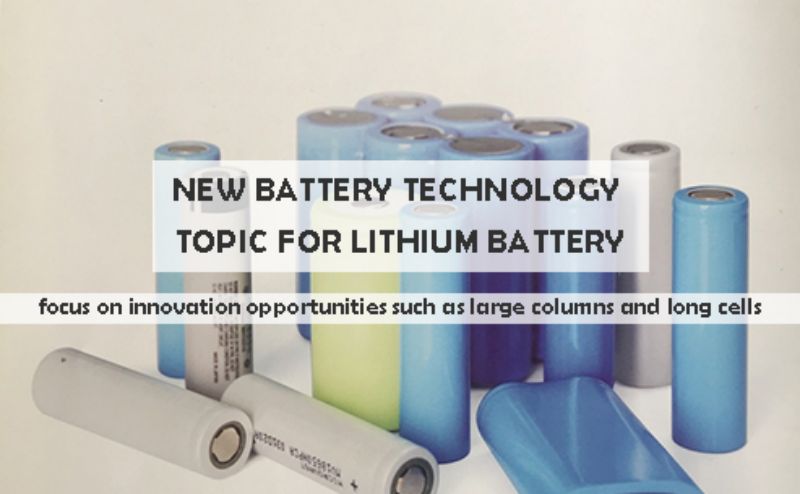
Main content:
With the popularization of new energy power, China vigorously promotes the development of new energy field, and lithium battery, as an important part of new energy, has ushered in a rapid development. Driven by the development of new battery technology, the new battery technology topic for lithium battery is constantly updated.
1. New battery technology development
① Battery performance trend
CATL, BYD and other core battery factories are all arranged in high energy ratio, super fast charging and battery safety technology directions, realizing paths including structural innovation, material innovation, etc.
With the development of new battery technology, leading battery factory CATL layout from six directions of high specific energy, super fast charging and true safety, realizing technology types including structural innovation, material innovation and management innovation, respectively, high specific energy, long life, super fast charging, true safety, self-temperature control and intelligent management. Take ultra-fast charging as an example. CATL ultra-fast charging refers to the fastest charging to 80% in 5 minutes. In terms of structure, multi-gradient pole plate and multi-pole ear mode are used.
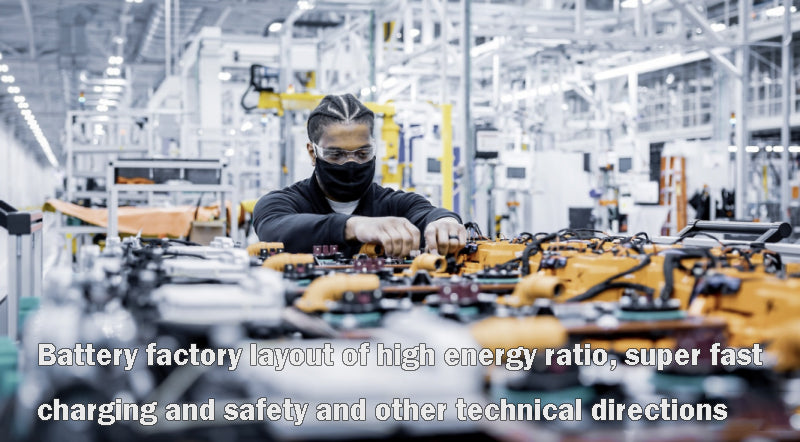
Specifically:
● Multi-gradient pole sheet: by regulating the gradient distribution of the porous pole sheet structure, realize the high porosity structure of the upper layer, the lower high pressure solid density structure, perfectly taking into account the high energy density and super fast charging double core;
● Multi-pole ear: Develop multi-dimensional space pole ear technology, greatly improve the current endurance of the pole plate, and break through the technical bottleneck of high cell temperature rise when 500A direct charging.
Driven by the development of new battery technology, BYD and other battery factories are also in the safety, fast charging, long endurance and other aspects of the battery layout. Take BYD blade battery as an example, "6S" technology concept to create blade battery super safety, super strength, super endurance, super low temperature, super life, super power super advantage; in addition, 96 cm long, 9 cm wide, 1.35 cm high single battery, through the array together, inserted into the battery pack like a "blade", skip the module and beam, reducing the redundant parts, forming the structure of honeycomb aluminum plate and so on.
Through a series of structural innovations, the blade battery realizes the super strength of the battery, while the safety performance of the battery pack is greatly improved, and the volume utilization rate is also increased by more than 50%. In terms of fast charging, the blade battery can charge power from 10% to 80% in 33 minutes.
② New-state battery / structural innovation
This article combs the battery form, mass production progress, performance indicators and advantage characteristics of the main battery factory, the main battery factory in the large cylinder, long cell and other new forms of battery actively layout;
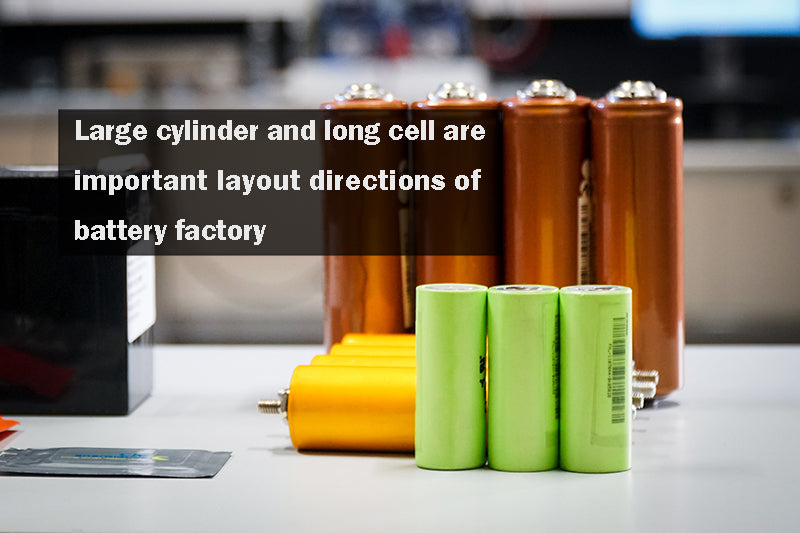
● Long cell: SVOLT, BYD and other battery factories for the long cell layout. Take SVOLT as an example, the second generation L600 of laminated long and thin cell layout has been developed; from the performance indicators, L600 monomer capacity increased to 196Ah, energy density over 185wh / kg, volume energy density over 430wh / L, with high compatibility, high adaptability, high safety and long life advantages.
● 4680 battery: TESLA, BAK, EVE and other battery factories on the large cylinder battery layout. Take TESLA as an example, 4680 battery uses high nickel cathode + silicon carbon anode material, anode ear technology, energy density of 300Wh / kg, battery capacity increased by 5 times over the current 2170 scheme, output power increased by 6 times, the electric vehicle range equipped with the battery can be increased by 16%, the battery cost per KWH can be reduced by 14%; In addition, it has advantages in energy density, power, charge and discharge efficiency.
2. 4680 battery: increased laser application and high equipment accuracy
① 4680 battery
In the context of the new battery technology, take TESLA 4680 battery as an example, technological innovations such as dry electrode and pless ear deserve attention. The Tesla 4680 battery is a cylindrical battery from the smaller 1865 to 2170 later, to further make a larger structural innovation. Compared with the previous 2170 battery, the 4680 battery significantly reduces the heat generation, solves the heat dissipation problem of high energy density cells, and improves the charge and discharge peak power. Finally, it makes the 4680 battery five times that of the 2170 battery, six times the power of the 2170 battery, and reduces the cost by 14% and increases the range by 16%.
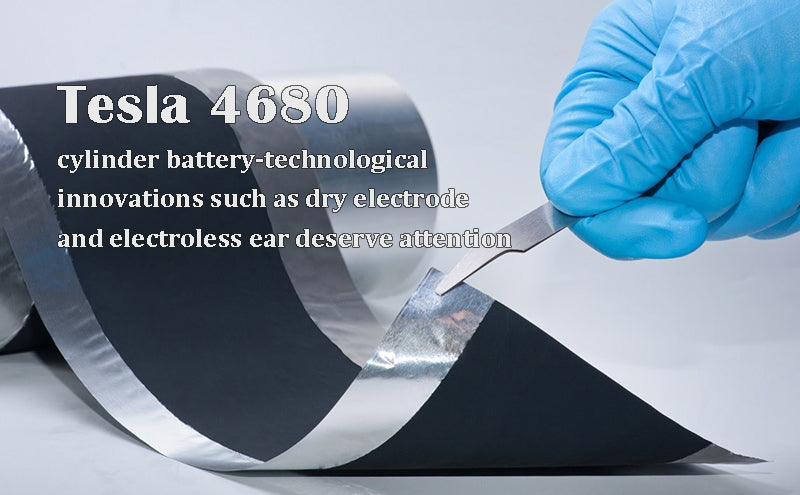
In the new battery technology, in terms of structural innovation and manufacturing process, compared with the previous battery, TESLA 4680 includes three main technical innovations: dry electrode process, no electrode ear (full pole ear), and CTC technology, which can reduce the production cost of battery cells and greatly improve the performance. Take the pole ear technology as an example, 4680 cell design turns the whole fluid into the pole ear, the conductive path no longer depends on the pole ear, the current from the pole ear to the collector to the fluid longitudinal transmission, so that the resistance drops to 2mΩ, and the internal resistance consumption drops from 2W to 0.2W.
② Dry-process electrode process
As a new battery technology, Maxwell dry-process electrode technology is suitable for the current lithium battery chemical system and advanced new electrode materials, compared with the traditional wet method cost is low, the core of the electrode formula and film extrusion equipment, no use in the manufacturing process of solvent, can be expanded to roll-to-roll production.
Maxwell dry-process electrode technology consists of three steps: dry powder mixing, from powder to thin coating molding, and thin coating with pooled fluid compression, all of which are solvent-free. The dry process electrode process of Maxwell is scalable, can adapt to the current lithium-ion battery chemical system and advanced new battery electrode materials;
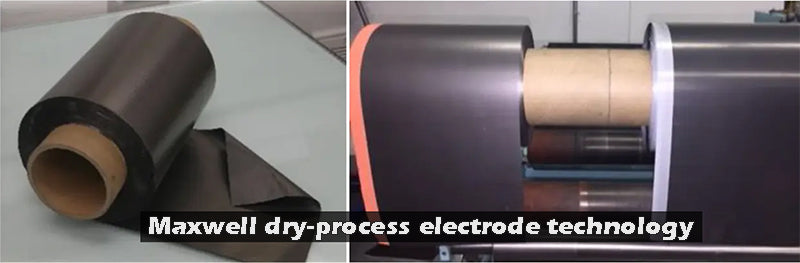
● In new battery technology, using the Maxwell proprietary dry process for powder mixing, to form the final powder mixture composed of active material, adhesive, and conductive additives, the powder mixture to form a continuous self-supporting dry coating electrode film, electrode film can be rolled to adjust the processing conditions of the thin coating electrode film, can control the material load and coating thickness, and prepare a variety of dry coating electrode structures. Finally, the thin electrode layer is combined with the fluid collector to form a battery electrode sheet.
● In terms of advantages, compared with conventional wet electrodes, the Maxwell dry electrode process can be used in classic and advanced battery materials in new battery technology, and can be extended to roll-to-roll production, while reducing manufacturing costs, eliminating solvent toxicity, and improving battery performance (dry coated electrodes output more power than wet coated electrodes).
● From the perspective of the core technology, the core technology of Maxwell's dry process electrode process is the electrode formula and the film-forming extrusion technology and equipment.
In addition, the dry process electrode can also be realized by pulsed laser and sputtering deposition. Compared with the wet process process and the Maxwell dry electrode process, it needs to increase the film annealing process. Different from the wet electrode preparation process, the dry electrode does not need the dry process, but the film annealing process should be increased due to the high temperature caused by the pulsed laser deposition.
The specific electrode preparation process is as follows:
Wet-process electrode preparation process; Slurry casting process: lithium battery electrode is cast with slurry (including active substance, conductive carbon and binder) through metal collector fluid. Solvent-based electrostatic spray deposition technology: the solvent-based electrostatic spray deposition technology is used to apply the electrode material on the fluid collector, that is, the deposited material is atomized at the nozzle and applied to the fluid collector. Lithium batteries are also produced using spraying technology.
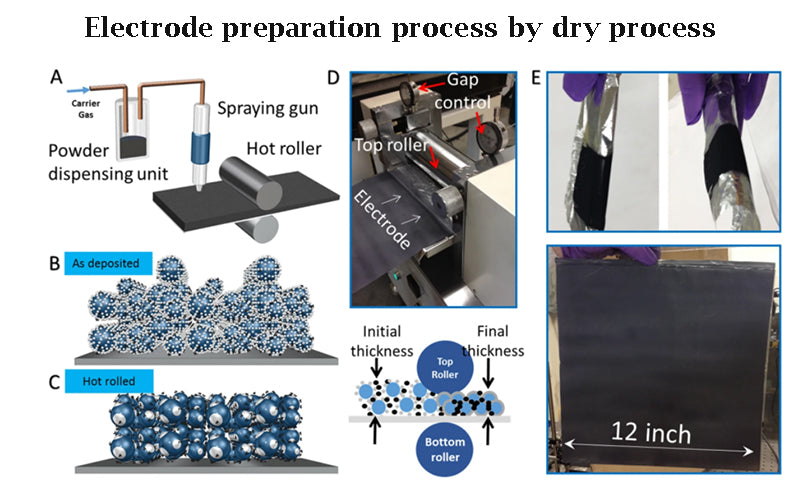
The dry process electrode preparation process is realized by pulsed laser and sputtering deposition. Pulsed laser deposition is achieved by focusing the laser onto the target body containing the material to be deposited, and once the laser hits it, the material vaporizes and deposits on the fluid collection; although not solvent is used, the deposited film must withstand a high temperature of 650-800℃, while the magnetron sputtering deposition can reduce the required annealing temperature to 350℃. This method is representative of dry cell electrode fabrication, but deposition is slower and requires high temperature annealing. As a new battery technology, compared with the traditional wet process, the cost of dry electrode process is low, which is mainly reflected in the labor cost, equipment input and plant area.
③ Electroless ear (full polar ear) technology
Electroless ear (full pole ear) technology can greatly reduce the battery resistance and internal resistance consumption.
● Traditional cylindrical battery: cathode and anode copper foil, aluminum foil diaphragm superimposed winding, in order to lead out the electrode, will be welded at both ends of the copper foil and aluminum foil respectively a guide wire (pole and ear).
● 4680 Battery: the whole fluid into the pole ear, the conductive path no longer depends on the pole ear, the current from the pole ear to the collector plate to the fluid longitudinal transmission, the entire conductive length from 1860 to 1000mm (battery height), so that the resistance is reduced to 2mΩ, internal resistance consumption from 2W to 0.2W, an order of magnitude.
Production angle: the process is divided into cutting first and then rolling first and rolling first and then cutting first, among which the latter requires a high precision of laser die-cutting.
Production process: there are two production processes for electroless ear, that is, cutting first before winding, winding first, and then laser die cutting;
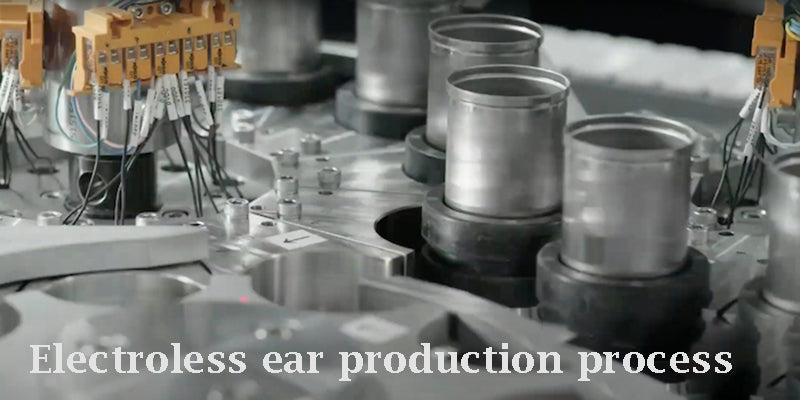
Cut first and then wound: through precision calculation, the material is cut into many parts before winding, winding when the position is cut can be easily aligned, when the winding reaches the preset energy after welding.
Winding first and then laser die cutting: the material regardless of the size directly winding, reach the preset energy after the excess material laser die cutting, the accuracy requirements are very high, if the gap between the two layers of materials is inconsistent, it may be cut to the material, resulting in inconsistent internal resistance.
Equipment requirements: from the perspective of production equipment, under the new battery technology, electroless ear (polar ear) mainly has major changes in three aspects;
Coating process: polar ear certain arc causes higher precision of the equipment requirements, the outer circle white than the inner circle will be more and more circle white;
Cutting equipment: the requirements of laser die cutting process are higher, the cutting edge is not uniform, resulting in the material layer seam gap; Laser welding: the number of solder points of full pole ear laser spot welding is more than five times higher compared with 21700.
3. Long cell: folding era
① Cell production trend: from the "rolling era" into the "folding era"
"Blade battery" adopts the lamination process, the non-traditional winding process, makes the core compaction density higher, thinner thickness, improve the energy density and safety. In the development trend of new battery technology, battery cells are developing towards the direction of large size and long battery cells. It is expected that the future automotive market will be the mainstream.
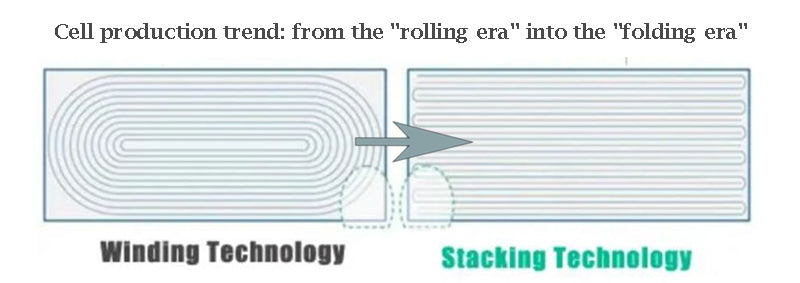
Take the BYD blade battery as an example, the lamination process improves the volume utilization rate of the cell when formed into a battery pack. The blade battery lamination adopts the equipment and cutting scheme completely independently developed by BYD. The BYD "blade battery" greatly improves the volume utilization rate through structural innovation, and finally achieves the design goal of installing more cells in the same space. Compared with the traditional module battery pack, the volume utilization rate of the "blade battery" has been increased by more than 50%, and the range has reached the same level of high-energy ternary lithium battery.
② Lamination machine
Compared with the winding process, under the development of new battery technology, the advantage of the lamination process is that it can effectively avoid the core defects such as powder drop and gap caused by the wafer and diaphragm bending, which meets the principle of lithium ion uniform motion, the core quality can be effectively improved and the overall energy density of the battery; but the winding process is slow in the production rate of the core.
The battery multiplier performance of the laminated structure is good. The laminated battery is cut into specific shapes and folded alternately through cathode and anode. There is a polar ear in each layer, which is better than the ordinary structure of winding process, polar ear structure and the structure of multipolar ear structure.
From different ways of lamination, the Z-type lamination technology is more common at present. Through the movable lamination platform, we pull the diaphragm back and forth between the lamination platform to realize the cross stacking of cathode and anode pole plates, but there are problems such as diaphragm deformation and difficult to improve the lamination efficiency. Compared with Z-type lamination technology, thermal composite lamination has the advantages of high chip diaphragm quality, improved chip chip quality and high equipment efficiency.
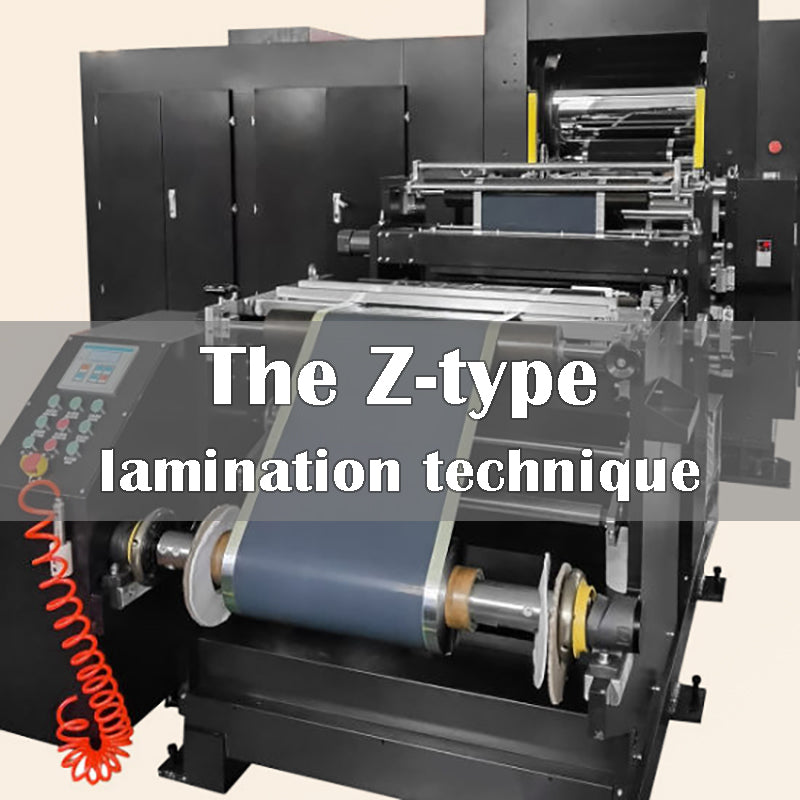
Relative to the traditional cathode and anode sheet single lamination cross stacking lamination, thermal composite lamination machine its biggest characteristic is to realize the cathode, anode and diaphragm disposable complete slice stacking, equal to the cathode and anode first once forming a small lamination unit, then by small lamination unit stacked into core, realize full sheet lamination, effectively improve the quality of lamination and core and production rate. Therefore, in the new battery technology, the thermal composite type lamination has the advantages of high pole core diaphragm quality, improved pole core pole wafer quality, high equipment efficiency, strong equipment expansion, and high degree of intelligence.
③ Technical reserve and application
Equipment factories actively layout lamination technology, cutting and stacking all-in-one trend; some equipment factories have batch orders and shipments. From the application of battery factory, taking BYD and SVOLT as an example, the application of lamination technology has gradually matured in the new battery technology, and the production efficiency has been improved rapidly, and in some cases, the efficiency is beyond the far winding mode.
BYD: In the production process of BYD blade battery, nearly 1 meter long pole sheet can realize the accuracy and speed of tolerance control within 0.3mm of ± and the efficiency of single chip lamination at 0.3s / pcs.
SVOLT: SVOLT innovatively takes the lead in applying the high-speed laminated process in the field of the square hard shell battery in the world, producing and launching the square laminated ternary battery, creating and leading the power battery industry into the folding era.
4. New battery technology integration scheme
① Technical trends
The CTP / CTC integration scheme makes the battery space utilization rate and the battery power higher, and the battery factory / oEMS actively layout, which has become the development direction of the new battery technology. Specifically, the CTC scheme can use the space in the floor to further increase the space utilization rate compared with the CTP scheme, and increase the battery power by about 5% to 10%. At the same time, because the integration mode is that the battery pack top cover independently replaces the battery body floor or uses the battery body floor as the battery top cover, the CTC battery integration scheme needs to carry the load.
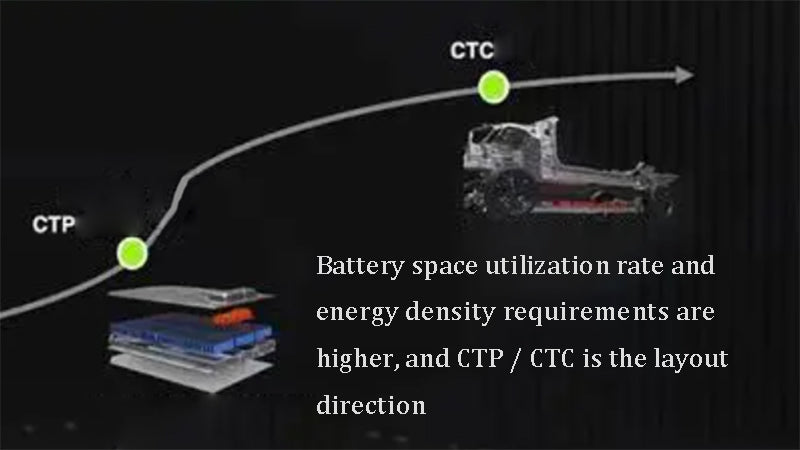
② CTP technology
In new battery technology, CTP technology has higher requirements for cell quality, and puts forward higher requirements for shock shock, air tightness and lightweight for the battery tray. Taking welding as an example, yield control and large-scale manufacturing requirements put forward higher requirements for CTP battery welding. The details of the CTP technology are as follows:
● The manufacturing process is simple and shorter cycle: by omit the module, reduce the use of parts, so as to optimize the space utilization rate, reduce the total weight of the battery pack, and achieve the effect of improving the battery energy density. The whole manufacturing process is simple and the production cycle is shorter.
● Cell yield requirements are higher: CTP batteries can be regarded as multiple small batteries to form a large battery, and all small batteries share the same package.
● Higher requirements for battery pallet and material: CTP technology is directly integrated into the battery pack, which puts forward higher requirements for shock shock, air tightness and lightweight battery pallet under new battery technology. In summary, both the yield control and the large-scale manufacturing have put forward higher requirements for CTP battery welding.
At present, CATL, BYD, SVOLT, CALB, Envision AESC and other battery factories are actively layout and applying CTP technology. Take CATL as an example, CATL's Kirin battery (third-generation CTP technology) has a number of technological innovations. In terms of performance, the system energy density of Kirin battery reaches 255Wh / kg, with 4C fast charging performance, and the thermal conductivity is improved by 50%, and the system integration efficiency is 72%; the original independent design of horizontal and longitudinal beam, water-cooled plate and heat insulation pad is cancelled, forming a multi-functional elastic interlayer to improve the system integration efficiency.
③ Chassis technology: innovative honeycomb mesh structure
Combined with the layout of TESLA and BYD in the chassis technology, both 4680 battery and long cell form are applicable to the CTC / CTB battery chassis honeycomb structure, to improve the overall stiffness of the battery pack.
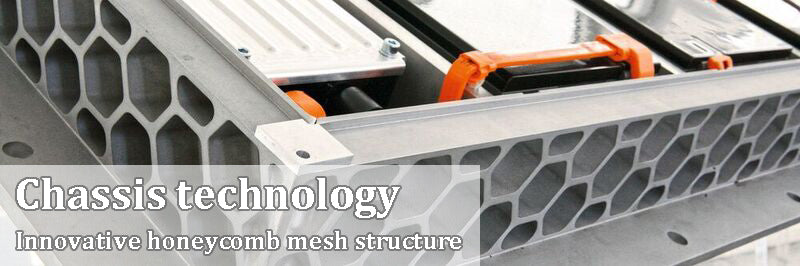
In addition, the innovative honeycomb mesh structure trial integrated casting process, has explosion-proof, impact-proof and other characteristics. Driven by new battery technology, other battery factories / oems also actively layout CTC / CTB and other chassis technologies, and some models of oems such as BYD and Zero Run are equipped with this technology and start pre-sale.
Related article: where to buy 18650 batteries, lithium battery vs other batteries