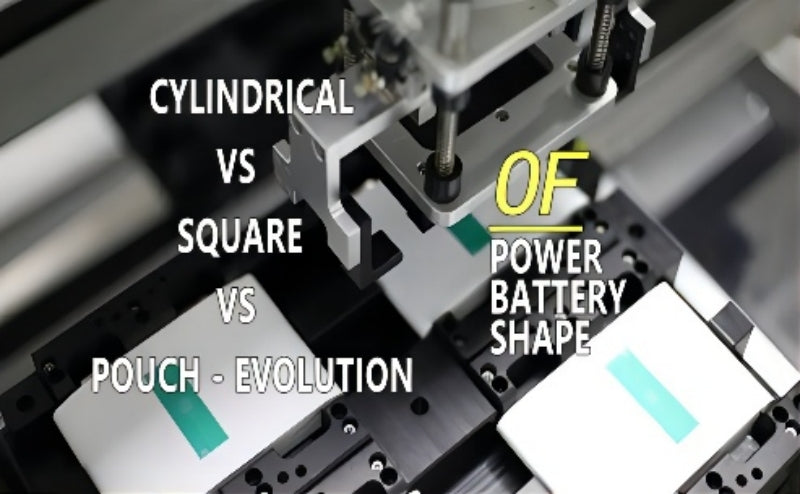
Main content:
- 1.Cylinder: Direct applications for 3C consumer batteries
- 1.Cylinder -- Tesla's first choice
- 2.Chinese cylinder battery adopts following strategy
- 3.Cylinder cell is difficult to pack
- 2.Square: China's mainstream car battery shape
- 1.From VDA to module 590
- 2.The development of square battery size in China is diversified
- 3.From making large cells to optimizing the structure
- 3.Pouch: Making it big is not easy
- 1.LG Chem -- The original pouch battery
- 2.The slow development of Chinese pouch battery represented by WANXIANG
- 4.Will the car battery become bigger and bigger?
Car power battery sizes are more varied. In 2017 alone, there were 145 types of product specifications and dimensions of power batteries for electric vehicles in China's national recommended standards. In contrast, there are 10 standard sizes of VDA in Europe, including 5 square cells, 1 cylindrical cell, and 4 pouch cells.
With the deepening of the cooperation between the battery industry and the automobile industry, the grasping of the scenarios and demands of the power battery for vehicles, as well as the introduction of high-standard battery manufacturing technology, there are several obvious trends in the form of the power battery:
The cell becomes larger: for example, the column evolves from 18650, to 21700, and then to 4680; Square batteries change either into long thin strips (BYD's blade battery and SVOLT's knife battery) or into thick, long squares; Pouch goes from applicable VDA module to MEB's 590 module...
Stronger structure: like Tesla 4680, as well as BYD, CATL, SVOLT's cell or adopt CTP, or even consider CTC, the cell becomes a structural part of the vehicle.
Energy density vs cost and safety: with the improvement of the range, car companies no longer blindly pursue energy density, but try to balance cost and safety consideration.
Why these trends? Will the cell keep getting bigger? This article will explain in detail the evolution process of power battery single specifications, and try to summarize the rules, to help us predict the future evolution direction of battery specifications.
1.Cylinder: Direct applications for 3C consumer batteries
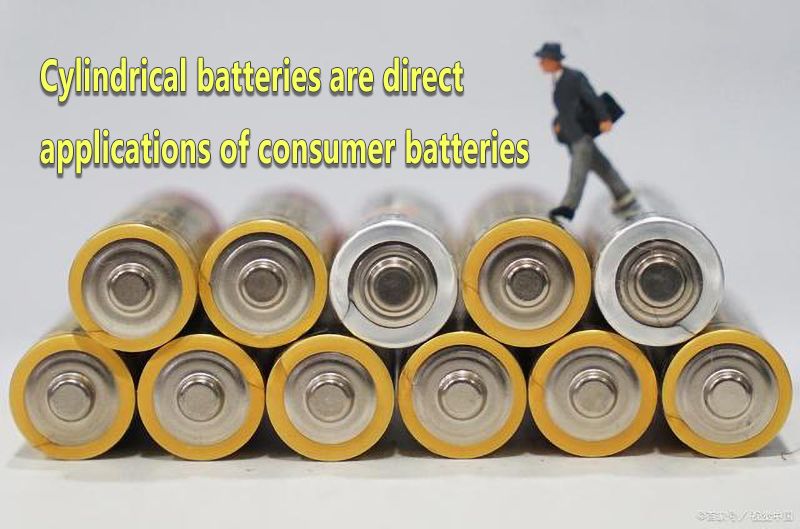
Electric cars were invented much earlier than petrol cars, but battery-powered vehicles were left behind by the rapid development of the internal combustion engine.
Still, automakers have never given up on electric cars. In the 1990s, Peugeot, GM, Nissan and others continued to experiment with battery-powered cars. In the 21st century, the preliminary competition has come to fruition. Nissan and Tesla are the only major automakers capable of mass producing electric cars. Nissan and Tesla, on the other hand, both started with cylindrical batteries as their preferred shape. Nissan's electric car comes to mind with the Leaf. In fact, an earlier Nissan electric car, called the Prairie Joy EV, also used cylindrical batteries, though not nearly as well known as Tesla's mass-produced Roadster.
Let's start with Tesla.
1.Cylinder -- Tesla's first choice
Tesla's first car, the Roadster, chose the 18650 battery with the best stability and cost.
In 1991, SONY invented the 18650 battery. It is the world's first commercially available lithium-ion battery. To save money, SONY designated the lithium-ion battery model 18650, with 18 being 18 in diameter, 65 being 65 in length, and 0 being cylindrical. Cylindrical cells are the oldest shape in the battery field, and their technology was the most mature and cheapest. The birth of this type of battery may be accidental, but with the explosion of 3C, small household appliances market, the popularity of this type has become inevitable. As soon as the model came out, it was mass-produced by major battery enterprises in Japan and South Korea and became one of the best-selling battery models in the field of consumer electronics.
Martin Eberhard, one of Tesla's founders, is a sports car enthusiast who also worries deeply about America's dependence on Middle Eastern oil imports and global warming. This eventually led him to cofound Tesla with Mark Tapenning. The two founders did not have the ability to research and produce batteries themselves, and their only choice was to select a suitable battery in the market. After many trials, they selected 18650 cylindrical cell. After careful comparison, Kurt Kelty, then Tesla's director of battery technology, decided that Panasonic's 18650 battery had the edge in energy density, cycle stability, and batch repeatability.
Panasonic, however, rejected Tesla, saying that consumer batteries could not be used in cars. Undaunted, Tesla assembled the battery cells and took them to Panasonic. After seeing the feasibility of the battery, Panasonic rejected Tesla's offer again, considering the safety risks posed by battery packs. It wasn't until Tesla came up with a cooling solution for the battery that Panasonic reluctantly agreed, but with two rules: 1. Tesla can't claim that its battery supplier is Panasonic; 2. No responsibility for any problems.
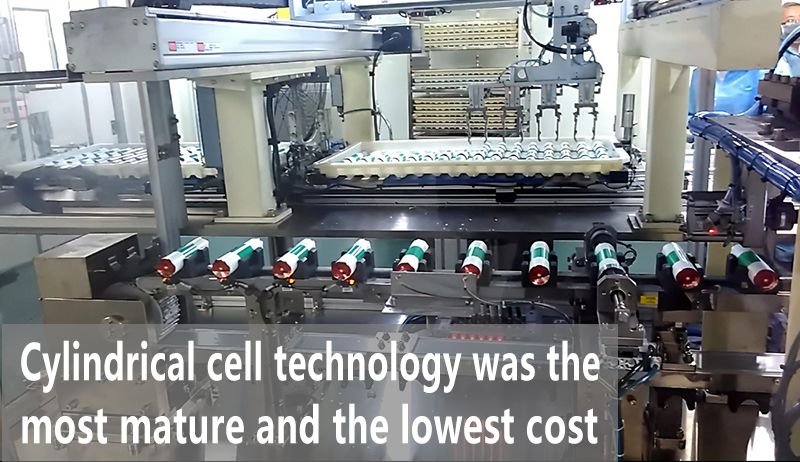
In 2009, Panasonic lost $4 billion on a failed bet on ion TVS. Panasonic, eager to pull itself out of the mire with new business, has cemented its willingness to work with Tesla. This tug-of-war shows that Panasonic doesn't think consumer batteries can actually be used in cars at all. Fortunately, Tesla's powerful battery assembly technology, basically achieve safety and performance, so that a success. As Panasonic's collaboration with Tesla deepened, the two companies began to make improvements in battery design and materials.
There's no doubt that the 18650 has a lot of room for improvement from the consumer battery. The simple logic is to enlarge the battery size to reduce the complexity of grouping and increase the energy density while maintaining the same yield. In addition, in terms of materials, the anode material is changed to silicon containing silicon carbon composite material to improve the energy density. Hence the 21700 battery, which is much fatter and slightly taller than the 18650. If 18650 can be compared to "primary school", 21700 has entered the "middle school" stage, and its volume, volume and energy density have significantly increased.
From the first quarter of 2016, the Gigafactory built in Florida, China, began to produce 21700. Panasonic supplied the cell exclusively for the Model 3. By adopting this battery cell, Tesla Model 3 effectively improves energy density and capacity, reduces the number of battery cells and PACK accessories, and lightweight upgrades drive down the cost and price of the vehicle. Panasonic's original 18650 battery for Tesla was limited by its size and key components, with a capacity of 2.2 to 3.6Ah, while the 21700 was capable of 4.8Ah, with a capacity of 5 to 5.3Ah. Compared to the 18650 battery, the 21700 improves the energy density by about 20%, approaching 300Wh/kg.
As Tesla grew bigger, Panasonic's production capacity and profits failed to keep up, and the two sides, already festering, squabbled. The tussle between Tesla and Panasonic hit the headlines in 2019. At this point, Tesla realized that relying solely on third-party suppliers might be difficult to keep up with their speed and cost requirements. Tesla's plans to develop its own battery have been accelerated by concerns over control of core components and increased bargaining power.
Unexpectedly, Tesla is not only determined to develop, and soon threw out the "king fried" level of products. In September 2020, Tesla unveiled the 4680 cylindrical battery at Battery Day, which increases the capacity of a single cell by five times compared to 21700. The cylindrical cell became "fat" again, only a little taller.
Compared with 21700,4680, the cost is further reduced, and the capacity and power are greatly improved again. In terms of cost, due to the reduction in the number of batteries required by the battery pack, the proportion of metal shell decreased, and the significant reduction in the number of structural parts and welds, the cost decreased, which is 14% lower than that of 21700 battery. In terms of performance, 4680 battery innovatively adopts the full pole ear technology to widen the battery current path, greatly reduce the internal resistance, reduce the internal loss, and then greatly improve the battery power, 6 times the 21700 battery.
On February 19, Tesla announced via its official social media platform that it had produced its one millionth 4680 battery in January.
Tesla CEO Elon Musk said on a conference call that the 4680 battery will be used in the first quarter of 2022 for the Model Y. In addition to Tesla, Panasonic, LG and other companies are developing and producing this type of battery to supply the world's largest electric vehicle company.
2.Chinese cylinder battery adopts following strategy
Tesla is not alone in experimenting with cylindrical batteries for electric cars.
In 1998, before Tesla was founded, Tianjin Lishen, an old battery company in China, had built a production capacity of 300,000 units of 18,650 batteries. However, at this time of production capacity, or for mobile phones and other 3C products. After seeing the success of Tesla's 18650 application, Chinese companies have also accelerated the application of the 18650. In 2012, Lishen 18650 cell took the lead in vehicle sales, carried in Jianghuai iEV2, only 100; In 2014, it began to be installed on Kandy. In 2015, the iEV5 of JIANGhuai was carried in batches.
At the same time, China's BAK battery also began to explore the application of 18650 batteries in vehicles. In 2010, BAK cooperated with Dongfeng to supply batteries for driving vehicles of Taiwan Flower Expo; In the same year, this battery cooperated with Beiqi Foton to become a demonstration model of new energy taxi in Beijing. In 2014, BAK achieved mass production of 2.4Ah cylindrical 18650 batteries. Under the background of China's vigorously promoting new energy vehicles, South Korean battery companies have entered China one after another seeing the business opportunities. In 2015, Samsung SDI also chose the 18650 cylindrical battery route in Tianjin and began to supply JAC motors in the following year.
After Tesla adopted the 21700, Chinese companies represented by Lishen batteries also began to introduce the model. Lishen's 21700 was first mass-produced in 2017 and carried on a pure electric logistics vehicle. At the same time of the rise of 21700 battery, enterprises represented by Guoxuan High-tech also developed 32131 and 32135 15Ah lithium iron phosphate cylindrical cell. At present, guoxuan High-tech 32mm diameter products are mainly used in baiC, JAC, Chery and other small cars. Later, under the guidance of Tesla, 4680 was also introduced into China. Ev Lithium, BAK and other enterprises are following this route, trying to supply Tesla or other large cylinder route car enterprises.
3.Cylinder cell is difficult to pack
Tesla, which makes the best use of cylindrical cells, also helped design the module for its first mass-produced Roadster. But Toyota itself chose to go in the direction of square cells rather than cylindrical cells. It can be seen that the small cylindrical cell is not the first choice of car companies. In China, only JAC motors is the most loyal user of cylindrical batteries.
A former CATL engineer said that in theory the cylindrical cell should be the cheapest solution, but it was difficult to assemble. Tesla was using the aluminum wire bonding process, which was mainly used in the electronics industry more than a decade ago, when no Chinese auto parts company could do it. At that time, the idea of the enterprise is to press an aluminum bar or bronze plate, and then press down the corresponding point of the bus bar corresponding to the pole point of the cell for laser welding with the cell, but this design is prone to miss welding or falling off. In fact, the car company can also let suppliers come up with a solution, such as using a multi-layer plastic frame to connect multiple cell ends into a long module. However, limited by the historical environment at that time, most of the designs did not make full use of the limited volume in the bag at that time, resulting in the advantages of cylindrical battery completely failed to play. Before 2015, China's car companies were relatively slow to respond to vehicle electrification and new energy vehicles, without serious research and improvement. At that time, the top executives of the car companies focused most of their energy on the profitable joint venture car field, and they did not have strong subjective initiative for political tasks such as new energy vehicles. In the case of small quantity at that time, suppliers are also difficult to cooperate, mold opening cost is very high, early completely can not be amortized out.
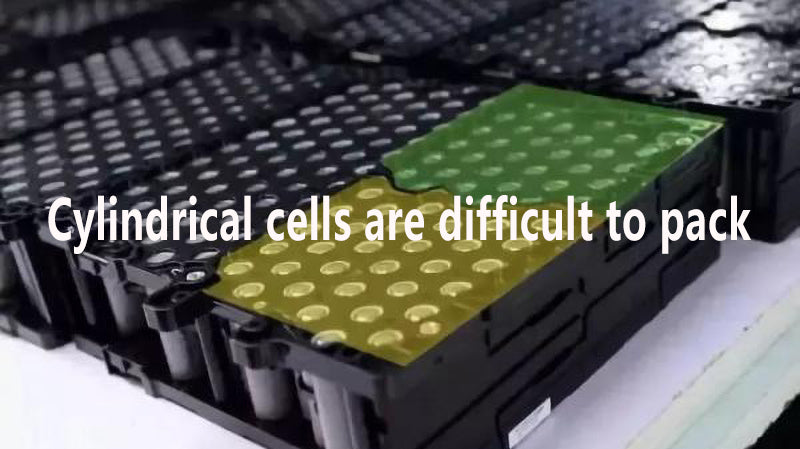
From 2012 to 2014, the number of new energy vehicles did not increase, the use of cylindrical battery electric vehicles did not do, only BAIC, JAC, Chery and other car companies made a little tentative use of cylindrical cell sample cars. When electric vehicles began to be mass-produced in 2016-2017, battery cells were monopolized by CATL and BYD for a variety of reasons, including policies and battery cell manufacturers. Cylindrical batteries have not been developed in the high-speed development period of China's electric vehicles. Another reason is that when cylindrical batteries are grouped, there will be a lot of "dead" space in battery arrangement, which is not conducive to the improvement of volume energy density due to low volume utilization efficiency.
Even now, the proportion of cylindrical batteries in The Chinese market is increased due to the application of Tesla. With the introduction of the Tesla CATL lithium iron phosphate square battery into Tesla, the proportion of cylindrical batteries fell back again.
2.Square: China's mainstream car battery shape
In addition to cylindrical batteries, square batteries also entered the automotive field early. Japan's Sanyo Electric may have been the first to make a dent in square batteries. In 1995, Sanyo Electric launched the square lithium-ion secondary battery, which is made of aluminum alloy and weighs about 30% less than the steel case. Because of their light weight, they are increasingly being used in products such as mobile phones.
In 2008, Panasonic acquired Sanyo Electric, which acquired the technology related to square cells. It's worth noting, however, that Panasonic is not exporting square battery technology to Tesla. In this regard, a battery enterprise related person in charge gave his view: "Cylindrical battery technology mature, high degree of standardization, square battery production is much more difficult than this." However, the person also pointed out that although square batteries are difficult to manufacture, they are relatively easy to assemble, so square batteries can grow into an important direction in the automotive industry.
1.From VDA to module 590
The square battery almost entered the automotive field at the same time as the cylindrical battery, but due to the lack of support from popular models, the early global progress of the square battery was not significant. In 2012, panasonic square batteries began to be adopted by Volkswagen, Toyota, ford and other enterprises, such as Volkswagen e-golf, e-up, golf GTE hybrid, Audi Q5 and A6 hybrid, Toyota eQ, Prius PHV1 generation, ford Fusion2 generation and other models.
One of Panasonic's earliest square cells, the 5Ah cell fits the VDA HEV's dimensions, which are 120*85*12.5.Toyota's Clarity PHEV uses panasonic's square battery, which also matches the size of the VDA PHEV2, and is much larger for plug-in models.
Samsung SDI has also mastered the square cell technology in the later stage. For example, the battery size of the matching BMW I3 model conforms to BEV2 in VDA size, which is 173*45*125. The development of Samsung's square power battery is similar to that of Japan's Panasonic, which is well accepted in markets outside China. Of course, the size of the square battery is also growing from small to large, mainly to the thickness and length of the continuous extension.
The idea of overall electrification in Europe is the process of battery enlargement step by step, following the development path of 48V, HEV, PHEV and then BEV.
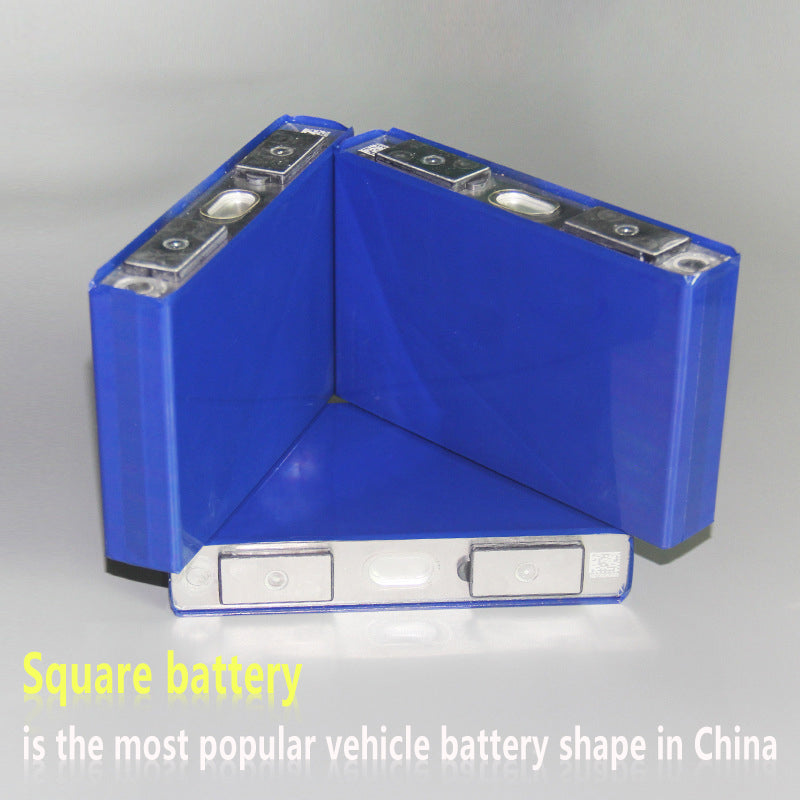
In the early stage of development, China used to learn from The European standard. Around 2012, with the launch of the European VDA standard size, Chinese car companies and battery companies began to learn from this standard. However, the maximum size of VDA is BEV2, and the maximum capacity of the battery under this size is 120Ah at present.
Currently, Samsung SDI is still making square batteries in accordance with the size of VDA. The development of square batteries in China has broken the standard of VDA size. This is because by 2017-2018, 120Ah capacity will no longer be enough to meet the needs of Chinese car companies. Global car companies are also considering the use of pure level platform, so that the battery breakthrough VDA size. Around 2017, Volkswagen began to consider the launch of pure electric MEB platform, launched the 590 module, for the further increase of the cell to provide conditions.
Make the square cell bigger, also become the direction of the global car enterprises.
2.The development of square battery size in China is diversified
The development of square batteries in China is another story.
The development path of BYD, CATL and Lishen represents the development path of square batteries in China. BYD started with batteries, and then began to make cars. Its battery design from the beginning to consider the battery and vehicle matching, and consumer battery migration to the vehicle path is completely different. CATL's automotive battery industry has many talents from BYD, so it has inherited some technology. Lishen square battery, is the global system vendors fancy, from the military battery to the automotive field.
BYD -- China's square battery leader
BYD started with batteries. In 2003, BYD's nickel-cadmium battery sales surpassed sanyo Electric, becoming the world's first.
Another goal of BYD founder Wang Chuanfu is to build electric cars. Just in 2003, while topping battery sales, BYD acquired Xi 'an Qinchuan Automobile Co., ltd. to form BYD Auto Co. After the establishment of BYD Auto Company, the establishment of electric vehicle departments immediately. According to public information, BYD started the research and development of lithium iron phosphate battery as early as 2002, launched the basic research of three-way battery in 2003, the first lithium iron phosphate power battery was listed in 2005, and the power battery was applied in e6 and F3DM dual-model cars in 2008.

In terms of batteries, BYD started to build batteries in the direction of automobiles, and the size of the battery cell exceeds that of other battery enterprises in the same period, such as F3DM, whose size is 356*100*28. As can be seen from the size, BYD's PHEV in 2008 (356*100*28) has already exceeded the size of the late VDA EV (173*115*45).
Compare that to the global market, where BYD built batteries specifically for electric cars into its vehicles in 2008, while Nissan, NEC and NEC Tokin have just set up AESC, a joint power battery company. BYD at this time in the development of power battery field, has been significantly ahead of the world.
Judging by the size of BYD's power battery, the idea is to make the cell longer.
CATL -- starts from VDA and breaks through VDA
BYD was CATL's teacher when it came to automotive power batteries: it had been working on them for about eight years when NEW Energy Technology (ATL, which CATL hadn't spun off yet) got involved in 2010. But unlike BYD, CATL's cell is mainly expanded along the VDA size. In 2010, BMW first approached ATL with a battery size of 173*115*45 for the VDA EV2. Of course, at this time VDA cell standards have not been released. Industry insiders revealed that the project was sheet metal and square battery, which was directly changed on the fuel vehicle platform. Three packages were plugged in the vehicle gap, with more than 400 kilograms of battery, but the driving mileage was very low, and the weakness of lithium iron phosphate battery was exposed. Around 2012, independent CATL made a second project for BMW -- BMW X1. The size of the electric cell given by BMW is 173*92*21, which is close to the size of VDA PHEV1.
As China's national policy began to tilt toward commercial vehicles, plug-in hybrid, pure electric commercial vehicles more and more. BYD's electric buses carry 150-300 KWH of electricity. BYD K8, for example, uses a lithium iron phosphate battery with a charge of 270 KWH.
CATL cell family
With such high electricity, Yutong sought cooperation with CATL. However, CATL's first model for Yutong was an HEV with a 13-degree charge and a sheet metal frame to hold the battery cell. CATL carries 173*45 batteries for Yutong buses, with a height of more than 200, which is roughly the same size as VDA, but has made a breakthrough. Overall, CATL's battery was still smaller than BYD's cells at the time.
Lishen -- the follower of the square battery
At the same time Lishen Battery, another early Chinese lithium-ion battery company, is also trying to use square cells in electric cars. Lishen's square battery was developed from the early regimental radio stations. Zou Yufeng, deputy general manager of Lishen Battery, recalled that miles Electric Vehicle Company of the United States discovered lishen's battery at that time and hoped to cooperate in developing the battery for use in cars.
Myers and Lishen first approached in 2008 and formed a joint venture in 2009.
"The battery in the battalion radio was about 27 by 70, and it got taller on the car, from 60 to 120, to 27 by 70 by 120." Zou yufeng said, "The elevation is based on the bottom design, and there is still space left. In order to make full use of it, the elevation is 120."
The collaboration with Miles didn't work out as expected, but Lishen is using the square cells in its cars in China.
3.From making large cells to optimizing the structure
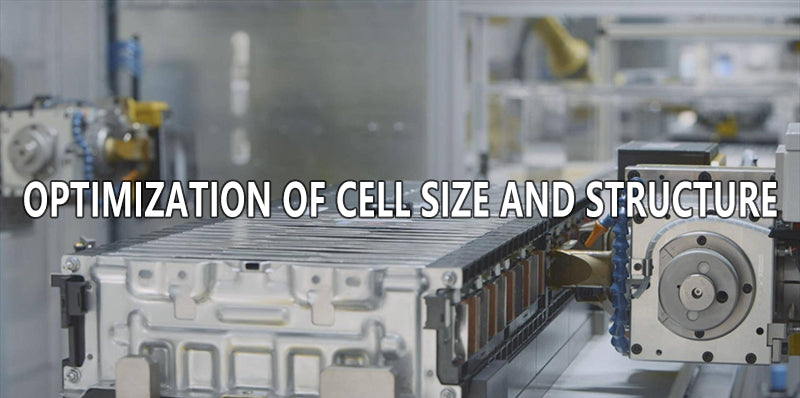
Whether BYD, CATL or Lishen, in the process of the development of new energy vehicle industry, have embarked on the road of cell size and structure optimization. Under the pressure of China's new energy vehicle subsidies on energy density requirements, battery enterprises through the normal chemical material system development, NCM111 -- NCM523 -- NCM622 -- NCM811 to iteration is completely too late, the optimal way is to optimize the structure.
For example, to raise the height of the cell, generally the shoulder height of the battery is 91, and the height of the module is about 108. Much of the 10 mm is wasted. On BEV, more space can be left by simplifying the control board, from 91 to 95, and then to 102, which is the general direction of the evolution of the cell in China.
The other direction is to make the coil core in the battery larger. For example, there are two coils in one cell. In the later period, the coil core is enlarged to make only one coil core, which can also improve the energy density. As a representative example, in 2019, CATL supplied NCM811 battery for GAC AION.S, with a size of 79*148*103; The corresponding size of VDA is 26.5*148*91, CATL has expanded in the height and thickness of the cell, especially in the thickness, reaching the industry often said 3 times the thickness.
In contrast, in 2021, Samsung SDI will still have 61.5Ah, double the thickness of the battery cell for BMW. Chinese enterprises took the lead in breaking through the constraints of VDA size. Under the extension of this idea, in 2019, China'S BYD launched blade battery and CATL launched CTP structure, both of which are further enlarged cells and continuously simplified module structure.
However, BYD and CATL have similarities, but also differences. CATL has two development directions. One is to gradually improve the thickness and height of the cell, and the length starts from the VDA size of 100+. The second is to elongate thin, for example, for NiO 100 degrees of electricity to do the cell length of 250. BYD's idea is to adhere to the battery do long thin, starting is 300+.
BYD was able to make such a size cell because of the autonomy of its vertical industrial chain, which developed its own equipment to support the production of such cells. CATL's production equipment mainly depends on outsourcing, the equipment capacity of suppliers and CATL's own consideration of the utilization of old equipment, which also limits its ability to make large cells in one step. Looking back at BYD's manufacturing capabilities in power batteries, its technological lead is due to equipment that can produce batteries in-house. And its precision manufacturing capabilities, and from the mobile phone contract manufacturing business. BYD, after all, was the first to enter the mobile-phone contract manufacturing business a year before it bought Qinchuan Motor in 2003. BYD electronics technology is used in two out of every 10 mobile phones worldwide.
Have to say, BYD vertical industry chain integration ability, to ensure its leading position in the industry. The innovative BYD and CATL have led the industry through the continuous iteration of the square battery. At this time, China's square battery, has gone ahead of Europe.
3.Pouch: Making it big is not easy"
There is also another direction for the in-car power battery, called pouch. The pouch battery, which is also known as lipo battery, was first developed by SONY in 1990. SONY began development of the battery in 1994, and the pouch has been in use in cars since 1998. However, the pouch battery has been popularized by Korean battery companies, notably LG Chem.
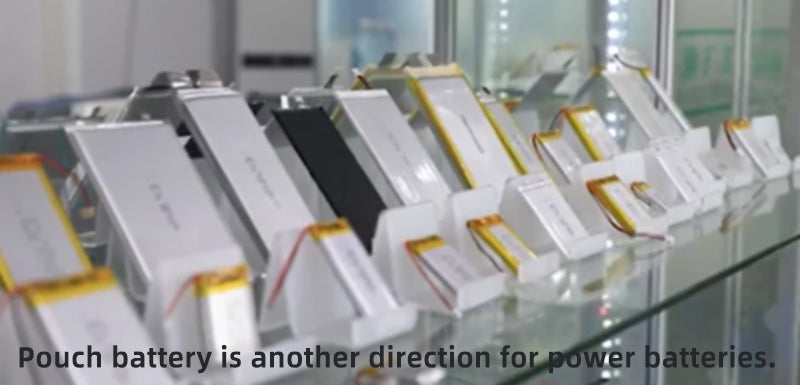
1.LG Chem -- The original pouch battery
LG Chem is also a latecomer in the field of lithium-ion batteries. It started lithium-ion battery development in 1995 and produced the world's first PHEV pouch cell, LMO/NCM111, in 2010 and BEV pouch cell in 2011. LG Chem also has round, square, and pouch shapes for its battery. However, FOR automotive applications, LG Chem chose pouch. Pouch the pouch is limited by the aluminum-plastic membrane, which makes the cell both wide and flat. In 2010, LG Chem successfully developed the first PHEV pouch cells, built an integrated manufacturing center in the United States, and began production of BEV pouch cells in 2011. LG Chem has a deep history in the materials field, including its extensive accumulation of aluminum plastic film, which may be the reason why it chose pouch path. LG s main sizes are 159*11.3*290.5, 159*11.5*290.5, and 99.7*11.3*301. However, to match the VW MEB platform's 590 module, LG also made an elongated cell, with the longest side approaching 550.
The world's flagship pouch battery manufacturers include Korea SKI and Japan's AESC. Pouch is characterized by relatively flexible dimensions, but not easy to make large. Pouch cell is limited by aluminum plastic film, so it is difficult to make a breakthrough in thickness, and the length is limited by production process, which also has a great bottleneck. Pouch cell length to 500-600 has reached the limit, longer, even if the production process does not come to the account, the pass-through rate will be significantly reduced. Even for LG, the Pouch is only 600 in length.
2.The slow development of Chinese pouch battery represented by WANXIANG
One of the early representative enterprises of pouch battery in China is Wanxiang one Two Three. In 1999, Wanxiang began to develop and produce pouch power battery for vehicles, but it was after the acquisition of A123 in the United States that wanxiang made a breakthrough. Wanxiang founder Lu Guanqiu first came into contact with A123 at the Shanghai World Expo in 2010 and was impressed by its excellent product performance.
It should be noted that At this time, Wanxiang Group has entered the auto parts industry for more than 30 years, and entered the power battery research and development field for 10 years. After investing 1 billion DOLLARS in research and development, its products are still far inferior to A123. Therefore, Lu guanqiu often lamented that A123 was the world's leading lithium battery and energy storage core technology at that time.
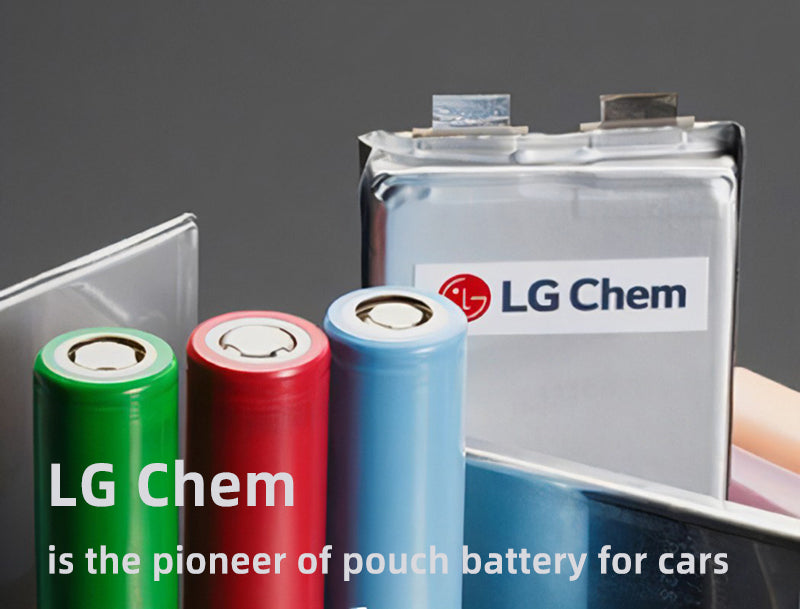
But specialties such as A123 can also fail. In 2012, A123 suffered a massive recall and was taken over from bankruptcy by Wanxiang. Subsequently, by virtue of A123 Lithium iron phosphate technology, Wanxiang 1123 Occupies more than 50% of the global share in the automotive low-voltage 48V field. Universal pouch in automotive high voltage, the route is three-way pouch. According to a person close to Wanxiang 1223, the Universal Pouch cell was relatively diversified in size around 2010, mostly based on the customized cells of customers in the Chinese market. Due to the differences in the chassis of customers from oil to electricity, the diversified size advantages of the Pouch were fully played and the pouch could quickly adapt to the market demand.
Later, Wanxiang 123 made its 48V low voltage the largest share in the world, and its size of 160*220 48V cell gradually became the mainstream and was used in many pure electric models in China. With the popularization of VDA355 module in 2015, the cell length of Wanxiang is gradually closer to it, with a size of about 355*100; In 2018, module 590 became popular, and Wanxiang also developed a battery cell suitable for module 590, with a size of about 590*100.
If the length of the cell is more than 600, the yield and cost can not be well balanced, and it needs to continue to improve the cell design, process and equipment. Because pouch cell capacity is not easy to enlarge, pouch should be connected in parallel in the vehicle, which requires more heat dissipation and fixed support. In addition, pouch does not have mechanical strength, so there will be more and more accessories in the group process. The advantages of pouch's high energy density will be completely offset in the group process.
Farasis Technology and JEVE Power are also representatives of the Pouch cell in China. However, in the early days of China, there were few enterprises that could perfectly solve the production process and group problems of pouch cell, so the power battery was almost monopolized by the square battery. At present, the Pouch battery of LG is mainly used as a supporting device. GM, Honda, Ford, Daimler, Nissan Renault, Volvo and other automotive companies have widely applied the pouch battery, but only a few enterprises in China have applied the pouch battery. The biggest advantage of the pouch cell is the single cell application. The pouch is the best solution for mobile phones or laptops, but not for cars.
In the short term, pouch battery technology is largely ignored by Chinese automakers. However, it is interesting to see whether pouch battery technology can regain its vitality in the solid-state battery field in the future.
4.Will the car battery become bigger and bigger?
Looking back over the course of power battery development, it's easy to conclude that batteries seem to be getting bigger as they become more compatible with vehicles. However, in a relatively micro time scale, automotive battery technology is still in the stage of a hundred flowers blooming, it is difficult to say that the mainstream technology now will be mainstream in the future. For example, one of the current technological routes is the change brought about by the leapfrog development of voltage platform: voltage platform leaps from 400V to 800V; However, the total electric quantity of vehicles develops at a step of every 10 KWH, and the increase of electric quantity fails to keep pace with the increase of voltage platform.
The impact of this unsynchronization is that, under the current 800V platform, the series number of the cell is increasing, which to a certain extent squeezes the space for the growth of the cell volume. Therefore, the cell volume will shrink in a certain stage.
According to the current technical level, under the ternary system and 400V system of passenger cars, the 285Ah cell (250.3*66.72*112) of NiO's 100kwH model may be the largest size. Under 800V system, ultra-long range vehicles with more than 1000 km are not made. That is, according to the calculation of maximum 150 KWH electricity of single vehicle, the maximum capacity of single volume is about 200Ah, and the typical size of CATL is 54*174*201.
Overall, the development direction of the power battery cell size is ultimately the result of the balance of technology, cost control and manufacturing system. It is difficult to simply say that the development direction of the cell is getting bigger or smaller.
But it is certain that with more and more automobile enterprises understand battery, as well as battery enterprises more and more understand the car, through continuous run-in and adjustment, the future will have more suitable for the car cell size birth.