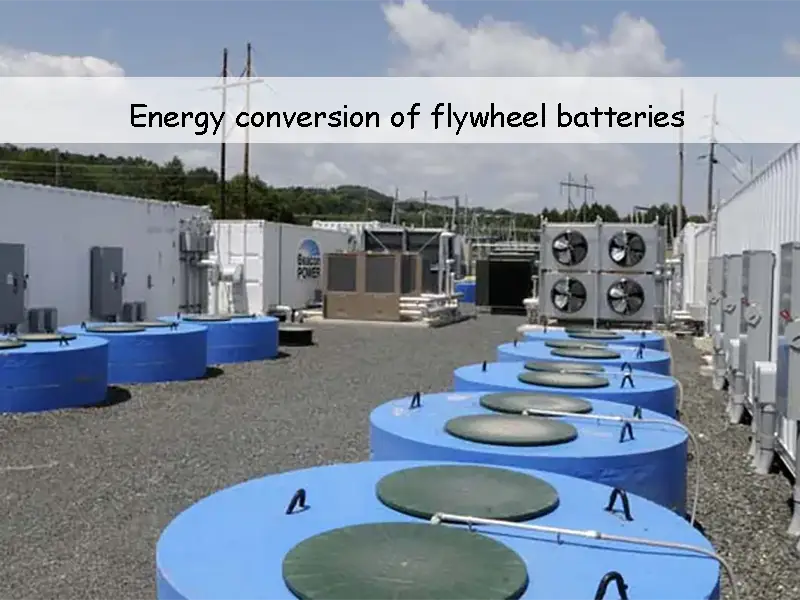
The motor/generator in the flywheel battery is an integrated component that mainly plays the role of energy conversion. When the flywheel battery is charged, it acts as a motor, converting the electrical energy in the mechanical energy of wind energy into the mechanical energy of the flywheel battery for storage, and when discharging, it acts as a generator. Converting the mechanical energy of the flywheel battery into electrical energy and outputting the flywheel battery as a high-speed motor should have both the characteristics of a high-efficiency motor and a generator. It is usually required to have the following characteristics as much as possible: large torque and output power; long stable service life; extremely low no-load loss; high energy conversion efficiency; can adapt to a wide range of speed changes. For flywheel batteries, there are currently five main types of motors to choose from, namely induction motors, switched reluctance motors, "write pole" motors, permanent magnet brushless DC motors and permanent magnet synchronous motors. A comparison of several available motor-related performance data is shown below.
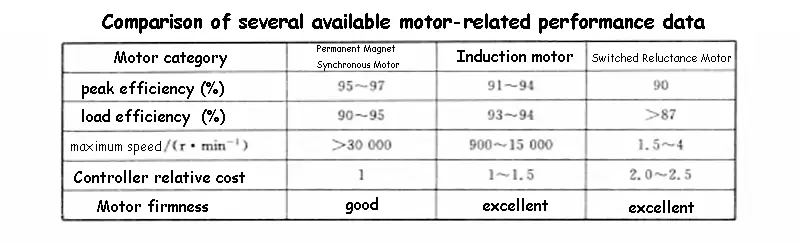
Compared with traditional DC motors, induction motors have many advantages: high efficiency, high energy density, low price, high reliability and easy maintenance. However, the disadvantages of induction motors are: the rotational speed cannot be too high; the rotor slip loss is large; the induction motor with a small number of poles uses a large amount of copper and iron to increase the weight of the motor.
The Energy conversion switched reluctance motor adopts a doubly salient structure. The flywheel stator adopts concentrated winding, and the rotor is not excited. Therefore, the rotor does not need maintenance, the structure is firm, it is easy to achieve zero current and zero voltage shutdown, and it is suitable for a wide range of speed regulation operation. The energy conversion brushless DC motor is to replace the excitation winding on the energy conversion DC motor rotor with a permanent magnet, and an electronic commutator is composed of a solid-state inverter and a shaft position detector. The position sensor is used to detect the position of the rotor during the movement, and convert the position signal into an electrical signal to ensure the correct commutation of each phase winding. When the energy conversion permanent magnet brushless DC motor is working, the square wave current is directly input into the stator of the motor to control the operation of the permanent magnet brushless DC motor. Its biggest advantage is that it removes the commutator and brushes in the energy conversion traditional DC motor, thus eliminating a series of problems caused by the commutation of the motor brushes. Another advantage of it is that due to the interaction of the rectangular wave current and the rectangular wave magnetic field, when the current and the back EMF reach their peaks at the same time, a large electromagnetic torque can be generated, which improves the load density and power density.
Energy conversion permanent magnet synchronous motor is actually a energy conversion permanent magnet AC synchronous motor. It replaces the rotor excitation winding of the separately excited energy conversion synchronous motor with permanent magnets, and inserts the magnets into the rotor to form synchronously rotating magnetic poles. The excitation winding, collector ring and brush are no longer used on the rotor to input the excitation current for the rotor, and the three-phase sine wave current is input to the stator. The motor has high energy density and efficiency, small size, low power consumption and fast response.
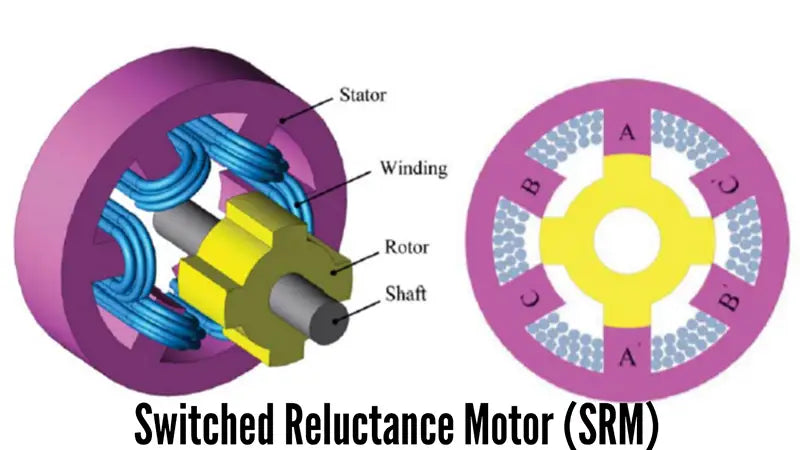
The "pole writing" motor is actually a pole-changing motor. A layer of hydromagnetic material is laid on the inner surface of the outer rotor. This layer of material is generally a highly anisotropic ceramic ferrite with a thickness of 15mm-50mm. Wait. In addition to the main windings arranged on the stator, concentrated excitation coils are also arranged around the excitation poles. As the motor rotates, this magnetic material can be magnetized by the field coil into any desired pole form. Therefore, the number and position of the magnetic poles of this type of motor can be continuously changed, which can realize fast start-up under the condition of small current, and realize constant frequency output under different rotational speeds. This feature is very suitable for wind power generation.
For the specific structure of the energy conversion flywheel rotor, it is impossible to make salient poles on it, thus ruling out the possibility of using a energy conversion switched reluctance motor. In addition, because the energy conversion induction motor can only operate reliably at medium and low speed, the possibility of using the energy conversion induction motor is also excluded. The working magnetic field of the permanent magnet brushless DC motor is a step-by-step rotating magnetic field, which is easy to generate torque pulsation and is accompanied by large noise. The working magnetic field of the permanent magnet AC synchronous energy conversion motor is a uniform rotating magnetic field, the torque ripple is small, and the running noise is also small, and it not only has the advantages of simple structure, reliable operation, and convenient maintenance of the AC motor, but also has the operation of the energy conversion DC motor. It has many advantages such as high efficiency, no magnetic loss, convenient adjustment and control, wide speed adjustment range, easy to realize bidirectional power conversion, etc. It is very suitable for use as an energy converter in flywheel batteries. Therefore, it is generally ideal to use a energy conversion water-magnetic synchronous motor as the drive motor of the flywheel battery.
Halbach arrays are actually ring-shaped gradient magnets constructed with multiple small magnets to create extremely strong magnetic gaps near the inner or outer edge of the ring. It was first proposed by Halbach, a physical scientist at Lawrence Berkeley Laboratory, and named after it. Halbach has formulated various electromagnetic system configurations, such as dipole, quadrupole and hexapole, and can easily calculate the magnetic field at any point in the air based on the calculation theory of the electromagnetic field of many-body annular gradient magnets.
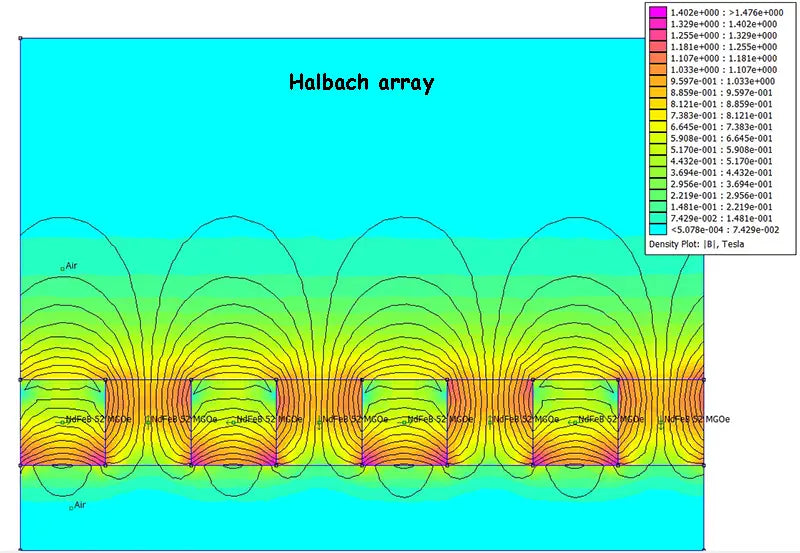
According to the energy converter designed by the Halbach array, since there is no need to install any iron core or yoke, there is no end load or unbalanced moment acting on the rotor or its suspension, and the external leakage flux can be ignored. There are no hysteresis and eddy current losses, and the rotor and stator air gaps do not need to be controlled as a critical dimension. By using Litz wire as the stator winding, the flywheel battery will have lower idle losses and higher efficiency.
Read more: Overview of energy storage devices