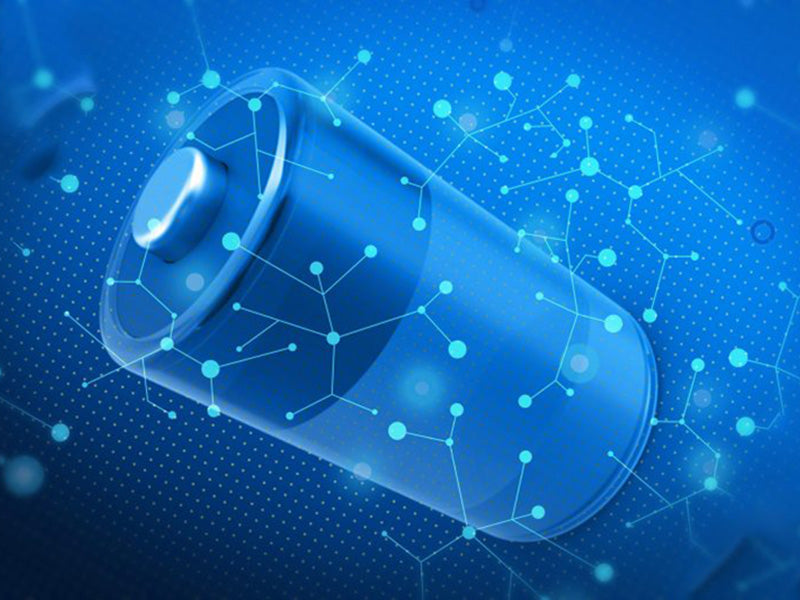
1. Development of battery technology
Since 1991, Japan has carried out three large-scale research projects in miniaturized industrial devices, sensors, controllers, etc., followed by the United States and the European Union in this field. The implementation of these projects has led to the emergence of new battery technology or the modification of conventional battery technology, especially in the field of microelectronic battery technology. This is what we usually call microtechnology and nanotechnology.
The energy supply has also gone through the same process, and micro power battery technology with thickness of no more than a few microns has also begun to appear, including non-rechargeable micro primary battery technology, and rechargeable micro battery technology.
Although this miniature power battery technology is still in the experimental stage, they have shown good development prospects in numerous application fields, including smart cards, micro-machines, electronic tickets, etc. But this type of battery technology is not to be confused with pocket or mini-battery technologies such as paper battery technology or polymer electrolyte battery technology, which are capable of delivering large currents but are tens of millimeters thick.
Electrochemical miniature power battery technology refers to power supply systems with a total thickness of no more than a few microns. It is made with special thin-layer technology, cathode atomization technology, thermal evaporation technology, etc., and is used to power micro-systems (microelectronics, micromechanics, etc.
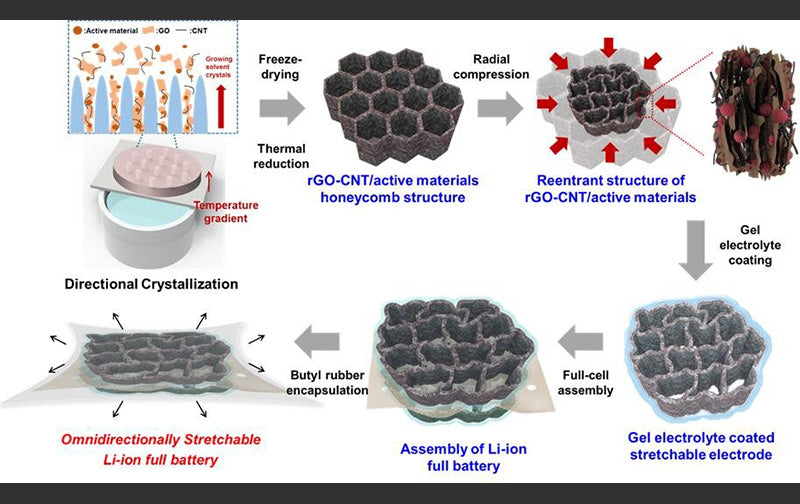
Micro power battery technology is made by thin-layer processing methods in microelectronics technology, which can provide more sufficient current for micro-systems. Such systems differ from other power systems made with thick-layer technology (each layer is tens of microns thick and is usually made by inkjet printing of fine powders). The thickness of each basic single cell in the micro power supply is about 10 μm, which can be superimposed and connected in series and parallel as needed. Therefore, it is foreseeable in the near future that such miniature power battery technology can be attached to a substrate in a rigid or flexible manner, the surface and thickness of which can be adjusted according to the available volume and performance requirements, and can finally be realized. Remote charging.
The materials used in miniature power battery technology are generally the same as those used in lithium battery technology. However, the structure of the thin layers makes micro power battery technology something special: the former may have a far different chemical composition than the latter, and the structure is looser. As a result, the electrochemical properties of micro-power battery technology are very different from those of large-scale battery technology. Thus, we can obtain new materials with desired properties from known large-scale battery materials using thin-layer techniques.
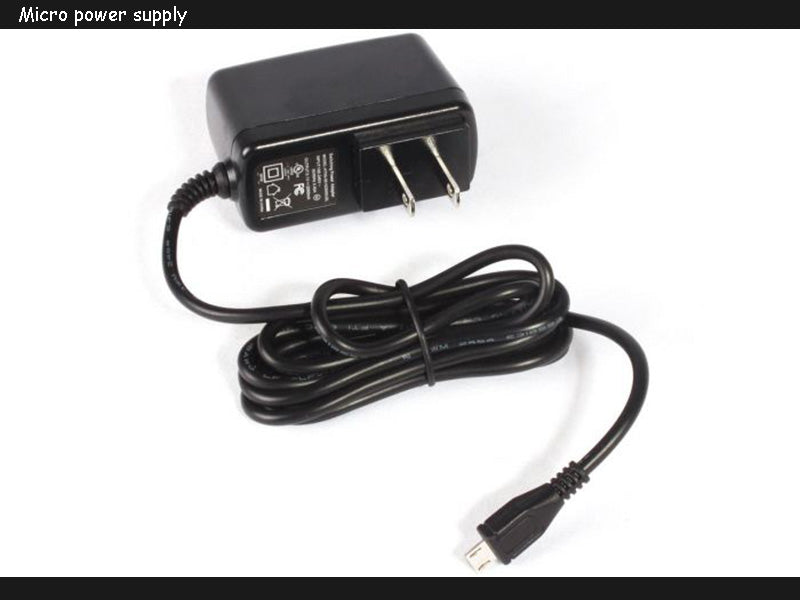
Due to the many advantages of metal lithium, it has become the main negative electrode material used in the current research on micro power battery technology. Lithium electrode materials have been performing well in conventional battery technology applications and appear to have no particular problems with thin layers. But lithium electrodes are not without their shortcomings, and some laboratories are also researching alternative materials for lithium. The disadvantages of using lithium electrodes are: First, the negative electrode is deposited by thermal evaporation technology, while the electrolyte and positive electrode are deposited by other methods, and a single deposition technology is also more appropriate. In addition, since lithium is very sensitive to humidity, it is necessary to carry out proper protection treatment without adding too much thickness. To compensate for these deficiencies, intercalation materials such as cathode materials can be used to replace lithium, but their potentials are required to be as low as possible. In this way, by inserting two electrodes, a micro power supply, also known as a rocking chair micro power supply, can be formed. Although the potential difference of this type of power supply is reduced compared to the miniature power supply with lithium electrodes, it does not matter much depending on the application. However, there have not been many attempts to utilize intercalation materials as anodes. The materials we can identify are Nb2O2 and Li4Fe0.5Ti4.5O11.75, which can be used in all-solid-state miniature power supplies. The use of graphite to replace lithium in large battery technology (lithium-ion batteries) does not seem to be applicable to micro power battery technology. Therefore, the search for non-graphite intercalation materials for anodes is a very unique problem in the development of micro-power battery technology, and there is still much work to be done in this area.
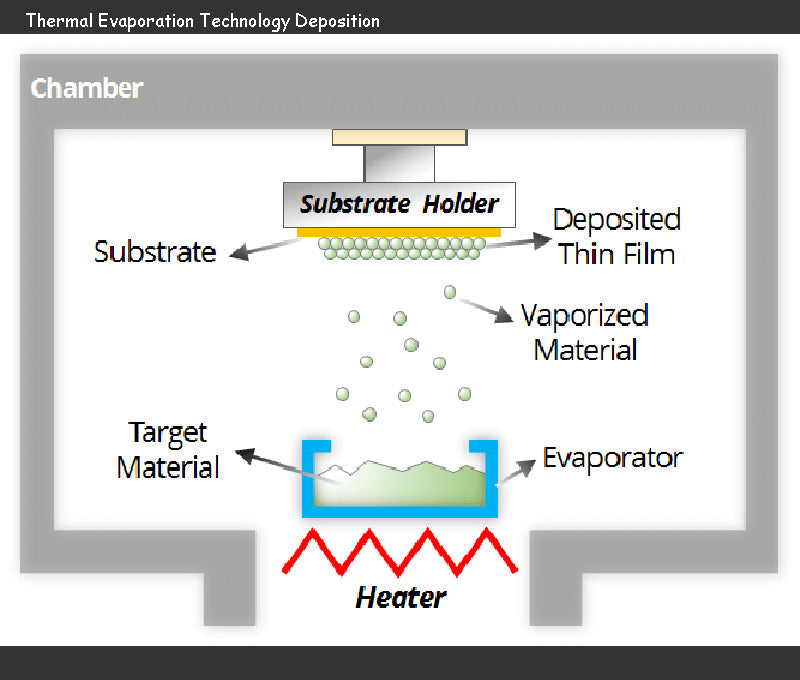
The ideal cathode material is both a good electronic conductor and a good ionic conductor, and the transition elements in it enable the reversible deintercalation of lithium ions. In order to make the energy density of the battery as high as possible, the potential corresponding to the redox reaction of transition elements must be as high as possible, and the molar mass must be as low as possible.
Titanium disulfide (TiS2) was the first cathode material used in lithium battery technology, and all-solid-state miniature power supplies made of this material appeared in the early 1980s. Such a TiS2/glass/Li battery system can be cycled 1000 times with a voltage range of 1.4~2.6V and a current density of 50μA·h/cm2
. By reversibly inserting 0.9 unit of lithium ions into the unit Ti, a corresponding capacity of 50μA·h/cm2 can be obtained, and it can not change with the charge-discharge cycle. The surface area of the system reaches 1~10cm2 and can be increased. The performance of this micro battery technology is sufficient for some applications and can therefore be developed industrially. However, micro-battery technology and micro-power battery technology are still in the research stage. Pioneers in the industry are developing prototypes and are actively preparing for industrialization.
Oxides of transition elements are theoretically more suitable for the preparation of cathode materials than their sulfides, and they are also widely used in lithium battery technology. Therefore, in the past few years, there have been numerous attempts to prepare them in the form of thin films and apply them in miniature power battery technology. Conventionally, these materials require thermal treatment after deposition, in order to make it easier for lithium to diffuse inside by increasing the crystallization of the thin layer. However, thermal processing can be a problem if the micro power supply is placed on the chip.
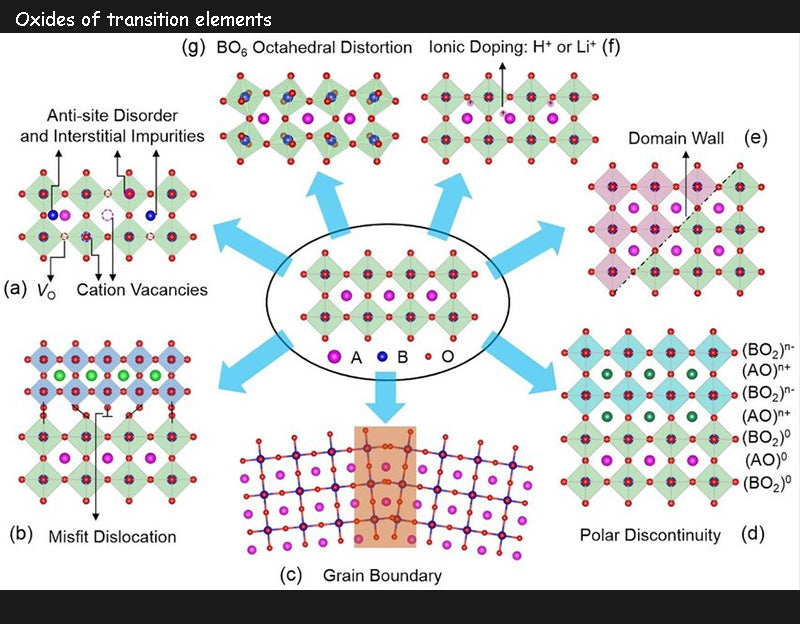
One of the most widely studied cathode materials is LiMn2O4, which is prepared by cathode pulverization technique or thermal evaporation technique. The current density of LiMnO4/Lipon/Li micro power supply is 10μA/cm2, the voltage is 3.8~4.5V, and it can be used for 300 cycles. Its constant capacity of 15 μA.h/cm2 remains almost unchanged; it only drops to 40% when the current density is 100 μA/cm2. Of course, the capacity density of 15 μA·h/cm2 is relatively low compared to TiS2, which is due to the small thickness of the LiMn2O4 thin layer. Other oxides have similar properties, such as LiNiO2、LiCoO2 and V2O5.
2. Battery Electrolyte Technology
The electrolyte must be stable with respect to lithium and have an electrochemically stable region of several volts. For thin-layer solid electrolytes with a thickness of about 1 μm, the ionic resistivity is sufficiently low, on the order of 1000Ω (10-7~10-4S/cm)
The main electrolyte is composed of inorganic materials, usually oxide glasses formed into thin films by cathodic atomization. For example, a vitrified film containing the composition (B2O3)0.38(Li2O)0.31(Li2SO4)0.31 has an ionic conductivity of 10-7S/cm at room temperature, which is sufficient to obtain 100μA/cm without excessive polarization. The current density in cm2. However, higher conductivity is necessary for micro power supplies to operate at higher currents or at lower temperatures. One way to achieve this is to deposit thin layers using active cathode atomization under partial pressure of ammonia. In this way, using the target material (P2O5)0.25(Li2O)0.75, the glass Li3PO2.5N0.3 called Lipon can be obtained through the above process, and its ionic conductivity at room temperature is 3×10-6S/cm. These glasses have an electrochemically stable region of about 5V and are very stable in contact with lithium.
Similarly, sulfur can be doped into oxide glass, a glass from P2O5-P2S5-Li2O-LiI system has an ionic conductivity of 5×10-5S/cm at room temperature. However, since this electrolyte readily reacts with lithium, a very fine layer of LiI
is required to isolate them, but also reduces the room temperature ionic conductivity of the glass/LiI mixture to 2 × 10-6 S/cm. The electrochemical stability domain of this mixture is about 3V.
The ionic conductivity of sulfide glass thin layers from the GeS2-Ga2S3-Li2S
system can reach 10-4S/cm
. However, these materials are hygroscopic like lithium, making their preparation more difficult.
3. Rocking Chair Micro Power Battery Technology
A typical representative of rocking-chair micropower battery technology is a microbattery, which consists of a lithium-doped compound Li4Fe0.5Ti4.5O11.75
as the negative electrode, an electrolyte containing a LiBO2 compound (a low-performance electrolyte), and a LiCoO2 compound as the positive electrode. To prevent the formation of the passivation layer, a thin layer of fine LiTaO2 was inserted between the electrolyte and the negative electrode. The battery system can perform charge-discharge cycles between 1 and 2.6V with a current density of about 100μA/cm2 and a capacity of about 35μ.A·h/cm2.
4. Battery manufacturing technology
Among battery technology, only chemical vapor deposition (CVD) or physical vapor deposition (PVD) can produce thin layers with better performance.
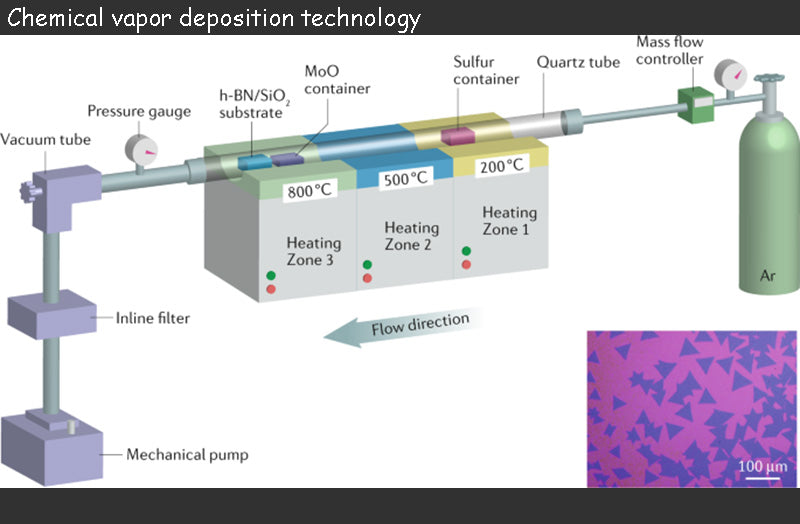
The thin layers produced by chemical vapor deposition techniques are usually crystallized and have good adhesion, and the deposition speed of this battery technology can be accelerated. Since the substrate needs to be heated to several hundred degrees Celsius, flexible thin layers of materials such as plastics, which are indispensable for miniaturized power supplies and their auxiliary systems, cannot be used in this battery technology to reduce the thickness. Therefore, although CVD can bring a great improvement to the performance of the battery, it seems that it cannot be further developed, and the technology is only used to process the positive electrode (TiS2).
Thin layers produced by physical vapor deposition techniques (PVD) require thermal evaporation and cathode atomization. Thermal evaporation battery technology is not the best way to manufacture electrode and electrolyte materials, as numerous compounds will partially or fully decompose as volatile elements are lost during thermal evaporation. The energy of evaporating particles is about tens of electron volts, which makes the adhesion to the substrate low, so it is not suitable for building a multilayer thin layer.
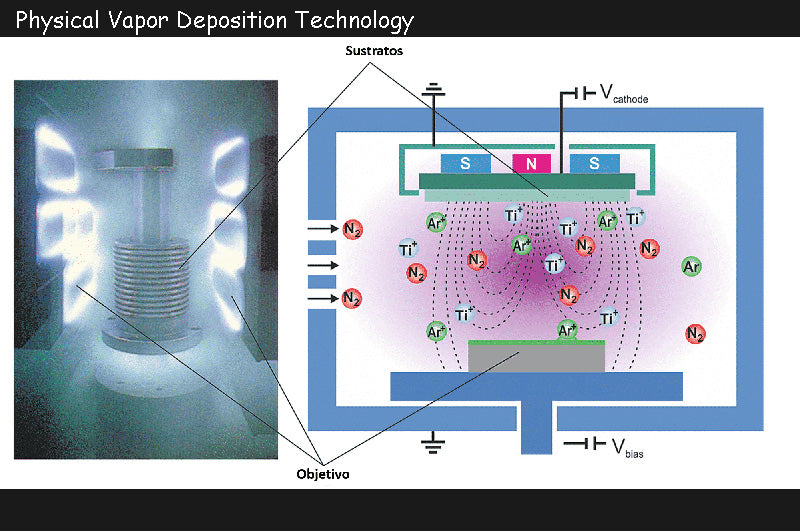
In contrast, cathode atomization battery technology is the method of choice for these applications, where the composition of the deposit tends to be very close to that of the target. Compounds such as oxides and sulfides are often available in an amorphous manner at room temperature, which is an important advantage for anodes. Due to the low density of the deposited material, the intercalated lithium will act as a homogeneous species without much dimensional change. This advantage allows the micro power supply to perform multiple charge and discharge cycles without damage. The energies of these particles are on the order of a few electron volts, allowing for good layer-to-layer adhesion, but occasional internal tensions that can cause tearing problems.
Since many materials are insulating or low conductive, RF cathode atomization technology can be used in conjunction with the magnetron effect for faster deposition rates and lower atomization pressure. Thereby, the quality of the thin layer will be improved, especially the porosity thereon will be lower. To prevent short circuits, the electrolyte membrane should be completely non-porous.
5. Printed battery technology
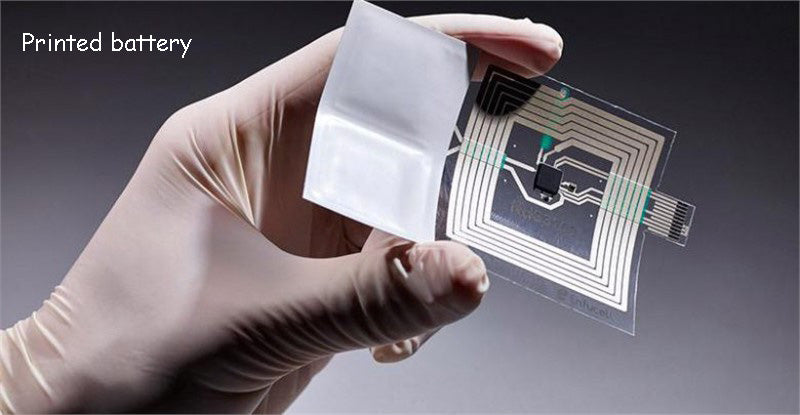
At least 1mm thick, ultra-thin battery technology can be well used in smart cards, RFID door cards, self-powered sensing systems, and smart packaging that requires external power supply; it can also be used in greeting cards, shopping cards, and even loyalty cards. Replace coin cell batteries in many applications. High-speed printed battery technology is the main method for making ultra-thin batteries, which enables thinner and more flexible products to be produced at low cost.
At present, most ultra-thin battery products use primary battery materials (non-rechargeable) such as MnO2/Zn (0.5mm thick), etc., with a capacity of 10~30mA·h and a lifespan of about 3 years. Blue Spark's carbon-zinc-based printed battery with a thickness of 500μm has an operating voltage of 1.5V (about 12mA·h capacity) and can provide a peak current of more than 1mA. Earlier, NEC developed an organic radical battery (rechargeable), but this battery can only provide a small amount of energy (about 0.1mA h/cm2), so when a larger capacity power supply is required application is restricted.
Finally, research and development work is underway on nano battery technology (some using carbon nanotube properties) and bio battery technology.
5.1 Lithium-ion printed battery technology
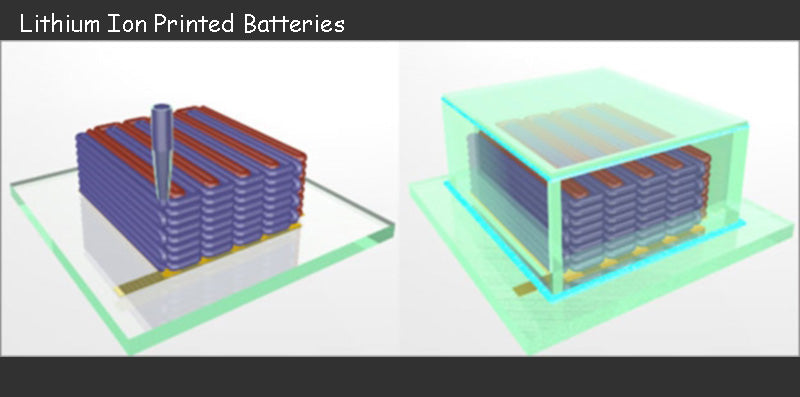
Due to the growing demand for autonomous power supply in practical systems, this requires a large number of innovative lithium-ion battery structures. Lithium-ion battery technology currently offers the best energy density and is dominating the power bank market. To make special batteries that are difficult to make with ordinary methods, one way is to use existing printing techniques to print electrodes to create the desired type of electrodes. This printing technology can reduce material loss, increase product yield, and make the manufacturing process more flexible.
At present, few well-known battery manufacturers have declared interest in this new method. CEA started the printing and preparation of this lithium battery technology in 2004, and in 2008 launched an ambitious European project with VARTA. The goal of this project is to print a complete lithium-ion battery directly on the device by means of a method that can only be achieved using printing technology.
Read more: Focus on Lithium-ion Battery Technology