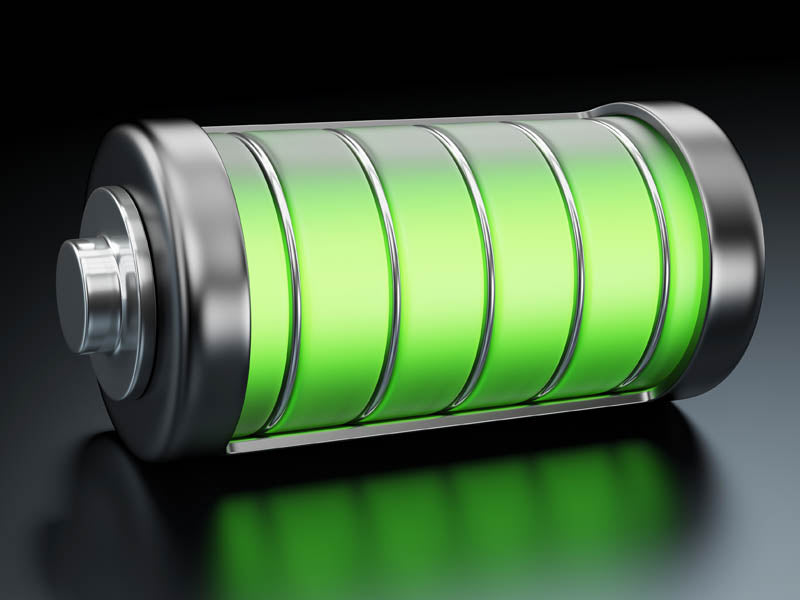
Main content:
1.Ni-Cd chemical batteries
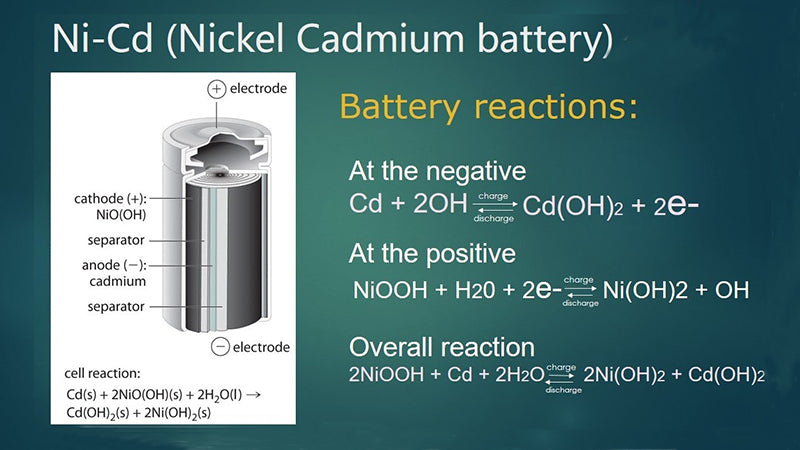
Nickel-cadmium chemistry, as we know it today, originated in 1899 and is one of the oldest battery technologies in history. The anode is chemically impregnated nickel and the cadmium cathode is plastic molded from a steel base. The separator is a non-woven fabric and the electrolyte is an alkaline liquid. The single cell is enclosed in a polypropylene case.
Nickel-cadmium chemical cells consist of cadmium electrodes and NiOOH in a concentrated potassium hydroxide electrolyte. The chemical reaction equation during discharge is as follows:
In industrial applications such as electric traction, nickel-cadmium chemical batteries need to be water-cooled or air-cooled and regularly maintained every 50 to 100 charge-discharge cycles. The specific energy of nickel-cadmium chemical batteries are 55W·h/kg, and the specific power can reach 100~135W/kg.
Nickel-cadmium chemistries are rated at 1.2V, but fluctuate between 1.15 and 1.45V depending on the state of charge.
Nickel-cadmium chemistry batteries can be fully discharged multiple times without damage, and have good ambient temperature adaptability to work in cold environments. Compared with lead-acid chemistry, nickel-cadmium chemistry is stronger in construction, lighter in weight, and more resistant to overcharge or overdischarge. As a result, cadmium chemistry has a longer life and requires less maintenance.
However, the nickel-cadmium chemical batteries also have certain shortcomings, its cost is about 5 times that of the lead-acid chemical batteries, the cycle charge and discharge efficiency is lower (Faraday efficiency is 70%), and the self-discharge rate is also higher than that of the lead-acid chemical batteries. (>15%). Nickel-cadmium chemistries have a memory effect, which is related to the pot negative (so it's best to do a full discharge before recharging the jinjin battery).
Compared with NiMH chemistry, NiCd chemistry has a stronger peak current discharge capacity (over 10 times), but its self-discharge rate is also higher than NiMH batteries. This battery technology will be phased out due to environmental pollution. Today, in the field of energy storage, nickel-cadmium chemistries have been replaced. Nickel-metal hydride chemistry replaced nickel-cadmium in 1990 and is now competing with lithium-ion chemistry.
2.Ni-MH chemical batteries
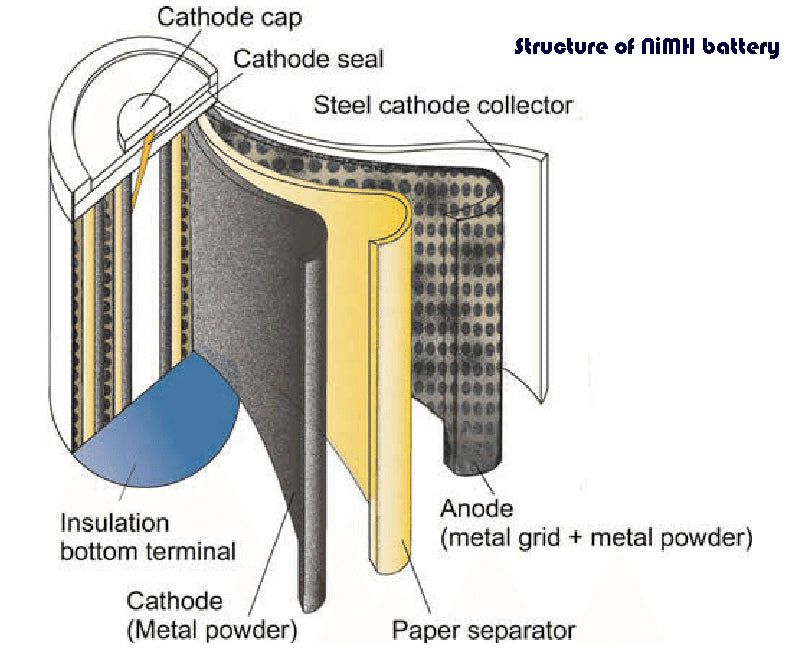
NiMH chemistries have demonstrated good performance at room temperature and are pollution-free compared to lead-acid chemistries and nickel-cadmium chemistries. It works in a similar way to nickel-cadmium chemistry.
The rated voltage of a single nickel-metal hydride chemical batteries are 1.2V, its specific energy is 40% larger than that of a nickel-cadmium chemical batteries, and the memory effect is small due to the inhibition of the negative separator.
The characteristic of the end of charging of NiMH chemical batteries is that the charging voltage will have a very small decrease (dv/dt), and high-performance automatic chargers can use this characteristic as the basis for stopping charging.
The design of bipolar nickel-metal hydride batteries originally originated in the United States. This battery module consists of laminated battery cells. The technology effectively exploits the chemical, thermal and electrical properties of conductive plastic films. Current flows through the cell interface perpendicular to the electrodes. The electrodes are manufactured using a unique compression molding technology, which enables NiMH chemical batteries to have higher specific capacity. There is also a nickel-metal hydride chemistry battery that does not contain diamonds in the positive electrode because it is believed that diamonds do not play a role in the battery pack. In fact, the drill can be used to control the release of oxygen when the battery voltage is too high.
3.zinc chemistry batteries
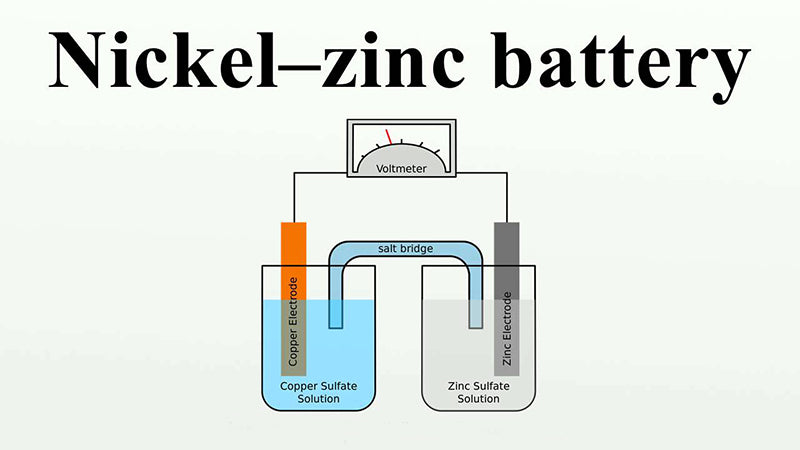
Zinc-based chemistries, such as nickel-zinc chemistries (Ni-Zn) and silver-zinc chemistries (Ag-Zn), operate in alkaline environments, where compounds are easy to recycle and raw materials are readily available. Zinc chemistry batteries have a wide range of applications, from consumer electronics to military or aerospace systems.
Compared with the nickel-cadmium chemical batteries, the nickel-zinc chemical batteries have a lower price and a 25% higher available voltage, but its charge-discharge cycle capability is poor (600~1000 times). The chemical reaction equation of the nickel-zinc chemical batteries are as follows:
Nickel-zinc chemical batteries are one of the few batteries that use water electrolyte, but can work at a voltage higher than water splitting, which is related to their thermodynamic properties. At the same time, zinc has a high theoretical capacity, which can reach 820A·h/kg. In addition, abundant zinc content, low cost, and non-toxicity are all advantages of zinc chemical batteries, and also the reason why a lot of research on zinc chemical batteries is currently carried out in the industry. However, one of the main problems encountered is basically how to improve the cycle performance of zinc electrodes in an alkaline environment, including the formation of crystals and the redistribution of large-scale zinc. In order to overcome the above problems, the industry has introduced some solutions. We are particularly concerned with those chemical cells in which the electrolyte is immobile, the main purpose of which is to limit the dissolution of zincate formed by the reaction of zinc under alkaline conditions. To achieve this, solutions of low concentration (<5M) potassium hydroxide have been employed, containing additives such as fluorides, phosphates, carbonates, etc., which form insoluble compounds with zinc. At the same time, lime was added to the active electrode to form calcium zincate, which was stable and insoluble when the concentration was lower than 7M.
To delay the increase of zinc exfoliated dendrites formed upon charging, multilayer microporous separators or even ion exchange membranes are often employed. Although different solutions improve the lifetime of chemical cells (about 200 cycles), problems such as increased internal resistance, reduced power and energy densities, and increased cost arise from this, especially for multi-layer microstructures. The introduction of pore separators or ion exchange modalities destroys the nickel-zinc system.
In the early 2000s, the American company Evercel built a large-scale industrial production capacity of nickel-zinc chemical batteries, initially in the United States, but quickly transferred to China. The technology is based on a low-concentration lye solution and uses calcium zincate activator (US Pat. No. 5,863,676) and a multi-layer diaphragm, but its cycle life hardly exceeds 300 cycles. Other U.S. companies with nickel-zinc technology are Evionyx, through its subsidiary Xellerion, which has launched the chemical batteries that include an ion-exchange membrane (US Patent 7,119,126); PowerGenix is developing the Sub C-type nickel-zinc chemical batteries for portable electronic devices, through Fluorides, borates, phosphates, etc. are added to improve the performance of alkaline electrolytes and reduce the solubility of zinc compounds (US Patent 2006207084).
Nickel-zinc chemical batteries have the characteristics of energy-based energy storage and power-based energy storage. According to the current development level, their performance has been superior to nickel-cadmium chemical batteries and nickel-hydrogen chemical batteries, and can withstand high-rate charging and discharging. Nickel-zinc chemistries are rated at 1.65V and have comparable cycle life to nickel-cadmium chemistries, but nickel-zinc chemistries have lower self-discharge rates and memory effects. Nickel-zinc chemistries are durable, stable, and require little maintenance (water-tight) during operation. Compared with other alkaline chemical batteries such as Jin-cadmium and Ni-MH, nickel-zinc chemical batteries are cheaper to manufacture and contain no heavy metals, and waste batteries are easy to recycle. However, the chemical batteries technology still need to be tested in practice, which is why its products have not yet been applied on a large scale.
4.Sodium-sulfur chemical batteries
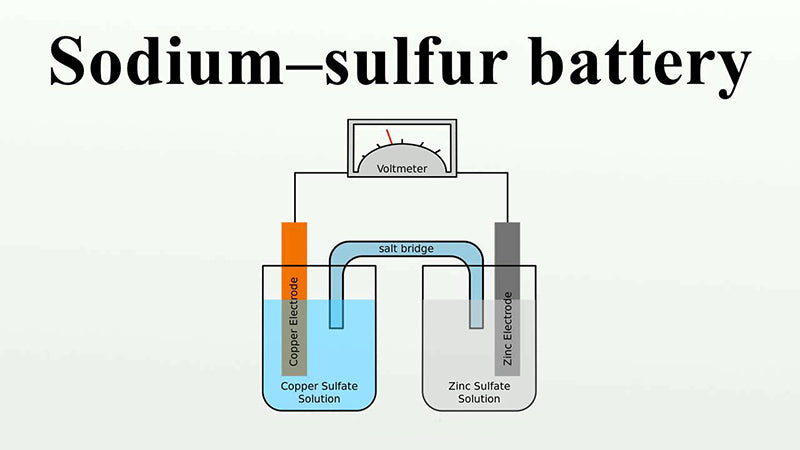
Sodium-sulfur chemistry cells are typically placed in cylindrical containers filled with sodium and sulfur on the outside. The two materials are separated by a ceramic dielectric (beta-alumina), and the entire system is packaged in a steel composite can. Sodium-sulfur chemical batteries need to operate in an ambient temperature of 300°C. Its energy density is about 100W·h/kg, and the power density is about 230W/kg, which is three times that of nickel-cadmium chemical batteries.
Considering the possible high risks of this battery technology, it is generally only used in stationary applications.
5.Redox (Flow) Chemical Batteries
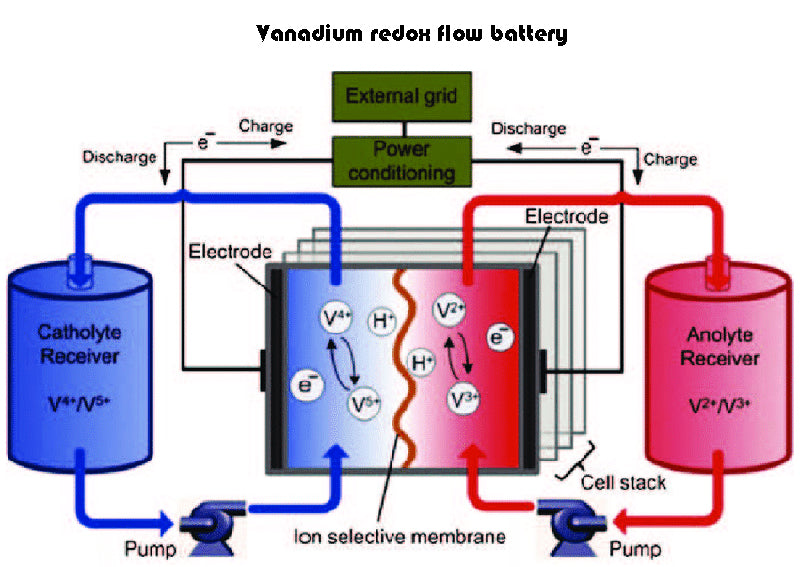
Compounds participating in chemical reactions are dissolved in the electrolyte of the redox chemical batteries, and the electrolyte needs to be continuously circulated. Several Australian compounds are used in flow batteries, such as zinc bromide, sodium bromide, and more recently sodium/bromine polysulfides, which are very popular. The electrochemical reactions flowing through the separator in flow batteries are reversible (charging and discharging). A large container is used to hold the electrolyte, so that a plurality of battery cells can be combined and applied, and a larger storage and release capacity can be obtained. For example, in 2003, Regenesys technology company in England developed a set of energy storage system using the above method, the capacity of this energy storage system is 15~120MW. But for now, vanadium batteries dominate the battery family, with an overall energy storage efficiency of about 75%.
6.Zebra Chemical Batteries

Sodium Nickel Chloride Chemical Batteries (Na-NiCI2), which can operate at high temperature (300°C), with a rated voltage of 2.58V. The negative electrode is composed of liquid sodium, and the positive electrode is bromine chloride. During charging and discharging, sodium ions can separate sodium from chloride through the ceramic electrolyte. The system is housed in a metal box that serves as the negative terminal. This type of battery can generate 8.5~130kW·h of energy, of which the energy density can reach 85W·h/kg, while the power density is between 72~130W/kg depending on the cooling method. This type of chemical batteries have a cycle life of 1000 cycles at 80% depth of discharge. This type of battery is still in the research and development stage, and the high temperature operation and potential risk of breakage limit its large-scale application. However, the battery is safer than sodium-sulfur chemistry.
7.Zinc-air chemical batteries
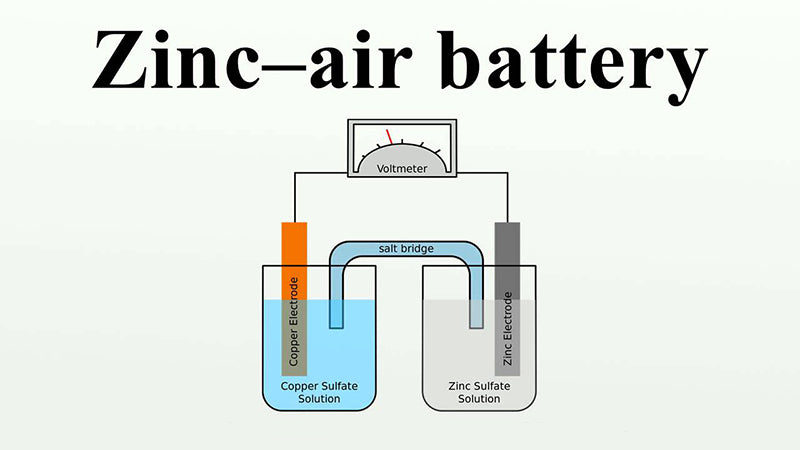
A variety of metal-air battery products have been around for decades, from small button cells to electric fences used in livestock enclosures and large cube batteries that can last for months. Metal-air batteries are well known.
Metal-air batteries are obtained by using metal particles suspended in an electrolyte, such as powdered zinc suspended in a bell solution, which flows and circulates in a bundle tube with an external air electrode. Such batteries can generate the high current densities that drive the power demands of electric vehicles. However, metal-air batteries (zinc or aluminum) require many precautions during operation. Nonetheless, the fast recharging capability makes it attractive in applications such as electric vehicles.
It can be seen that it is very likely that nickel-metal hydride chemical batteries and zinc-air batteries will be installed on electric vehicles in the future. The nickel-metal hydride chemical batteries provide peak current demand and realizes braking energy recovery during braking, while the zinc-air battery meets the energy demand for long-distance endurance (1000km or more). Toyota announced in 2008 that it was seriously working on the battery technology that could power future long-range electric vehicles.
The success of a metal-air battery depends on multiple factors, including the choice of metal or metal alloy for cycling, control of the air electrode (where research lags behind fuel cells), miniaturization of hydraulic systems and single cells, system thermoelectricity The feasibility of repeated charging is achieved by controlling and filling with new suspended metal particles to avoid changes in the transition properties of the electrolyte after discharge. Rechargeable metal-air batteries under development use high-energy-density metal oxide materials such as zinc or aluminum. The cathode (air electrode) of a metal-air battery consists of a porous carbon structure or a metal grid impregnated in a certain catalyst. The electrolyte can ensure the smooth passage of OH- ions, both liquid and solid (the polymer membrane is saturated with KOH). The metal-air battery has a cycle life of about 100 times and an overall efficiency of about 50%. The energy density of zinc-air batteries can reach 450W·h/kg, while the energy density of aluminum-air batteries is expected to exceed 550W·h/kg. Once the charging technology for metal-air batteries matures, this battery technology using high-energy-density, low-cost materials will be very attractive.
Read more: What is the battery application?