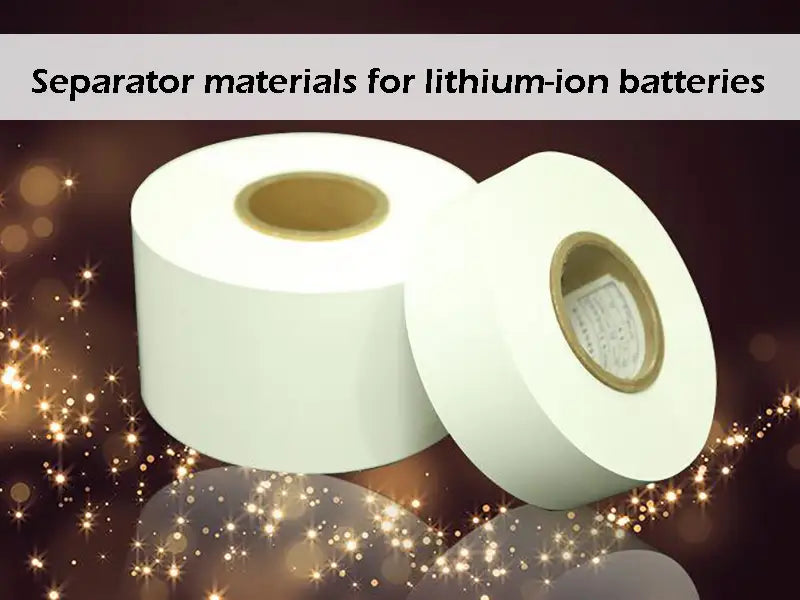
Main content:
The separator is a high value-added material with the highest technical barriers among lithium battery materials. After the gross profit margin of the separator usually reaches 70%, the value of the separator can reach 3 million yuan/t, and the appreciation rate is as high as several hundred times.
With the advent of the 3G era of digital electronic devices and mobile communications, there is a huge demand for small lithium-ion secondary batteries worldwide; while power lithium-ion batteries are widely used in power tools, robots, electric vehicles/hybrid vehicles, aerospace, Important applications in many fields such as national defense and military industry, its development has risen to the height of national strategic needs. At present, China has become a major producer of lithium-ion batteries in the world. In 2005, it produced 900 million lithium-ion batteries of various types, and it exceeded 1 billion in 2008. It needs a lot of separator materials every year. As an important component affecting battery performance, the role of lithium-ion battery separator cannot be ignored. The separator is an important part of the liquid lithium-ion secondary battery. It plays a role in preventing the positive/negative short circuit in the battery, and at the same time providing an electrical channel for ion transport during the charging and discharging process. The performance of the separator determines the interface structure and internal resistance of the battery. It directly affects the capacity, cycle performance and safety performance of the battery. The separator with excellent performance plays an important role in improving the comprehensive performance of the battery.
At present, only a few countries in the world, such as Japan and the United States, have the production technology and corresponding large-scale industries of polymer separators for lithium-ion batteries. The products used as separators for power lithium-ion batteries mainly come from the PP/PE/PP three-component composite films produced by the dry method of CELGARD Company of the United States and UBE Company of Japan. The dry method is to melt the polyolefin resin, extrude and blow it into a crystalline polymer film. After crystallization heat treatment and annealing, a highly oriented multi-layer structure is obtained, which is further stretched at high temperature to peel off the crystal interface. The formation of a porous structure can increase the pore size of the separator. The porous structure is related to the crystallinity and orientation of the polymer. This method has disadvantages such as difficulty in controlling the pore size and porosity. The ratio of the separator to heat shrinkage is large, and the closed-circuit protection design is not ideal when used as a power battery separator. China does not have its own high-quality separator products, and it costs billions of RMB to import separators every year. . The high price of separators (20~60 yuan/m2) is the main problem to reduce the cost of lithium-ion batteries. It is foreseeable that in the next 20 years, there will be a great market demand for high-performance, low-cost lithium-ion power battery separators.
For more than ten years, in order to solve the problem of localization of lithium-ion battery separators, the state and local governments have made large investments in the research and development of PE and PP stretch films, but so far, there is no evidence that China has A certain company has truly mastered the process technology for producing high-quality PP/PE stretch film. Compared with foreign products, some stretch film samples produced in China still have obvious gaps in quality and overall craftsmanship.
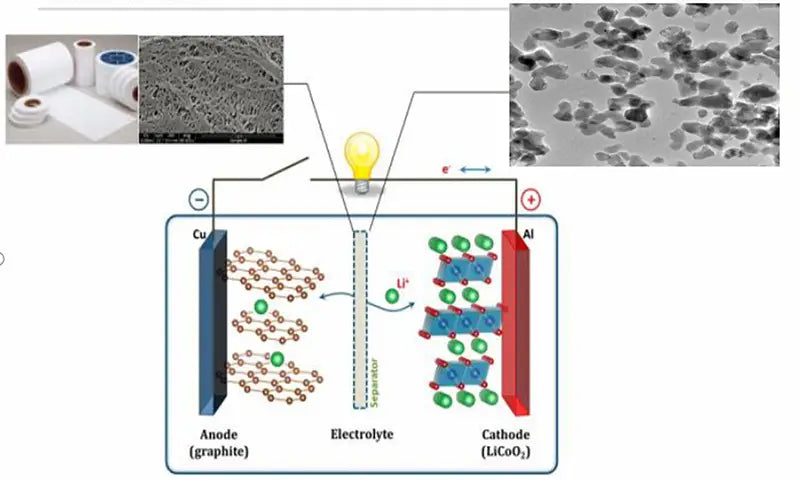
Lithium-ion battery separator paper is also called polyethylene film and PE film. Its role in lithium-ion batteries is to isolate the positive and negative materials. The quality of the separator paper directly affects the safety performance and capacity of the battery, so the selection of high-quality separator paper is the only way for battery manufacturers. There are usually two types of separator paper. One is to use PP, PE, PP three-layer composite separator paper. Currently, there are CELGARD in the United States and UBE in Japan. The characteristic of this type of separator paper is to reduce the cost, but the manufacturing process is complicated, and it is especially difficult to achieve ultra-thin below 16um. Second, single-layer PE separator. At present, there are three companies: Asahi Kasei of Japan, Tonen, and ENTEK of the United States. This type of separator paper is a single-layer PE, so the production cost is high, but it is particularly suitable for the manufacture of ultra-thin separators below 16um, so it is favored by large battery manufacturers, such as Sanyo Sony, Panasonic, Wansheng, etc. Almost all Japanese high-quality cells use single-layer PE separators.
1. The main characteristics of the polyolefin separator are as follows
1.1 Thickness of Polyolefin separator
The thickness of the lithium-ion battery separator is generally ≤25um. On the premise of ensuring a certain mechanical strength, the thinner the separator, the better. Now, most of the new high-energy batteries use a single-layer separator with a film thickness of 20um or 16um; the separator for batteries used in electric vehicles and hybrid electric vehicles is about 40um, which is the need for high current discharge and high capacity of the battery, but the thicker the separator, the more The better the mechanical strength, the less likely to be short-circuited during battery assembly.
1.2 Pore size and distribution of polyolefin separators
As a battery separator material, it has a microporous structure, which allows the absorption of battery electrolyte; in order to ensure consistent electrode/electrolyte interface properties and uniform current density in the battery, the distribution of micropores in the entire separator material should be uniform. The uniformity of the size and distribution of the pore size has a direct impact on the performance of the battery: if the pore size is too large, it is easy to make the positive and negative electrodes in direct contact or easily pierced by lithium dendrites and cause a short circuit; if the pore size is too small, the resistance will increase. The uneven distribution of micropores will cause excessive local current during operation, which will affect the performance of the battery. C.Venugopa et al. used a capillary flow pore meter and a non-volatile gas-containing organic liquid as a medium to measure the relationship between pressure and gas flow rate for different commercial lithium-ion battery separators. The results show that: the commercial membrane The pore size of the membrane is generally 0.03~0.05μm or 0.09~0.12μm, and it is considered that the difference between the maximum pore size and the average pore size distribution of most commercial membranes is less than 0.01um.
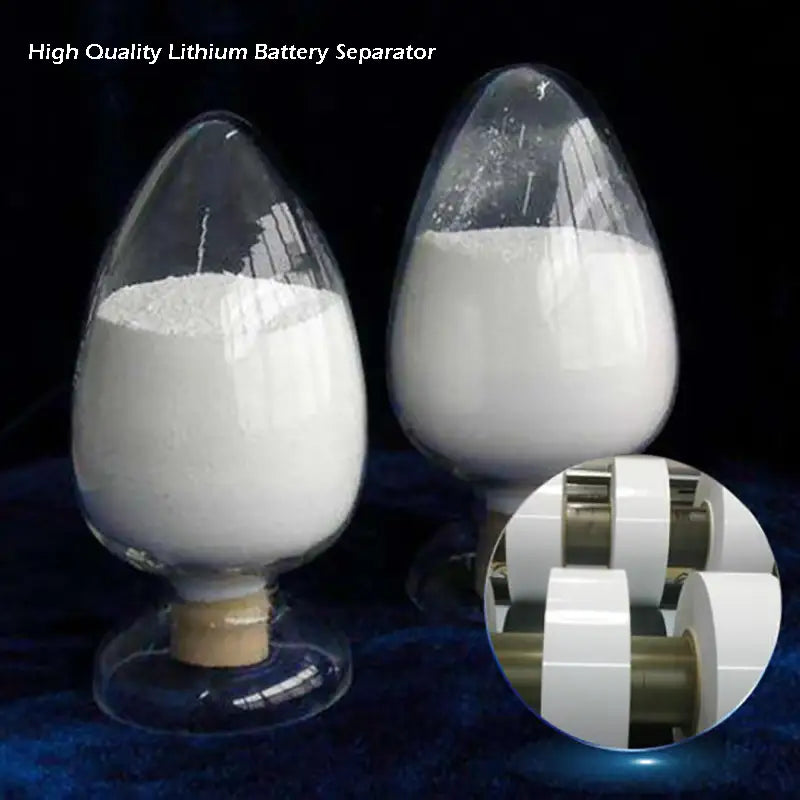
1.3 Porosity of polyolefin separators
Porosity is very important for membrane permeability and electrolyte holding capacity. It can be defined as: the ratio of the volume of pores to the volume occupied by the separator, that is, the volume percentage of pores in the volume of the unit membrane, which is related to the density of the raw resin and products. The porosity of most commercial lithium-ion battery separators is between 40% and 50%. In principle, for a given electrolyte, a separator with high porosity can reduce the impedance of the battery, but it is not the higher the better. Too high porosity will make the mechanical strength of the material worse.
1.4 Permeability of polyolefin membranes
The permeability can be characterized by the amount of gas passing through the separator under a certain time and pressure, which mainly reflects the smoothness of lithium ions permeating through the separator. The permeability of the separator is the result of the combined effects of the internal pore structure of the separator, such as the porosity, pore size, pore shape and pore tortuosity. Among them, the pore tortuosity has the greatest influence on the permeability, and the increase of the pore tortuosity will decrease the permeability in a square order.
In the structure of lithium batteries, the separator is one of the key inner layer components. The separator is made of plastic film, which can isolate the positive and negative electrodes of the battery to prevent short circuits; it can also block the current conduction in the battery by closing the cell function when the battery is overheated. The cost of lithium battery separator accounts for about 1/3 of the battery cost. At present, 60%~70% of the separator market mainly adopts the wet biaxial stretching process, because the wet biaxial stretching is more uniform in the longitudinal and transverse directions. The wet method is mainly used for high-end separators, and the dry method is used for low-end products.
The development of battery separators is mainly evolving with the changing needs of lithium-ion batteries. From a volume perspective, ion batteries are developing in two distinct directions, small and large. In some electronic products such as mobile phones and digital cameras, in order to meet the needs of beauty and portability, battery factories make the cells of batteries very small. In order to pursue high energy density and accommodate more electrode materials in a small volume, battery manufacturers hope that the thickness of the separator should be as thin as possible. Smaller volume is a challenge for the separator, because the separator must be made thin, but it must be able to maintain the original battery capacity, cycle performance and safety performance, etc., while having greater power and simpler design. On the contrary, in In terms of power batteries used in electric bicycles, electric vehicles and power tools, in order to obtain high capacity and high power, a battery usually needs to use dozens or even hundreds of cells for series connection. Due to the potential explosion hazard of lithium batteries, the safety of the separator is very important. Due to the increasing size, the technology requires higher efficiency, which can reduce greenhouse gas emissions and have higher power.
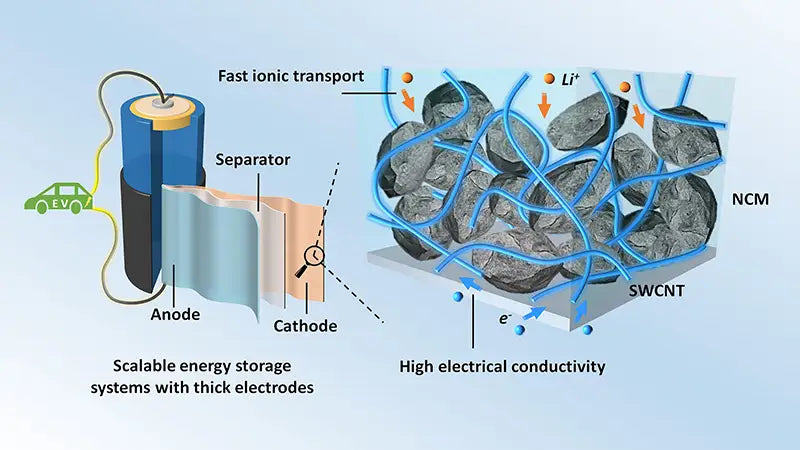
Lithium battery separators will develop targeted products according to the different needs of different customers, which is the development trend of separators in the future. Although the current separator market products are mainly single-layer, Exxon Mobil has been able to put different materials on different separator layers, each layer uses a different solvent and raw material formula, multi-layer hot melt co-extrusion to manufacture The thickness of the separator is similar to the diameter of the hair, so as to produce products with different properties. It is predicted that the development trend of the multi-layer separator is also obvious.
From a structural point of view, the liquid electrolyte in the lithium-ion battery may leak and pose a safety hazard. In order to eliminate the potential explosion hazard of liquid lithium-ion batteries, in recent years, all-solid-state gel polymer lithium-ion batteries have begun to appear in which the electrolyte and polyelectrolyte with ion transport properties are fully infiltrated to form gels. All-solid-state lithium-ion polymer batteries use gel polyelectrolyte, which requires the separator to have good liquid absorption properties. A method for preparing gel polymer separators was studied and reported. At the same time, there are also a lot of reports on the research of composite separators suitable for gel polymer lithium-ion batteries using polyolefin separator materials as the matrix and coated with PVDF, PE and other materials. All-solid-state gel polymer lithium-ion batteries have pointed out the main direction of lithium-ion battery development in the future. It will be the general trend for Chinese separator manufacturers to develop separators that can meet the use of all-solid-state lithium-ion polymer batteries.
2. ExxonMobil’s research on lithium-ion battery separators
Exxon Mobil Chemical produces innovative microporous membranes for HEVs and EVs on commercial lines The separator is designed to meet the safety, reliability and power performance requirements. This new type of separator adopts a proprietary wet biaxial stretching production process and is made by co-extrusion of a specially tailored high heat-resistant polymer, which improves the performance of the separator, ensures the uniformity of the quality of the separator, and is easier to use. Used in lithium-ion batteries for hybrid electric vehicles. The separator has improved breathability, higher fusing temperature and melt integrity, while maintaining shutdown temperature and mechanical strength. The unique comprehensive performance of the advanced microporous separator is the crystallization of the cooperation between Dongran Chemical and ExxonMobil Chemical. The separator will help produce lighter, smaller and more durable hybrid electric vehicle batteries, reducing system cost and increasing design flexibility.
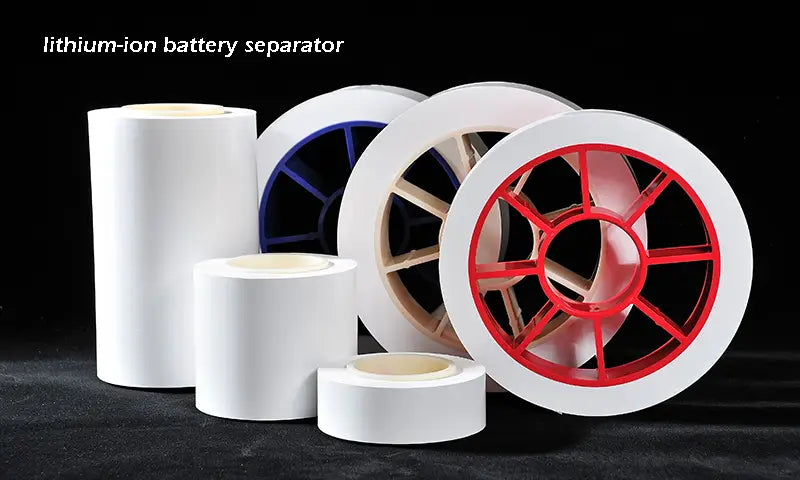
ExxonMobil Chemical announced at the end of January 2008 that it had developed a new battery separator membrane technology that will help electric vehicles hit the road and form part of Electrovaya's brand new electric vehicle. ExxonMobil battery separator membranes can greatly improve the power, safety and reliability of lithium-ion batteries, helping to power a new generation of low-emission vehicles with smaller and lighter batteries. Electrovaya has launched its zero-emission, low-speed vehicle, the Maya-300, and ExxonMobil's membrane technology enables lithium-ion batteries to meet the needs of hybrid and electric vehicles, helping to make vehicles like the Maya-300 lighter and more efficient. The Maya-300 electric vehicle has a range of 120mi.
ExxonMobil Chemical announced in May 2009 the development of two new grades of V-Series co-extruded battery separators. The new products will help produce lithium-ion batteries that are safer than ever for use in hybrid and electric vehicles, power tools, and electronics such as laptop computers. These newly developed grades have higher thermal stability and lower shut-off temperatures, which increase the safety factor of the separator. The grade further enriches the company's battery separator product line, including the award-winning V-Series battery separator launched in 2007. Like the V-Series separators, these new grades are developed on an advanced co-extrusion technology platform and proprietary wet biaxially oriented production process. The grade prevents thermal runaway in the battery, while providing designers of lithium-ion batteries with greater flexibility in choosing electrode systems and battery design formats, as well as increasing the power and capacity density of the battery. Both newly developed grades have improved safety factors. One of the grades has improved thermal stability, and its transverse shrinkage has been improved to 8%, which is far better than the 35.5% level of the previous generation of separators; the other grade has significantly reduced the shutdown temperature, only 128 ℃, which is also better than The 134°C level of the standard V-series grades maintains longer insulation periods at higher fusing temperatures. The high performance of the new battery separator will enable battery manufacturers to develop smaller, higher-power batteries, including batteries for a new generation of lower-emission vehicles.
It is precisely because of the huge business opportunity of battery separators that global chemical giants have been involved in this field. ExxonMobil Chemical already produces battery separators at its Nasu plant in Japan, and is building a new production plant in Gumi, South Korea, to meet growing market demand. The new plant opened in 2010.
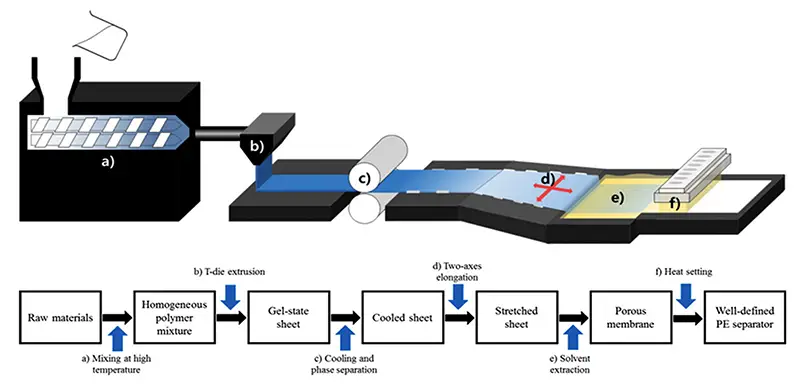
Nanofiber lithium-ion battery separator prepared by electrospinning method has a new material system and process method; corresponding experimental equipment and multi-nozzle preparation technology with production value have been developed; the preparation of mesh nanofiber membrane has been developed method, the porosity is controllable between 40% and 75%; the energy retention rate of the battery is as high as 74.4% at 14C discharge (under the same conditions, the energy retention rate of the battery assembled with the Japanese Ube separator is only 13.8%). After testing, the lithium-ion battery assembled with nanofiber separator has excellent cycle performance, thermal stability and high-rate discharge performance, which is obviously better than that of foreign separator products. The preparation process of nanofiber composite membrane is exquisite but not cumbersome, which is much simpler than that of stretched membrane; high porosity, high liquid absorption, low resistance, no direct relationship between thickness and porosity, good thermal stability, high rate discharge performance Prominence is its distinctive feature. Electrospinning is a powerful means to prepare nanofibers and various functional thin film materials. The biggest advantage of preparing lithium-ion battery separators is that the electrospinning process parameters can be easily adjusted, and the important characteristics such as porosity, fiber diameter, pore size, and thickness of the film can be effectively changed to meet the actual needs of the application. Incomparable with other methods. Taking the PP/PE film prepared by stretching method as an example, it is not easy to increase the porosity while keeping the film thickness unchanged. The separator is directly sprayed by electrospinning on the surface of the lithium-ion battery electrode sheet, and the assembly process of the separator and the electrode sheet is completed during the process of preparing the separator. This technology is undoubtedly an important innovation in the manufacturing process of lithium-ion batteries. Unparalleled features of craftsmanship. If the separator is directly sprayed on the surface of the electrode sheet, there will no longer be relative sliding and dislocation between the separator and the electrode sheet. The close contact can greatly reduce the internal resistance of the battery and suppress the shrinkage of the separator when the battery is heated, thereby improving the performance of the battery. Battery safety and overall performance. Now it is possible to design a reasonable spraying method according to the size of the electrode sheet, and spray the uniform separator material on its surface.