film grows faster in the negative electrode and becomes more loose and unstable. At low temperature, ion diffusion and reaction rate slow down, and the possibility of Lithium plating and lithium dendrite growth increases. Almost all aging reactions are accelerated at high temperatures; Low temperature can reduce the side reaction rate but also reduce the diffusion of active substances. If lithium metal is precipitated, the decay will be accelerated. In addition, the increase of low temperature polarization will lead to increased heat generation and reduced energy efficiency. In most cases, SEI film growth at the anode/electrolyte interface is the main decay mechanism. SEI film will increase the internal resistance of the battery, reduce the power, and then lead to capacity attenuation. At high temperatures (60˚C or more), the SEI group dissolves and decomposes, damaging the integrity of the negative protective film. In extreme cases, when the temperature of
fast charging lithium ion battery exceeds the safety threshold, thermal runaway may occur.
2) Influence of lithium plating
Lithium plating refers to the deposition of lithium ions in the electrolyte on the negative electrode as a Faraday side reaction of lithium metal, instead of embedding negative particles. Lithium plating may occur when the negative electrode potential drops below Li/Li+. In the process of Lithium plating, the lithium metal first forms droplet shape to reduce the surface energy, and the surface metal and electrolyte react quickly to form SEI film. As more lithium deposited under the SEI film until the SEI film broke, new SEI film was formed on the surface of lithium, and the concentration of lithium salt decreased gradually, and lithium metal began to grow perpendicular to the polar surface, forming lithium dendrites. Lithium dendrite growth is considered one of the worst side effects. If the dendrite punctures the membrane and reaches the positive electrode, an internal short circuit causes the battery to heat up quickly. Lithium metal is more reactive than the negative electrode, further causing internal side reactions, resulting in SEI growth, gas production and electrolyte dissolution.
Nondestructive lithium ion observation techniques are important for practical fast charging lithium ion battery applications. The common nondestructive lithium analysis observations use the external characteristics of the battery, including aging rate, lithium embedded voltage platform, model prediction and other methods. The increase in battery thickness may also lead to Lithium plating, but the mechanism needs to be further studied.
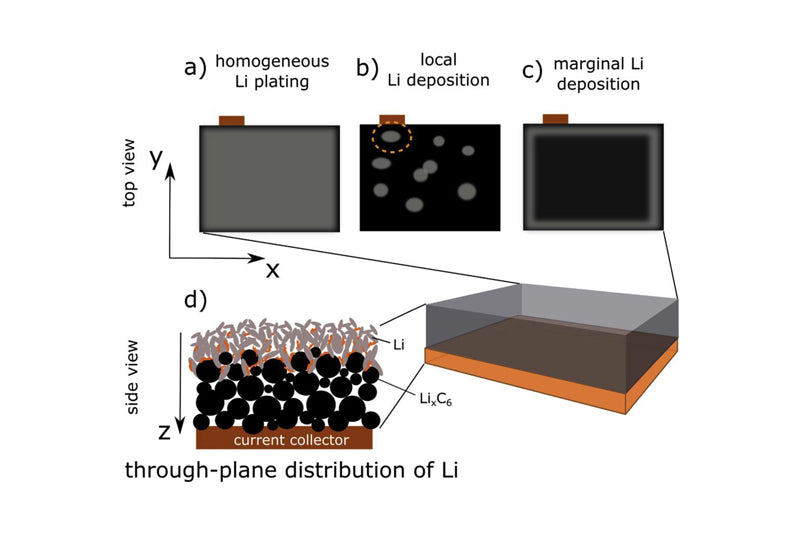
3) Mechanical influence
Mechanical chalking is another important aging phenomenon caused by fast charging lithium ion battery and has been demonstrated in a variety of electrode materials (graphite, NMC, LCO, NCA, Si, etc.). Mechanical attenuation can be divided into the following parts according to the scale: the fracture within the electrode particle, the separation of the electrode particle from the conductive carbon and the adhesive, the separation of the active material from the collector, and the electrode stratification. The main reason for these phenomena is the stress mismatch caused by the gradient distribution of lithium concentration during the fast filling process. High magnification results in severe uneven distribution of current density between the plates, and delamination between the plates is possible without external pressure. The effect of mechanical degradation on battery performance can be divided into active material loss (LAM), active lithium loss (LLI) and impedance increase.
4.Design of multi-scale fast charging performance
The aging and aging mode induced by quick charge are affected by many factors, such as the composition of battery materials (intrinsic characteristics of electrode materials and electrolyte), operating conditions (high rate charge and discharge, extreme voltage and temperature), battery production process and Pack design. Multi-scale design and composite means will contribute to the development of high-performance fast charging lithium ion battery.
1) It is always a challenging problem in battery design to select the right electrolyte and electrode material to give full play to high specific capacity and high rate performance. At present, many researches have been devoted to the development of dendrite-free fast charge anode materials, such as carbon matrix materials, metal oxide composites and alloys, which have achieved a certain degree of success. The conventional graphite anode potential is very close to the REDOX potential of lithium, which can make the battery exhibit higher energy density, but at the same time increase the possibility of lithium separation. Therefore, improving the anode material becomes one of the important ways to improve the performance of lithium ion battery. In addition, LTO is expected to be used to develop ultra-fast fast charging lithium ion battery with long life because it does not generate lithium and does not form SEI films. On the other hand, the high potential of LTO, as a negative material, will reduce the voltage of the whole battery, limit the energy density of the battery. Some metal oxides and alloys also have good energy and power characteristics, but their cyclic stability is usually poor due to severe volume changes, powders and agglomerations.
Other graphene-like two-dimensional materials have high surface area/mass ratio and unique physical and chemical properties that shorten ion transport paths, accelerate electron transport and increase the active sites of lithium ions, and are considered as potential anode materials. These materials mainly include transition metal oxides, transition metal sulfides, metal carbides and nitrides. Lithium metal is one of the cathode materials which can improve the energy density of battery most, but its power performance is poor due to the low specific surface area of pure lithium metal foil.
The selection and modification of materials will undoubtedly be the focus of future research. Many of the new materials exhibit faster charging performance than current commercial materials. However, these materials are in the early stages of development, and large-scale commercialization is still a long way off. In many cases, problems such as developing new production processes and equipment and reducing costs may also hinder the application of new materials. In addition, many new materials and structural designs are evaluated only at the laboratory level and may be compromised when applied to a commercial battery or Pack. Materials science will undoubtedly play an important role in the development of future batteries, but it will take a lot of engineering effort to truly solve the problem of fast charging lithium ion battery.
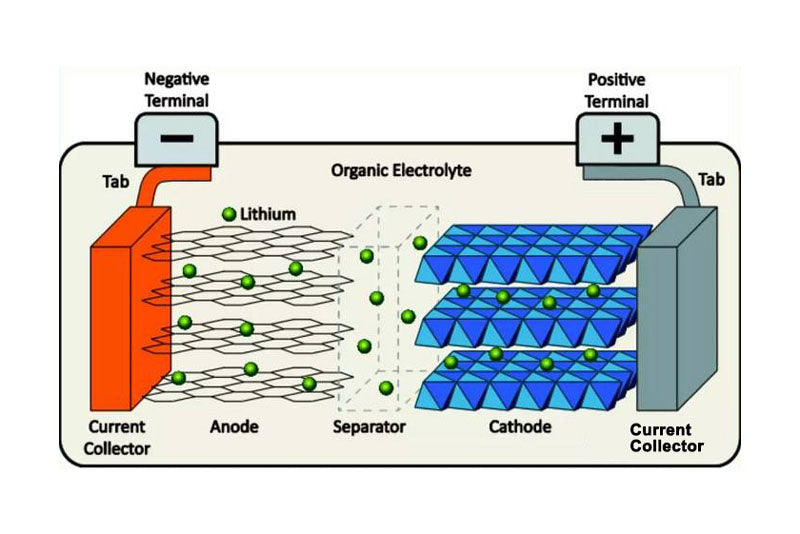
2) Cell and Battery Pack Design In addition to material selection and microstructure design, geometric parameters of electrode design also have an important impact on fast charging lithium ion battery performance. Increasing porosity and anode thickness can inhibit Lithium plating, but reduce energy density.
The geometric parameters of the fast charging lithium ion battery are also important factors affecting the fast charging capacity. The shape of the battery affects the distribution of current density and temperature, and larger batteries are more likely to cause uneven distribution of temperature and current. The location, material, structure and welding process of the electrode lugs are important for uniform distribution of current density, limiting local heat generation and delaying aging.
In addition, the relationship between Pack performance and cell performance is not well defined. Although there are many fast charging models of cells, few studies have attempted to extend this to Pack design, because Pack design needs to consider more parameters. At present, there are still many problems in the design of fast charging lithium ion battery Pack: 1) Fast-charging Pack requires high performance and low inconsistency between cells; 2) Advanced BMS requiring more sensors and circuit control for battery monitoring and balancing; 3) Advanced thermal management system shall be designed to maintain safe temperature and reduce temperature difference between battery and Pack.
5.Strategy for fast charging lithium ion battery
Although many solutions at the material level have shown good results, commercialization will be difficult in the near future. The researchers moved the quick charge solution to the battery and Pack levels to be available in the short term. The design of charging strategy is the key to solve this problem.
1) Types of charging strategies
Standard charge
CCCV is the most common charging protocol at present, that is, constant current charging to cutoff voltage (CC stage), and then constant voltage charging to small current close to 0 (CV stage). Constant pressure process can make the ion concentration distribution in the electrode material more uniform, which is very important for the material to play a high specific capacity. However, the current at constant voltage gradually decreases, so that the charging time of CV is significantly longer than that of CC. The simple operability of cc-CV charging mode makes it the most widely used standard charging protocol. But many other focused strategies can reduce charging time, improve charging efficiency, and improve capacity/power retention. The following figure shows several common fast charging strategy curves.

FIG. 9 Common fast charging strategy curve a) Constant current-constant pressure (CC-CV); B) Constant power-constant voltage (CP-CV); C) Multi-stage constant current-constant voltage (MCC-CV); D) Pulse charging; E) Boostcharging in CC-CV-CC-CV mode; F) Variable current charging (VCP)
Multi-stage constant current charging
Many studies suggest that adjusting the current in the charging process can slow battery aging and reduce charging time. These studies are often aimed at reducing heat generation, avoiding lithium extraction, or reducing mechanical stress. MCC is one of the earliest strategies for fast charging battery. It consists of two or more constant current stages followed by a constant pressure stage. Since the negative electrode potential at the beginning of charging does not easily fall to the lithium evolution potential, the current in the early CC stage is large. But some researchers have taken the opposite approach, charging with increasing current in the CC region, because the internal resistance of the battery gradually decreases.
Pulse charging
In the pulse charging process, the current changes periodically to reduce concentration polarization, avoid local potential negative or reduce mechanical stress increase caused by local lithium ion deembedding.
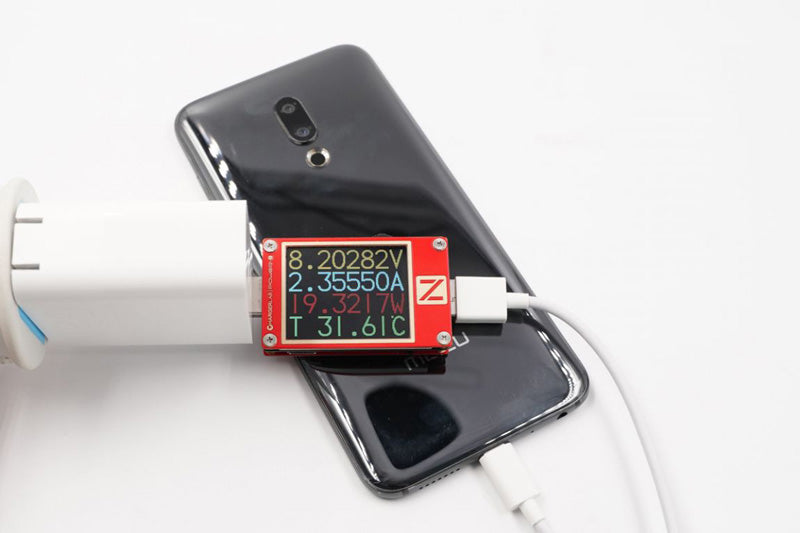
Enhance the charge
A large average current is used in the initial charging stage, followed by a reduction of current for CC-CV charging. The first charging stage can be the CC stage (the entire charging strategy is equivalent to McC-cv), the CV stage after the battery voltage reaches the maximum set voltage (CV-CC-CV), or a complete CC-CV stage (CC-CV-CC-CV). Compared to CC-CV, this strategy sets higher current and voltage to reduce the total charge time. However, under the same charging time, the capacity attenuation of enhanced charging is faster than that of CC-CV, while pulse charging has no significant difference with CC-CV. Some researchers have suggested that CC-CV is suitable for fast charging lithium ion battery with high-power, while MCC is often used for charging scenarios where lithium is easily flating.
Variable current charging
In order to achieve the purpose of fast charging, researchers proposed a series of more complex variable current charging curves, including VCD, UVP, etc. As the battery ages, the current curve needs to be adjusted according to the change of internal resistance at the same voltage. In addition to the aging factor, the current is always low during the initial charging phase and then increases rapidly, due to the maximum internal resistance of the 0%SOC battery, which decreases rapidly thereafter. The maximum current usually occurs in the lower SOC region, and then decreases gradually due to the increase of lithium embedding amount of particles and the limitation of Li transmission. In addition, temperature distribution within the battery and Pack during charging is important, but charging control strategies often only consider surface temperature as the main factor for attenuation.
Schindler combined different charging strategies in FIG. 9 to conduct cycle experiments on the battery and compared with CC-CV to study the capacity attenuation of the battery under different cycles. The results showed that the battery maintained 80% capacity after 800 cycles with all charging strategies, and performed best in all cycles. Only the CC-CV cycle decayed to the same capacity only 400 times; The cc-CV combined with cold derating cycle performed the worst with 330 cycles.
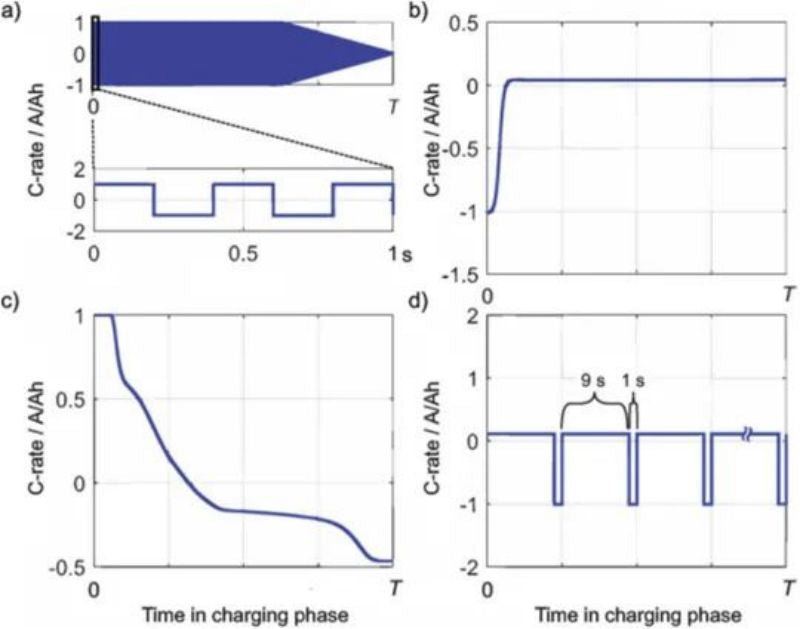
FIG. 10 Current curve: a) AC pulse; B) cold derating; C) Polarization retention; D) Pulse charging
Most fast-charge strategies work only at standard temperatures and specific battery configurations. Caution should be taken when fast charging for different types of batteries, as high current can cause greater mechanical stress within the electrode particles, accompanied by significant current and temperature heterogeneity. The universality of many current charging strategies lacks further experimental verification. With the popularization of electric vehicle in low temperature area, more research on strategy for fast charging lithium ion battery at low temperature is needed. In addition, it is the temperature itself, not the ambient temperature, that determines battery performance, and changes in battery temperature during charging also need to be considered. Finally, the effects of different charging strategies at Pack level need to be studied.
2) Strategy optimization based on model
Fast charging strategy based on ECM model
Some researchers optimize charging strategies based on equivalent circuit models. They embed these models into single-objective or multi-objective optimization constraints by using formulas. The thermal-electric-aging coupling model based on the equivalent circuit model can describe the thermal effect or battery aging caused by charging, and can optimize the battery heating and aging based on the model. Once the framework of optimization problem is established, an appropriate algorithm can be developed for fast charging control according to the cost function and constraints.
The equivalent circuit can describe the external characteristics of the battery, but cannot provide the information of its internal state, especially the side reactions in the charging process, such as SEI film thickening and lithium deposition. Therefore, electrochemical models have attracted much attention.
Fast charging strategy based on electrochemical model
Electrochemical models can estimate the internal state of the battery (solid/liquid potential, ion concentration, reaction flow, etc.) to predict side reactions during charging. The most commonly used electrochemical model is the P2D model proposed by Doyle, Fuller, and Newman. However, in the full order model (FOM), the calculation of partial differential equation (PDE) is very large. Therefore, the researchers performed a lot of simplification based on FOM to improve the computational speed. Some models also incorporate side effects to more realistically simulate what happens inside a battery.
In summary, model-based optimization charging optimization usually preferentially uses ECM, SP, ROM, etc., rather than FOM. Although there are many optimization methods based on model at present, few model results are completely consistent with experimental data, and these results are only applicable to new battery scenarios, so it is urgent to solve the problem of establishing a long-term aging model for batteries.
6.Impact of thermal management
Fast charging lithium ion battery is often accompanied by a large amount of heat generation and uneven heat generation. High rate charging at low temperature will do great damage to battery life and safety. Therefore, effective thermal management is very important to achieve lossless fast charging under all conditions. The design of a battery thermal management system varies greatly at different temperatures. High thermal conductivity is needed to cool the Pack, while better thermal insulation is needed to keep the Pack warm at low temperatures. Adjusting thermal conductivity according to temperature is one way to solve this problem.
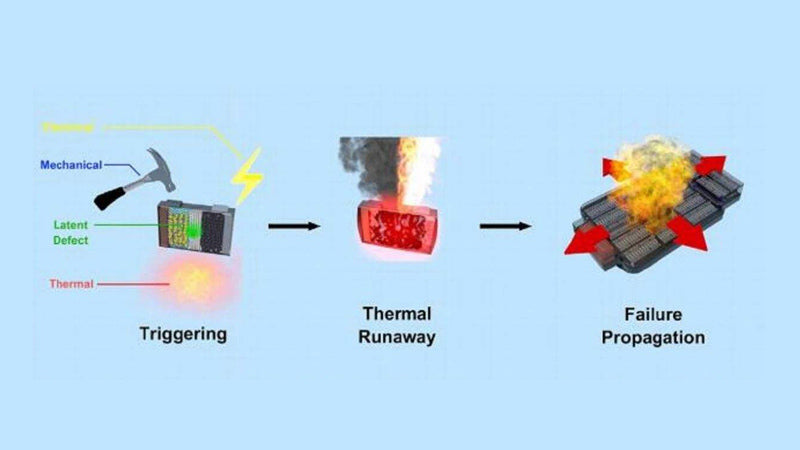
1) cooling
Common cooling media for Pack electric vehicles are air, liquid, and phase change materials (PCM). Air cooling system cost is low and simple, but because of its low heat capacity and poor thermal conductivity, air cooling rate and temperature consistency are poor, it is not suitable for fast charging system. Liquid cooling is 3,500 times more efficient than air, but it is costly, complex and leaky. To avoid short circuits, the cooling medium must be an insulator, and common liquids include deionized water and mineral oil. PCM cooling absorbs the heat produced by the battery through the phase transformation process of the material, but its disadvantages are also obvious: when the room temperature is very high, the PCM will completely melt even if the battery does not produce heat, and the liquid PCM with low thermal conductivity will hinder the heat dissipation of the battery.
Efficient and uniform cooling techniques are more important than standard charging because fast charging inevitably further aggravates temperature distribution inhomogeneity. The poor thermal conductivity of the inside of the fast charging lithium ion battery relative to the surface, which is usually connected to the cooling system, exacerbates the uneven distribution of temperature inside and outside the cell. Similar problems occur in the cell module and Pack.
Finally, some ev charging piles will be equipped with corresponding external cooling system according to charging conditions while improving the fast charging rate. If realized, this approach would reduce the cost of onboard cooling systems.
2) Preheating in low temperature environment
It is very difficult to fast charging lithium ion battery at low temperature. This section only describes how to heat the entire battery quickly, because rapid heating is essential for fast charging. Internal heating is favored for its high efficiency and high uniformity. The four common methods are: 1) self-discharge heating. This method is inefficient; 2) The electric heating wire is driven by the battery and heated with the fan. The heating speed of this method is relatively fast but the efficiency is not high enough and the heating is uneven; 3) Bidirectional pulse heating. A battery Pack is divided into two groups of batteries of equal capacity, and the electric power is pulse exchanged between the two groups, and the internal resistance is used for heating. This method has high efficiency, mainly limited by DC/DC conversion. Simulation results show that this method can heat 2.2Ah 18650 battery from -20℃ to 20℃ in 120s. 4) alternating current heating. This method of heating is faster, but its effect on battery aging and cycle stability is unclear. The design of fast charging lithium ion battery configuration to achieve rapid preheating is also one of the ways to solve the problem of low temperature fast charging.
Although the internal heating method is more efficient and makes the temperature distribution more uniform, there are few studies on the effect of the coupling of internal heating and fast charging on the cycle life of the fast charging lithium ion battery. Because the current is more likely to pass through the low resistance region, the corresponding region temperature will increase, so even a small temperature gradient caused by preheating will be amplified during fast charge. Because the internal temperature is difficult to measure experimentally, cyclic testing or a reliable model is needed to evaluate the preheating method. Nickel foil pre-heating, while promising, requires a non-standard battery design and can add weight, among other problems.
7.Safety
1) Influence of fast charging on thermal runaway
The study shows that the thermal runaway behavior of the battery will change after fast charging. Thermal runaway is caused by a chain reaction. Thermal runaway in a new cell is usually caused by a short circuit, followed by a reaction of the electrolyte and a maximum cell temperature. The process of thermal runaway of the battery after fast charging can be divided into three stages, as shown in FIG. 10. In the first stage (60℃ < T< 110℃), the precipitated lithium reacts with the electrolyte to heat the battery, and the SEI film continuously breaks and regenerates. At this stage, the temperature is relatively low. In the second stage (thermal uncontrolled induction stage), the lithium metal is consumed in the reaction with the electrolyte, resulting in a sharp rise in temperature. Diaphragm contracts, positive and negative contact. The third stage (thermal runaway to maximum temperature), due to a sudden rise in temperature, the positive and negative electrodes and the electrolyte and the reaction between the positive and negative electrodes. Finally, the fast charging lithium ion battery temperature reaches the maximum and thermal runaway occurs.
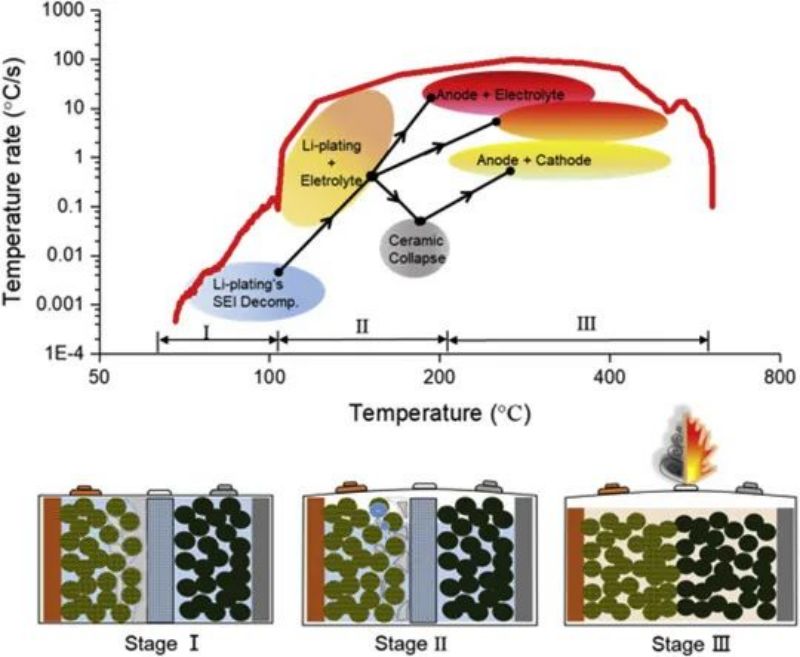
FIG. 11 Chain reaction of thermal runaway process of battery after fast charging
2) Thermal runaway caused by overcharging
Some fast charging lithium ion battery may overcharge due to inconsistencies between cells, which may lead to thermal runaway. This process can be divided into four stages:
Stage 1(100% < SOC < 120%) : the voltage exceeds the charging cut-off voltage and begins to increase slowly. At this time, the excess anode material can still insert lithium normally to ensure safety. Some side effects of the battery material may be induced, with a slight increase in battery resistance and temperature.
Stage 2(120% < SOC < 140%) : Transition metal ions such as Mn2+ in the positive electrode begin to dissolve due to excessive delithium. At the same time, because the voltage exceeds the electrochemical window of the electrolyte, the electrolyte also begins to oxidize. The negative electrode cannot receive more lithium ions and becomes unstable and produces lithium evolution. Lithium metal reacts with electrolyte to form a new SEI film, which increases battery internal resistance. The joule heat generated by overcharging can significantly increase the temperature of the battery.
Stage 3(140% < SOC < 160%) : The exothermic reaction of the battery material quickly catches up with and exceeds the joule heat generation of the current and becomes the dominant mode of heat generation. Electrolytic liquid oxygenation produces a large amount of heat and gas, resulting in battery pack expansion. With the increase of the amount of lithium evolution, the side reaction with electrolyte becomes more severe. When SOC approaches 160%, Mn2+ dissolves in the positive electrode. The positive electrode structure begins to change, and the fast charging lithium ion battery voltage reaches its maximum and begins to decrease gradually.
Stage 4 (140% < SOC < 160%) : The electrolyte decomposes and produces a large amount of gas, resulting in a sudden rupture of the battery pack. The diaphragm breaks, and a large area of internal short circuit occurs inside the battery, resulting in thermal runaway of the battery.
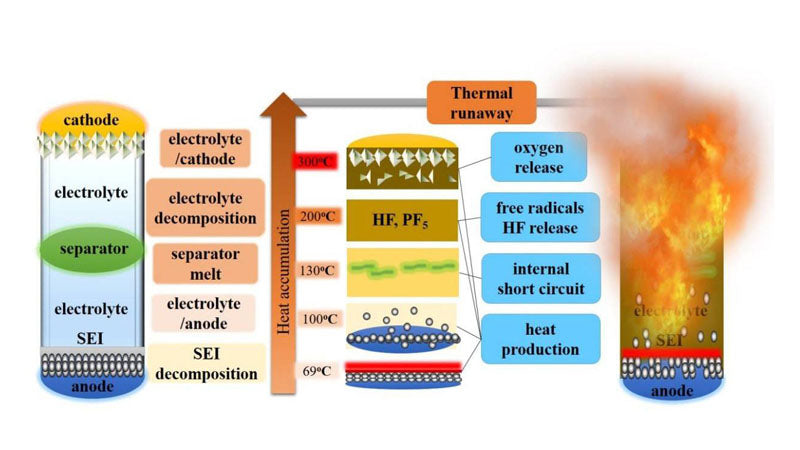
Based on the internal materials and reaction dynamics of the battery, two design methods have been proposed to protect the fast charging lithium ion battery from overcharging:
1) Increase the oxidation potential of the electrolyte from 4.4V to 4.7V, which can make the electrolyte more stable and increase the SOC of thermal runaway to 183%. This can be achieved by adding functional additives or additives that can undergo reversible REDOX reactions to the electrolyte.
2) The thermal runaway temperature of the battery is raised to 300℃ to delay the occurrence of short-circuit in a large area, and the SOC of thermal runaway is increased to 180%. Battery pack rupture can be delayed by optimizing the pressure design of the battery or by using a diaphragm with high heat exchange stability.
8.Conclusion on fast charging lithium ion battery
Electrification of transport is undoubtedly one of the most important ways to tackle climate change. In order to cope with range anxiety and meet customer needs, many manufacturers regard Pack's ability to recharge quickly as an important indicator. Although there have been many studies on fast charging lithium ion battery over the years, there are still many problems:
- To date, there is still no reliable on-board method to detect battery aging (such as lithium extraction and mechanical fracture). The lithium extraction detection method based on voltage platform is expected to be applied online, but it cannot effectively distinguish lithium extraction platform from other phenomena, and detect lithium extraction platform without voltage.
- Many new electrode materials have good fast charging capacity, but their stability, attenuation mechanism, large-scale production and cost remain to be discussed. Although graphite anode is very easy to remove lithium, graphite will dominate the market for lithium ion battery anode materials in the foreseeable future, considering the cost, wide application and maturity of the technology.
- Existing model methods have obvious limitations: ecM-based models cannot predict the internal state of batteries and can only be used in a limited range. On the other hand, the high-precision FOM model cannot be applied in real time due to the large amount of calculation. Therefore, a reduced order model is needed to accurately describe the inner core state of the battery, which can be applied in the future fast charging lithium ion battery BMS system.
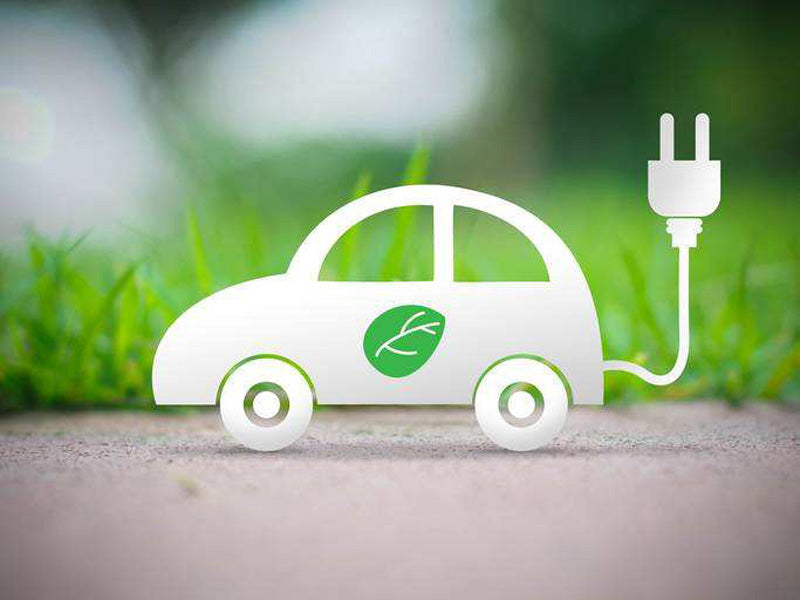
- Many fast charge strategies are developed based on experience or experiments, and their results are only applicable to specific battery configurations or specific operating conditions, and cannot be extended to other types of batteries. In addition, many model-based charging optimization studies are based on SP or ECM models, and the prediction accuracy of large current models is often insufficient.
- In order to further optimize the charging process of individual batteries in the battery pack and avoid local aging or overcharging, an advanced BMS system with balanced fast charging lithium ion battery consistency needs to be developed.
- Finally, the relationship between the decay rate of a cell and Pack is not clear. While many charging and preheating strategies work for individual cells, their effectiveness, feasibility, and cost for Pack applications are poorly studied. Effective charging strategies for some individual cells applied to the Pack can result in uneven distribution of temperature and current density, so any unconventional charging technique will require extensive research before practical application. In addition, few models take into account the effect of inconsistencies between cells within the battery pack. Due to the inconsistency of rapid charging amplification, multi-size research is urgently needed. Multi-dimensional studies are crucial for cell integration and Pack design.
Paper information:
Gregory Offer from Imperial College London, Ouyang Minggao from Tsinghua University and Billy Wu from the Faraday Institute, in collaboration with researchers from Shell Oil, are writing in the International Journal of Electrification of Transport ETransportation published A review of lithium-ion battery Fast Charging: A review. In this paper, the factors affecting the fast charging of lithium ion batteries, the existing main problems and solutions are reviewed from the material level to the system level.(eTransportation, Volume 6, November 2020, Pages 100088)